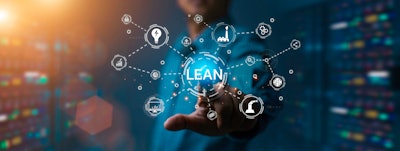
Employee engagement rates across the U.S. are dipping, due to a number of factors. A Gallup report measuring employee engagement disclosed that in 2022, an overall 32% of full- and part-time employees considered themselves engaged, while some 18% were actively disengaged. This level of active disengagement increased by two percentage points from 2021 and four points from 2020.This is the lowest ratio of engaged to actively disengaged employees in the U.S. since 2013, almost a decade earlier the report states.
The Gallup report listed some of the engagement elements that have been impacted the most. Among those elements listed were “opportunities to learn and grow” and “opportunities to do what employees do best.”
By implementing lean management principles, you can provide increased employee engagement – and so much more.
In its simplest form, lean is about engaging problem solvers in an organization. Lean helps teams look for, and implement, continuous improvements that are in the best interests of the company. Lean practices can result in significant benefits for your company that can include improved morale, workplace fulfilment and deeper sense of responsibility. Executives realize this, so much so that 69.7% of manufacturers use some form of lean practices in their facilities, according to data published with Reliable Planet.
Lean management is a long-term operational discipline that systematically engages associates to find workplace improvements. These improvements over time lead to increased efficiency and quality. The procedures and techniques used within a lean management initiative allow leaders to optimize production lines, improve inventory movement, monitor key performance indicators and make continuous progress to ensure the best possible results for their customer experience.
Lean helps to combat the increasing trend of disengaged employees by challenging them to help improve the organization and its operations. Lean helps teach employees to identify inefficiencies and then implement changes to improve processes and workflow throughout the supply chain. The implementation of lean management fosters a more collaborative culture – one that further empowers people to participate in continuous improvement.
How Lean Management Drives Employee Engagement and Continuous Improvement
1. The lean process boosts overall engagement. By involving supply chain employees and operators in the decisions and processes that directly affect their work productivity and efficiency, your team members will develop a feeling of ownership. Lean management teaches team members how to identify areas of improvement, therefore allowing them to leverage their expertise in the tasks they perform daily to optimize processes. Through continuous improvement and submitting Kaizens, employee morale can be improved through workplace collaboration, recognition of creative solutions, and providing a path to delivering outstanding work.
2. Lean generates operational improvement through collaboration. Lean management focuses on a number of core values throughout an operation. First, the practice of “Go and see.” This is the Toyota principle (Genchi Genbutsu) of going to and directly observing a location. Second, there is challenge. Lean looks to identify weakness in the systems operating within your business. This gives practitioners target areas to seek to make improvements. Third is kaizen, which refers to making small, consistent improvements to the system. Using kaizen as a tool provides everyone within your organization, regardless of title or responsibility, an avenue to submit ideas for improvement. Here again, the kaizen process boosts employee engagement and the feeling of ownership in making an impact in their daily work. Lean management encourages teams to practice respect – with much importance placed on the recognition of those doing the work being the experts. Last but certainly not least, lean management helps to instill a culture of continuous improvement through a deep sense of teamwork, showing support for individuals and their value-added work.
3. It helps to eliminate waste in time and materials. By teaching supply chain employees – team members of any level and tenure – how to identify time/material wastes in their processes, you can come up with solutions to help address those challenges. Leveraging data also helps. Combining lean management practices with telematics solutions can provide a wealth of real-time data and the capability to track key performance indicators. A number of benefits can be obtained by pinpointing inefficiencies. Identifying the inefficiencies can help us reduce waste, improve environmental sustainability and strengthen cost containment efforts.
4. The process utilizes visualization, organization and standardization. You can achieve higher operational efficiency and productivity by helping to eliminate or reduce non-value-added steps. Through standardization, for example, facilities can better help support improvements. You can establish specific targets for improvement once a standard is identified. Standards, performance, and targets for improvements are visualized so the team can see and work together effectively.
5. Lean management identifies optimization opportunities. Optimization is key to meeting today’s demands. Lean management looks to maximize use of limited resources by finding areas of opportunity to create flow of product, increase workforce productivity and leverage data for suitable tasks. By exemplifying teamwork, we find opportunities for improvement that lead to cost savings.
6. It encourages the practice of Plan, Do, Check, Adjust (PDCA). By making systematic changes that move the needle, rather than implementing arbitrary changes, you can gather data and facts to drive these improvements. PDCA spurs the organization to not blindly forge ahead – but instead to check and understand the effect of that change on both people and process to ensure effectiveness.
Today’s world is supersonic fast. Our factories, warehouses and distribution centers churn on, trying to keep pace. Much credit goes to our hard-working and dedicated supply chain employees. Now that you have an idea of how the practice of lean management can make a positive impact for your team and business objectives, what steps will you take to boost engagement and continuous improvement at your facility?