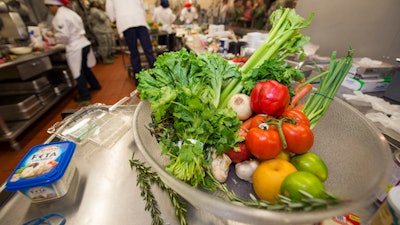
It was clear from the start that 2022 wouldn’t be business as usual for the foodservice industry. As new variants of the Coronavirus disease (COVID-19) emerge, supply chain leaders are also dealing with overwhelmed ports, labor shortages and other disruptions. But, these aren’t today’s only pressing supply chain challenges.
Food availability, safety and consistent quality are always a given. The next wave of change will be driven by impending regulatory requirements for traceability, along with growing consumer demand for transparency around responsible sourcing, sustainability and reduced food waste. Other factors, such as increased globalization and complexity of products are also making an impact. All of these challenges necessitate foodservice brands invest in technology-driven supply chain quality management, monitoring and compliance programs to implement requirements around finished product standards, ingredient sourcing, inventory management and supplier management.
Furthermore, the foodservice ecosystem must continue to increase its investment in preventative controls, facility audits, on-site inspections, product testing and product evaluations—all of which can further reduce instances of contaminated food products from entering supply chains to begin with. This will be imperative as the FDA ramps up its ability to identify defective products and trace pathogens to their sources in the supply chain within hours vs. weeks or months like in the past.
The brands that will survive and thrive during these changing times will be those that are well-positioned to address the following forces this year and beyond.
- FSMA Rule 204 and the new era of traceability. The proposed rule 204 of the FDA’s Food Safety Modernization Act (FSMA), which will be voted as a finalized rule in the United States in 2022, impacts the whole supply chain—from farms to facilities to retail food establishments, including both foreign and domestic entities. It requires organizations involved in manufacturing, processing, packing or holding foods on the Food Traceability List to maintain specific records regarding their traceability operations and the foods and ingredients they handle. The purpose is to help FDA investigators understand the entity’s traceability procedures and records when reviewing them during a foodborne illness outbreak or a routine inspection.
This level of record keeping will ultimately be empowered by item-level traceability, which will impact supply chains and retailers from end-to-end in foodservice and other industries. As part of its drive to spur innovation in this area, the FDA held a competition in 2021 and ultimately selected 12 worldwide winners in its New Era of Smarter Food Safety Low- or No-Cost Tech-enabled Traceability Challenge. One of the winners was Mojix, who partnered CMX. Mojix is working to advance traceability through the use of innovative technology and processes. As an outcome, Mojix launched what is said to be the first open data access, item-level food traceability platform, with CMX being the first solution provider to integrate with the new platform.
Item-level traceability data, combined with solutions such as CMX’s Enterprise Quality Management Software (EQMS) platform, CMX1, equip foodservice brands to manage supply chain partner records and relationships to products, formulations, ingredients, ingredient sourcing, packaging and labeling. They can also monitor the flow and inventory of inbound and outbound products within an organization’s supply chain and retail locations.
Furthermore, the CMX1 platform provides automation to manage product quality incidents, withdrawals and recalls when issues arise and when pinpoint accuracy and speed are essential. Item-level traceability data enables risk management and recall teams to quickly and accurately identify the quantity and physical location of impacted products or ingredients. It will also lead to less food waste because any storage or retail location without ties to the problematic ingredient’s supply chain journey can be taken off the product recall or removal list.
- Environmental, social and governance (ESG) and corporate social responsibility (CSR) as drivers for transparency. According to a recent research report by Deloitte, “to continue to thrive, companies need to build their resilience and enhance their license to operate through greater commitment to sustainable value creation that embraces the wider demands of people and the planet. The companies that hold themselves accountable to their stakeholders by increasing transparency will be more viable—and valuable—in the long term.”
In the near future, ESG and CSR will drive a new way of doing business. To demonstrate what compliance might look like in the consumer arena, expect a QR code on every piece of packaging. Buyers will be able to take out their phone in a grocery store and scan that code to see precisely where that product and all the ingredients it contains came from and all the places it’s been along its journey. The barcode could also include evidence that the product was tested and the supplier was audited and that it was kept at the recommended temperature the entire time it was in storage and transport. Recall information should also be available and perhaps even the manufacturer’s food waste policies and sustainability practices.
All of this will come about as consumers require more transparency in what they feed their families and more insight into who they do business with. Preference will be given to those foodservice entities that meet their personal requirements around these emerging concerns.
The consumer sector won’t be the only area of impact. Commercial lending, financial ratings, credit ratings and more may all be tied more closely to ESG/CSR ratings in the future as increasing regulation and the focus on clean food, responsible sourcing, food waste and other related concerns rise in importance across the business landscape. In fact, in California and Vermont, momentum is already evident in legislation that requires grocery stores to give community food banks excess food that would otherwise be thrown away. Also, by 2024, restaurants, hotels, schools and other businesses in California will, by law, no longer be able to send excess foods to landfills. They’ll be required to donate it to food programs for people in need.
As both consumer sentiment and government regulations around these initiatives increase, compliance auditing and record-keeping capabilities will be critical to foodservice businesses and their suppliers. To be managed at scale, these capabilities must be driven by digital, data and automation, using tools such as CMX’s ActivityStudio® for in-person and remote auditing and inspections for suppliers.
Moving toward a safer, more sustainable future
Although digital transformation has taken root in the foodservice industry, the reality is that many brands are woefully behind in their investment in technology. As we’ve learned during the pandemic, dealing with massive business change today requires agility. Digital tools and platforms, like CMX1, enable agility through real-time insights and timely, proactive decision making to fuel these quality management essentials:
● Know your suppliers and maintain accurate and up-to-date records and documentation about them.
● Monitor supplier compliance and performance.
● Know your products, formulations, ingredients, packaging and labeling and know their sources.
● Monitor the ongoing quality, safety and consistency of the products you source, sell and serve.
● Identify and resolve non-conformances and ensure that corrective and preventative actions (CAPA) are being implemented.
● Automate and resolve quality incidents, withdrawals and recalls.
As the next wave of change hits, a quality management program will need a robust digital foundation to move your business forward. Proven digital tools will be required to effectively execute crisis management for incidents and recalls, maintain regulatory compliance with FDA rules and government regulations for traceability and support the transparency consumers demand with the rise of ESG and CSR.
*This is paid contributed content.