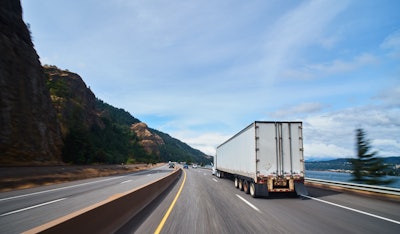
Global supply chain concerns have escalated through the pandemic, geopolitical tensions, and the rapidly declining availability of nonrenewable resources. The consequential delays and shortages consumers are experiencing call into question whether our supply chains have truly been built to last. Incentive programs, allocating bigger budgets towards product transportation, and strategic stockpiling have all been floated as viable solutions. But at the end of the day, these are ultimately temporary patches that won’t be able to fix an intractable problem.
Instead, the answer lies with leaders, who must embrace change and redefine how things are done. Just as a home’s plumbing and electrical systems must be properly set up to avoid dangerous situations, a company’s supply chain must have the right foundation. Here are three ways that leaders can reimagine supply chains and strengthen organizations along the way.
Focus on opportunities, not threats
A company can achieve unprecedented growth through a “volunteer army” that has been encouraged to solve problems and pursue individual passions for the greater good of their company. To keep them motivated, it’s important for leaders to address challenges as new opportunities for innovation, instead of potential roadblocks. Shift rhetoric away from “threats” so employees can see problems as solvable. And when those problems are solved, make a point of celebrating them publicly to show proof of progress and maintain morale.
Reframing threats as opportunities does not have to mean relentless optimism. Acknowledging that a situation will be hard to fix can earn a leader more respect than trying to hide behind fake positivity. Be up front about the challenge but also convey why you believe the company can overcome it – together. A timeless example is the chemical company DuPont’s reaction to a limited supply of rubber from Asia during the Great Depression. Employees were encouraged to find alternatives and eventually developed a way to engineer their own synthetic rubber, which then became used for a range of products – from neoprene and military supplies to women’s pantyhose.
Enlist leaders at every level
The interconnectedness of our global supply chain has made it simultaneously more efficient and more vulnerable. Because smaller mishaps aren’t always reported or widely communicated, it can be hard to grasp the full extent of the damage for weeks or months. By that time, your pipes have burst, the basement is flooding, and the only option is to rip out the walls.
We need to begin rebuilding our supply chains before the pipes begin to burst. Doing so will require a massive amount of support from many people working together to drive the process forward. Leaders need to empower employees at all levels and create diagonal leadership, which encourages collaboration and input from employees across a range of title levels so that there is strength throughout the entire supply chain.
With a culture of diagonal leadership, leaders can more easily cultivate a devoted “volunteer army,” comprised of people who are more willing to collaborate and tackle challenges together. They will be more willing to work on-site, jump into projects in separate departments because they want to (not because they have to), and voluntarily offer their unique insights. A house reinforced from top to bottom is less likely to fall than one that has a strong roof but weak walls.
Make the switch from “survive” to “thrive”
Supply chain difficulties and any number of other (perceived or real) catastrophes can send the human brain into “Survive” mode, a mechanism triggered by threats that increases blood flow and prepares us for “flight or fight.” It is most often characterized by “negative” emotions like anger or anxiety, rapid problem solving, and a spike in energy intended to help us eliminate the threat. However, remaining in Survive mode is unsustainable and limits our ability to think broadly or creatively. Soothe Survive by bringing your company’s primary concerns into focus and solving them, while eliminating the flurry of activity that might be happening around less critical threats (or things that aren’t actually threats). In other words, don’t redo the entire electrical panel when all you really need is to change a few light bulbs.
Leaders can then trigger “Thrive” mode by presenting employees with new opportunities that inspire passion and active engagement. The Thrive channel triggers “positive” emotions like excitement and pride, which help mitigate fear and prompt us to pursue the opportunity. Thrive is much easier to maintain in the long term, provided that clear progress is made toward achieving a goal and positive emotions remain high. This is possible by encouraging innovation (even if it requires a degree of risk), touching hearts through more positive communications, and always finding ways to talk about opportunity.
Today’s business and work environments have been significantly altered since the onset of the Covid-19 pandemic. Remote or hybrid work is the new norm, workdays look different, and everyone is trying to adjust to a rapidly changing world. Businesses are still emerging from a state of fear and uncertainty. Despite it all, supply chain leaders have a unique chance to rebuild a crumbling process from the ground up. Empowering leaders at all levels, focusing on opportunities, and tapping into “Thrive” will be the key to creating a better system for everyone.