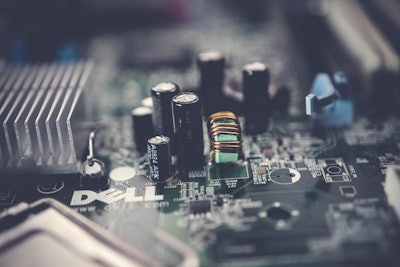
The recent pandemic created new challenges and disruption for all manufacturers, but it forced mid-sized manufacturers to address unique challenges created by significant supply chain disruptions. Manufacturers had to adapt to quickly working with limited personnel and the aging out of talent to keep up with demands. Luckily, the recent advances in technology include lower costs and improved access to the Industrial Internet of Things (IIoT).
Many large manufacturers boasted big budgets and more resources to help operations during this unexpected disruption; even small manufacturers were not facing the same experience as their mid-sized counterparts. Due to the global health crisis, many companies are refocusing their efforts on two fronts, first building resiliency into their organizations, and second, improving overall agility to address supply chain challenges, both on the vendor and customer sides. Prior to this disruption, many mid-sized manufacturers felt that Industry 4.0 was only meant for large-scale manufacturing operations. Mid-sized manufacturers allocated resources to pressing needs that delivered benefits today instead of the looming unknown tomorrow.
One of the benefits of 4.0 are smart analytics. This is important for manufacturers because every operation cannot afford machine downtime or poor quality. The analytics should deliver product quality test results and equipment statuses for operators to review at the end of the shift (or immediately if things are out of spec). With Industry 4.0, any detected issues can instantly be directed to an operator or maintenance staff. Unfortunately, many manufacturers who have not embraced Industry 4.0 keep this data in excel or paper notebooks, which prevents it from being used as actionable intelligence. In the face of disruption, Industry 4.0 can be used by mid-sized manufacturers to deliver better quality products while increasing production efficiency on the factory floor. So why haven’t the majority of mid-sized manufacturers already transitioned to smarter operations with Industry 4.0?
- Costly upgrades. It is a common misconception that upgrading current machinery to Industry 4.0 can be costly and unattainable for mid-sized manufacturers. Recent technology has introduced sensors that capture machine metrics from older machines that do not have this pre-existing technology. These sensors capture real-time data by recording cycle time, temperature, vibrations and other machine variables to improve processing efficiency. This means that older machinery without the technology for smart analytics can be upgraded to Industry 4.0, which is more affordable than replacing all older machinery. Industry 4.0 should provide continuous improvement by utilizing these news sensors to give manufacturers actionable intelligence. A good partner for Industry 4.0 will use the pre-existing machinery to save your operation money and time during an upgrade.
- Change is challenging. There is another misconception that Industry 4.0 is only meant for large scale manufacturers with significant amounts of money and resources that can be dumped into Industry 4.0. Due to this, many mid-sized manufacturers thought that smart manufacturing was not the right fit for their production floor, but Industry 4.0 can be the right fit for any mid-sized manufacturer. To successfully move toward Industry 4.0, your team needs a leader, a culture of continuous improvement, a willingness to be open to change and a good team to support your company through this development.
- Transition speed. The third and final misconception of Industry 4.0 is that many mid-sized manufacturers believed the entire production floor would require an overhaul all at once. Actually, the most beneficial way to transition to Industry 4.0 is by targeting and modernizing specific pain points. An appropriate Industry 4.0 solution should utilize measured sprints that can be anywhere from 90-120 days to correct the biggest pain points on the production floor in a step-by-step process. Any change in production should be tracked so machine operators and management can have easy access to this information in a smart way to demonstrate competency from these sprints.
As mid-sized manufacturers modernize in this new landscape, they must be open to change. It is important to note that implementation of technology could cause employees to feel like supervisors are trying to look over their shoulder during work tasks. In contrast, to attract the younger generation mid-sized manufacturers are better served by providing devices (e.g. tablets, monitors, dashboards) that are familiar. This can actually help build a healthy workplace culture which is important to smooth over any factory-wide changes including the aging out of critical talent.
What is the next big disruptor?
That’s the fun part -- no one knows. For mid-sized manufacturers, Industry 4.0 brings increased production efficiency, streamlined workflows, reduction in errors, real-time data for analysis and proven ROI. This revolution in technology helps manufacturers utilize actionable data to predict machine downtimes or processing inefficiencies. While implementing Industry 4.0, your team should have transparency into the processes, improvements and benefits that are delivered to the company. This should help mid-sized manufacturing teams stay prepared for future potential disruptions.