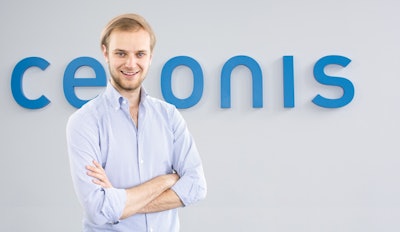
The Geodis 2017 Supply Chain Worldwide Survey collected responses from more than 600 supply chain professionals in 17 countries, and the results painted a clear picture of an industry in desperate need of visibility.
Consider the following: when polled, only 6 percent of managers reported having complete visibility across their supply chain, and 77 percent of respondents indicated having no visibility or restricted visibility. In parallel, those same respondents named “data analysis” as the No. 1 technological priority critical to their departments’ success. Put the two together, and you get a pretty good idea of what these experts already know: analyzing data leads to improved visibility in the supply chain.
The now-famous “productivity frontier,” outlined by Michael Porter in his landmark 1996 essay “What is Strategy,” conceptualized that a rise in overall operational effectiveness raises the competitive bar for everyone, and yet benefits no one in particular. In light of recent technological advancements, which have been adopted across industries, the productivity frontier has expanded quickly, and it stands to reason that supply chain objectives have had to shift from cost savings to value creation. In short, supply chain priorities have shifted from saving money to creating a seamless customer experience which, addresses customer demands.
So, what happens when you give supply chain managers better visibility? According to survey results you end up with improved risk mitigation, better flexibility, a higher percentage of on-time and in-full deliveries, happier customers, and significantly improved profitability.
How to Increase Visibility
Continuing with the theme of a customer-centric supply chain model, consider modern consumer expectations. As a customer, most people expect full visibility from the moment they place an order. Companies like Amazon empower end consumers with information from inventory levels to warehouse departure timestamps, all the way up to delivery confirmation. In theory, shouldn’t supply chain professionals have even more visibility in their day-to-day than end consumers?
These managers have a defined responsibility to improve visibility into inventory and the velocity of inventory movement, but they don’t have nearly as much visibility into operations as they might hope. In reality, supply chain professionals have really only scratched the surface of driving processes towards the desired state, and there’s plenty of room for increased efficiency and compliance within business processes.
Supply chains have always been driven by quantifiable key performance indicators (KPIs), but companies only recently began incorporating big data analytics to better understand the complex business processes in place. Emerging analytic technologies have allowed organizations to make more informed decisions, sifting through the massive amount of data being collected to uncover hidden patterns, correlations and customer preferences. But a key limiting factor of traditional analytics is that they’ve always required the business to have a hypothesis about where they want to look and what they want to investigate. Thanks to a new form of big data analytics called process mining, that’s about to change.
What is Process Mining?
Think of process mining as a MRI for business processes. Powered by artificial intelligence and machine learning, the technology leverages the digital footprints that processes leave behind in their IT systems, and provides complete transparency into how processes are working in real life.
For supply chain professionals, this means having access to a visual reconstruction of the entire organization’s business processes. Supply chain professionals can visualize and analyze how well their logistics and supply chain operate, in every variation of the processes—from order entry, all the way to cargo delivery. Process owners can see how efficient (or inefficient) their distribution network is, and identify any causes of delays. Process mining quickly and easily pinpoints larger systemic weaknesses in order processing, but can also drill into granular details like vendor data and invoice tracking.
A Common Application of Process Mining
A common area where supply chain professionals are facing challenges is with the establishment of a stable supply chain that ensures fast, on-time and in-full delivery to customers. When companies cannot deliver on their promised delivery dates, the impact is clear: customer satisfaction declines, as does customer retention. However, there can be many potential root causes across the supply chain that drive up long wait times.
Imagine a company that runs a global supply chain with a large number of product variations and local market requirements; the task of identifying the exact problem and understanding the root causes for late delivery can be enormous. There could be issues in production, logistics or order handling process, driven both by internal and external factors—production plant with quality issues can cause a lot of rework, a logistics provider can deliver too late or an order is stuck in an internal approval process.
Eventually, the problem becomes visible when customer satisfaction goes down and churn increases, but management wouldn’t have any idea of the scope and impact of exact process inefficiencies unless they were first aware they should be looking for it.
Ultimately, process mining is applicable to any process, and is not limited to the supply chain. Unlike with traditional analytics, process mining allows process owners to find and eliminate inefficiencies and errors in the transactional process and monitor compliance, production and supplier performance in real-time. The added visibility allows organizations to improve performance metrics and reduce throughput times by finally shining light on the inner workings of their business processes.