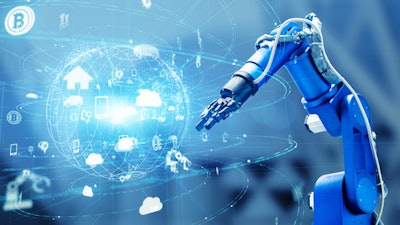
Companies are stuck with the warehouses and infrastructure they have. Very few can afford to immediately purchase new space when interest and sales pick up and there is a desire for increased production. This means working with what you have and finding ways to wring every last piece of efficiency out of the space you are currently in.
But, that’s often easier said than done.
If you’re looking to increase production and get more out of less, then it’s highly likely that you don’t have the resources to dramatically invest in new equipment that would increase throughput and ability to do more in less time. There may be some investments and upgrades you can afford that would help, but you need to find other complimentary areas to invest time and resources in that might have the payoff you’re looking for.
Optimization is critical
Optimizing the factory floor or assembly line sounds like a buzzword - that is, until you actually take a moment to step back and look at your specific situation. When trying to do more with less, it is an excellent first step to review daily operations, so you understand all of the critical processes.
Part of this is not just becoming an expert on the ideal situation (when everything goes correctly and flows smoothly throughout the day), but also the situations when everything goes wrong. When there are errors, shutdowns or unplanned downtime, what has happened to cause these situations? Are there repeated patterns that come to light that you either want to promote or eliminate?
Reviewing the entire operation, down to each detail, will improve your ability to cut down on everything from collisions to miscommunication to basic human error. Sometimes it’s as simple as remembering to locate goods in a reachable location, making sure the path to bring a package to shipping isn’t obstructed or making sure a robot doesn’t interfere with another robot (or a human) in their workflows.
There are software solutions that can solve collision problems for your operation right away, and proper planning and simulation will enable a team to better identify and respond to issues, such as ensuring that emergency equipment and shutdown buttons are located conveniently.
So, the question of “is your operation optimized?” is actually a good one to start with. Sometimes the smallest changes are missed when managing day-to-day operations, and often these can make a big difference in efficiency, throughput and ability to quickly bounce back from downtime.
Click here to hear more about robotics in the supply chain:
Focus areas
Once you've completed the overall review of the factory floor or assembly line, there are still a few key ways to optimize or upgrade existing operations that can make a real difference. These include:
● Simulation. Simulation can be a powerful tool when looking to optimize a retrofit or upgrade of operations. You can utilize software solutions that simulate downtime and recovery using a digital twin of the factory floor. The right software can help you test out different reasons for downtime, as well as to see how different solutions could solve the issue. If you upgrade as much as possible based on what you find to be the most efficient simulations, then you can be sure you’ve done as much as possible with your current environment. Simulation also enables the team to create a plan of attack for every possible disaster scenario, giving what you need to train your team so they’re ready to react at a moment’s notice.
● Synchronization. Another way to improve operations is through better synchronization. Take a moment to review that all critical technology has been set up correctly. Are your robots calibrated and workcells well-defined? Are there updates or upgrades needed? Ensuring your robots, other equipment and the software that runs them is in lockstep will help you get more out of your existing operations.
● Coordination. Improving the robot-human coordination in your line or on the floor can help ensure operations are moving at the highest speeds possible. When looking to get more out of your current facility and equipment, better coordination between humans and robots is an easy place to see real improvement. Robots are very good at some tasks, where human capabilities are required for others. Allowing robots and humans to work together on tasks allows for high throughput while keeping the human touch that is needed for the more involved operations. To make this work, robots need to be able to understand exactly where the human is at any given time and plan around the human should the human enter the robot’s workspace. Stopping at any time a human is near a robot isn’t a great solution because the stops and starts of the robot will have negative impacts on speed and throughput. Look to software solutions that can help robots adapt to their locations in real-time.
● Monitoring. Ongoing monitoring of floor operations or assembly line is critical to ensuring you have optimized all aspects of your operations. Proper monitoring can help you ensure things are running correctly and that there are no problems, but can also help identify any areas where additional efficiencies can be implemented. Perhaps there’s the opportunity for an additional robot. Or to move and adjust equipment that seemed to run well on paper, but in real life, can see another solution. In addition, the most important part of mitigating a shutdown is identifying it early and getting to it before it becomes a problem. Monitoring can help prevent this.
It’s the nature of business to want to get more from less, even when it’s not seemingly possible. While it’s true that most in the manufacturing, logistics and supply chain industries are locked in to their current facilities for a portion of time, that doesn’t mean that nothing can be done to make the best of that situation. By reviewing your factory floor or assembly line layout and looking for ways to optimize how you work and how efficiently you do so, there are ways to increase uptime and throughput - maybe even opening the door to investing in additional robots, equipment and physical space.