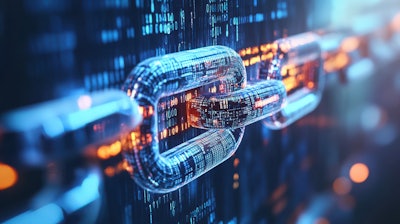
In 2023, 5,283 workers lost their lives on the job in the United States. While this is a slight decrease from last year's 5,486 fatalities, the reality is stark: a worker dies every 99 minutes from a work-related injury.
For too long, the supply chain industry has accepted a reactive approach to workplace safety as the status quo. We investigate incidents after they occur, implement corrective actions, and then turn our collective attention to other initiatives until the cycle repeats. This approach isn't just failing today’s workers—it's failing many businesses.
The most progressive supply chain organizations are embracing a shift: moving from a reactive response after an incident has already occurred to proactively - and systemically - preventing risks before they turn into incidents. And this transformation isn't just about deploying new technology—it's about reimagining how we approach workplace safety altogether and recognizing it as a strategic business imperative.
The true cost of reactive safety
When discussing workplace safety costs, many supply chain executives focus primarily on direct expenses: workers' compensation claims, medical costs, regulatory fines, and legal fees. While these costs are significant, they only represent a fraction of the total impact.
The indirect costs of workplace incidents often go unrecognized but can be up to ten times greater than direct costs. To name a few:
● Productivity losses: When an incident occurs, operations slow or stop entirely. The inevitable investigation consumes management time, while the injured worker's team is disrupted and has decreased efficiency.
● Replacement and training costs: Temporary workers typically require significant training investment while delivering lower productivity, especially in specialized roles.
● Equipment and product damage: Incidents often result in damaged equipment, product loss, or quality issues that ripple through the supply chain.
Yet, the most overlooked costs are those that affect the organization's long-term financial health:
● Insurance premium increases: A facility with a poor safety record can face significant premium increases annually.
● Talent acquisition and retention challenges: Organizations with poor safety records struggle to attract and retain talent, especially among younger workers who prioritize workplace wellbeing.
● Customer confidence and contract implications: Major retailers and manufacturers increasingly include safety performance in their supplier evaluation criteria, directly affecting contract renewals and business growth opportunities.
● Delivery delays and service disruptions: In just-in-time operations, incidents that cause delays can trigger contractual penalties and damage customer relationships.
The technology-enabled proactive revolution
Technology has evolved to make proactive safety not just possible, but highly accessible. Computer vision (CV) technology can observe operational environments 24/7, identifying risk factors and their potential to result in incidents. Unlike traditional monitoring approaches that rely on manual observation or post-incident review, modern systems can detect unsafe behaviors in real-time, such as improper lifting techniques or PPE non-compliance, identify environmental hazards like spills, blocked emergency exits, or unstable material stacking, recognize patterns of near-misses that human observers might miss, and even provide alerts to supervisors when interventions are needed.
What's transformative is how artificial intelligence (AI) then analyzes this vast amount of collected data, identifying trends across time periods, shifts, and locations that would be impossible for humans to process manually – turning thousands of safety observations into actionable intelligence. More powerful still, these AI systems continuously learn and improve, not just from a single environment but by incorporating insights from hundreds of similar operations across different sites and industries, creating a collective intelligence that far surpasses what any individual safety program could achieve on its own.
The most sophisticated systems utilize predictive analytics to identify patterns across operations, shifts, and locations. This allows safety leaders to address systemic issues rather than just individual behaviors. For example, if analytics reveal that near-misses consistently increase during shift transitions in multiple facilities, this points to a systemic opportunity for improvement.
The value of these technologies isn't just in identifying more risks, it's in reducing the monitoring burden on safety teams and on-site leaders. Instead of trying to be everywhere at once, balancing competing priorities, safety professionals and leaders can focus their expertise where it's most needed.
From cost center to value driver: Changing how to measure safety
Perhaps the most significant shift in progressive supply chain organizations is how safety performance is measured and valued. Traditional metrics like Total Recordable Incident Rate (TRIR) or Days Away, Restricted, or Transferred (DART) are lagging indicators—they tell us how we performed in the past but offer little insight into future performance.
When measured properly, proactive safety approaches deliver benefits far beyond incident reduction:
● Operational efficiency gains: Organizations often discover that addressing safety risks simultaneously improves process efficiency by reducing unnecessary movement, streamlining workflows, and eliminating redundant steps.
● Quality improvements: The same conditions that create safety risks—rushed work, procedural shortcuts, improper equipment use—also lead to quality issues. Addressing these root causes improves both safety and product quality.
● Workforce engagement: When workers see risks addressed before incidents occur, it demonstrates organizational commitment to their wellbeing. This builds trust and improves overall engagement.
● Compliance readiness: Proactive organizations find themselves better prepared for regulatory inspections and changes in compliance requirements, reducing the resource drain of crash compliance efforts.
Safety implementation strategies for supply chain leaders
While the benefits of proactive safety are clear, implementation requires thoughtful planning. Successful organizations typically focus initial efforts on high-risk areas like loading docks and material handling zones, while integrating safety as a priority in all operational reviews. Progressive supply chain leaders must cultivate a culture that embraces technological innovation and proactive thinking. The key is creating accountability at every level, balancing technological solutions with human expertise, and addressing change management through transparent communication and frontline involvement.
Looking ahead, the evolution of proactive safety will become the standard for high-performing worksites. Organizations that remain stuck in reactive approaches will find themselves at an increasing competitive disadvantage—not just in safety performance but in operational efficiency, talent acquisition, and customer relationships. The gap between innovation adopters and laggards will only widen as technologies like CV and predictive analytics become more sophisticated and accessible.
The most forward-thinking supply chain leaders are already asking different questions. Instead of "how do we reduce incidents?" they're asking "How do we transform our workplaces into environments where we catch and neutralize risks before they evolve into incidents?" This fundamental shift in thinking represents the future of supply chain safety.
For executives still viewing safety primarily as a compliance requirement or cost center, the time for reevaluation is now. The technology exists. The business case is clear. The only missing piece is leadership commitment to transform how we approach workplace safety in our supply chains. Leaders who recognize safety technology as a strategic investment rather than an expense—and who actively champion innovation in this space—will not only protect their workforce but position their organizations for sustainable competitive advantage.