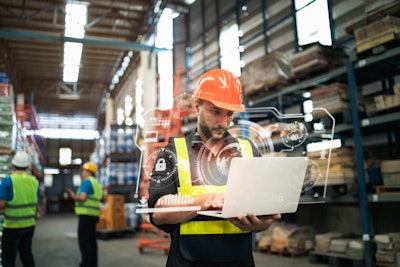
In today's always evolving manufacturing landscape, maintaining a skilled workforce is a serious challenge, especially in light of a Bureau of Labor Statistics report that saw a staggering 53% annual turnover rate in warehousing, transportation, and utilities sectors. While the labor market has shown some improvement since 2022, the challenge of keeping warehouses fully staffed with competent employees remains difficult.
If you’re a manufacturing or distribution leader, your first thought might be to invest heavily in automation technologies like autonomous robots and artificial intelligence. Certainly, these kinds of solutions can reduce the need to hire additional workers or replace those that leave. However, they also usually require substantial capital and a significant amount of time to implement them. Warehouses need to make the most of the labor they have right now. In the short term, manufacturers and distributors can take advantage of their enterprise resource planning (ERP) system to boost efficiency and mitigate the impact of high turnover rates.
By focusing on improving warehouse efficiency, companies can achieve multiple benefits. First, they can reduce the need for additional staff and when employees leave, if efficiency is high enough, they may not need to be replaced — in fact, taking the following measures could reduce attrition because greater efficiency will reduce pressure and improve employee satisfaction. Additionally, warehouses can increase order fulfillment accuracy, improve on-time delivery rates and, ultimately, increase profitability.
Let's explore four cost-effective strategies that warehouse managers can implement quickly to enhance efficiency:
- Optimize Warehouse Layout
The way in which you organize the physical layout of your warehouse can significantly improve productivity. Consider the following steps:
- Engage your warehouse staff for improvement ideas: Your pickers and other warehouse workers live the current processes and undoubtedly have ideas for how systems could work more efficiently. Not every idea will be a good one, but it’s well worth considering their thoughts.
- Implement a clear and logical labeling system for bins, aisles, and rows: Large signs with easy-to-read letters and / or numbers that progress in a systematic way can make it much easier for pickers — especially new pickers — to find exactly what they’re looking for. Some have created systems so effective that they decided they didn’t need to invest in a warehouse mapping solution.
- Designate separate areas for raw materials and finished products: We all know how chaotic things became during and immediately after the pandemic. Inventory was put wherever there was space for it. But the supply chain has (mostly) recovered, and if you’ve not cleaned things up, it’s time to do so.
- Utilize vertical space and mobile shelving units effectively: Use mobile units to store seasonal items, which can be moved out of the way and efficiently stored until the time is right. Stackable containers can augment capacity without consuming floor space.
- Arrange inventory based on picking frequency and order patterns: The fastest moving inventory should be the easiest to access. Additionally, if items are often ordered together, group them all nearby one another in the warehouse.
One manufacturer with whom I have worked with reorganized their warehouse layout according to these suggestions and reported a 33% increase in usable pallet floor space.
- Streamline Picking Processes
Even without a sophisticated Warehouse Management System (WMS), you can improve picking efficiency with a few simple systems:
- Sort packing slips as soon as they are printed by bin location: Pickers will spend less time traveling across the warehouse to fulfill their slips
- Consolidate multiple orders into single pick lists where possible: Fewer trips means less wasted time
- If you have a WMS, enable suggested picks to support practices like first-expire-first-out (FEFO): This is particularly helpful in the food industry for avoiding spoilage
These simple changes can significantly reduce the time and distance pickers need to travel, improving overall efficiency.
- Upgrade Barcode Scanning Technology
While older scanning devices may still function, modern handheld devices can load pick lists in seconds rather than minutes. This seemingly small improvement can add up to substantial time savings across multiple pickers and shifts. For example, let’s stipulate that a new bar scanner loads 30 seconds faster than the current set. That may seem insignificant, but if you multiply this by 30 lines of 20 pickers across two shifts, you’ll see 10 hours of time savings every day, and 50 hours each week, which is more than one FTE!
Moreover, newer devices often support additional features like lot tracking and picking suggestions, further enhancing efficiency.
- Implement Real-Time Pallet Tracking
For warehouses with a high number of SKUs but low volume per item, locating specific products can be time-consuming. By leveraging your ERP system and investing in RFID tags or IoT sensors, you can implement real-time pallet tracking. This allows for faster item location, improved sales order staging and enhanced theft prevention.
The implementation of these four strategies doesn't require a ton of time or much in the way of financial resources. With strong leadership support, most warehouses could put these changes in place within one to two months. So, while the challenge of high turnover in warehouse operations is significant, it's not insurmountable. By focusing on these practical, cost-effective solutions, manufacturers and distributors can not only mitigate the impact of labor shortages but also create a more efficient, accurate, and profitable operation.