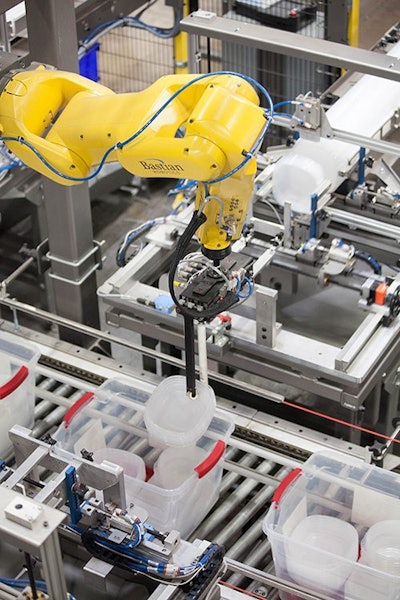
A growing number of distribution facilities are faced with the challenge of scaling up the efficiency of their end-of-line, storage, picking and fulfillment operations. The changing and increasingly complex dynamics of the distribution industry – such as expanding SKU counts, retail store just-in-time ordering, and fluctuations in throughput volumes due to seasonal influences and the popularity of e-commerce items – necessitate the need for more efficient, flexible and scalable requirements in distribution.
The continuous increase in the cost of land, construction, labor and facilities has put a heightened demand on more efficient automation and space utilization within these operations. Until recently, these warehouses were forced to invest in expensive, somewhat permanent, complex systems for what they could only project they might need well into the future.
Logistics executives’ concept of what an ideal distribution operation should look like, how it should function and what material handling systems should be in place is influenced by their distribution experience, the insight that they have gained from material handling equipment suppliers and by visiting the sites of other distribution facilities of similar application.
They are confronted with hundreds of decision points to be worked out when upgrading their current distribution operations. Yet many logistics executives do not have the extensive knowledge of systems available or maintain the analytical resources in-house to successfully upgrade their distribution centers. Evaluating the tremendous volumes of information required from many dozens of automation options for each application and making the correct decisions throughout every step of the process, can be a risky and daunting task for any logistics team, no matter how talented they may be.
Evaluating Process Solutions
Regardless of the distribution application, the automated solution must meet requirements for the desired volume throughput, cost efficiency, ROI and quality standards. Increases in production volume requirements and higher yields are often the key drivers that necessitate the move to a more efficient distribution system.
Process improvement, however, should be the central aspect of any solution, rather than focusing on the type of automation or a specific brand of automation. Approaching system design from a process perspective does not necessitate the implementation of any specific automated technology but leaves the door open to any options to achieve the objectives of the distribution facility’s supply chain executives.
The following questions should be asked when considering distribution process improvements:
- Will this approach deliver the best solution to the logistics challenges being faced?
- Will it actually provide an optimized design over the system(s) being used?
- Will it increase throughput and/or capacity in the upgraded distribution facility?
- Will it leverage capital investment, minimize operating costs, and provide a total lower cost solution?
- Will it provide design flexibility to easily expand as distribution needs require?
To properly evaluate a process solution, the distribution facility’s SKU and order activity should be monitored and analyzed to determine how that activity varies over time for the process being considered. Even down to the level of variations on a wave-by-wave basis, if necessary. Factors evaluated may include daily unit volumes, units per order, lines per order, packing sequence, unit cube and cube movement, cartons per order, total SKUs and percent of SKUs in daily demand.
An operational assessment for the process might include spikes in throughput, order cut-off times, number of fulfillment shifts, growth projections, initial capital investment, manageability, total labor, accuracy, product security, space and speed of processing required.
Not all of these factors would need to be assessed, but these are key factors that could be approached when evaluating any process solution relating to receiving, put-away, storage, picking, transport through the DC, sortation, value-added services, packing and shipping. Process evaluation ensures that the right amount of technology will be implemented for current and future growth needs. Too much capability is capital absorbing. Too little capability will necessitate higher operating costs by increasing labor. Only after adequate process evaluation should specific technology solutions then be considered.
Accessible Automation Point Solutions
Technology advances in automated distribution have enabled a more integrated approach for the operation of material handling systems, which, in turn, have provided significant advantages for increased throughput, system uptime and better ROI. Along with this technological evolution, an accelerated capability for streamlined energy management, energy efficiency and sustainability have also become possible, allowing ambient-temperature, deep-freeze and chilled distribution facilities to better manage their power draw, energy utilization, systems integration and overall operational costs.
Centerstage in this technology evolution are automated point solutions – discrete material handling systems which can be positioned within existing distribution processes to deliver a heightened level of automation. Point solutions provide a simpler alternative to bigger, more complex and permanent material handling systems, at much lower capitalization they enable a more accessible automation solution.
Automated point solutions are fully capable of interconnecting with existing manual and automated distribution processes. Integrating with the latest controls-based solutions and standard API-based software solutions, they enable a more seamless production flow to be engineered and implemented, attaining the highest levels of operational predictability and production efficiency.
On a more holistic scale, point systems can integrate the exchange of data between distribution processes facilitated by the Ethernet and cloud-based Industrial Internet of Things (IIoT) to support Industry 4.0 operation. Automated point solutions are designed to communicate and cooperate in synchrony with humans. This cyber-machine/human integration enables a much more efficient connection of processes and better organization within the production environment.
Essentially, accessible point solutions embody specific automation which: a) can be easily put into a distribution operation quickly to replace manual functions; b) permits scalability to accommodate future growth; c) can be smoothly integrated with existing manual and automated systems; and d) provides easier access to capitalization.
Examples of Accessible Automated Point Solutions for Distribution
Accessible automated point solutions can encompass a wide spectrum of technologies applicable to every distribution process from receiving through shipping. Following are some of the key technologies which are particularly suitable for accessible automation point solutions.
Autonomous Vehicles
Autonomous vehicles (AVs), like automated-guided vehicles (AGVs) and automated mobile robots (AMRs), are ideal accessible point solutions for transporting materials and finished goods between receiving, end-of-line, storage, picking and shipping operations.
Utilizing a combination of logic software and wireless navigation, AVs can perform tasks that are not possible with other transport systems – such as the uniform movement and positioning of loads to within a fraction of an inch of their designated targets, with minimal noise, and with a high degree of safety for workers and their operational environment. Interfacing with multiple systems, AGVs provide reliable unit-load movement, with near zero potential for product damage. AMRs support goods-to-person picking, transporting common load carriers like tables, carts, racks and shelves to specified locations throughout distribution facilities.
AVs permit a distribution facility to start out with a small point-solution system to fit discrete requirements, then add to the network with additional vehicles as needs grow. They finance only what is needed for the first installation, then refinance for subsequent expansions. This enables a relatively quick conversion from manual to automated processes and permits a fast ROI.
Robotics
Robotics are a key operation of distribution automation, delivering flexibility, speed and accuracy, making them ideal for point-solution productivity enhancements in a wide range of distribution functions. From a safety perspective, robotics minimize the risk of fatigue and injury that human labor is subjected to in repetitive and hazardous applications.
Utilizing articulating-arm robots and delta-style high-speed robots, a wide range of applications are possible for pick-and-place, sorting and end-of-line material handling. Accessible point solution applications include robotic pick-n-place for tray packing and e-commerce fulfillment. These systems are low maintenance, flexible and reconfigurable, and especially beneficial in applications dealing with sterile, hazardous and potentially injury-causing materials.
Robotic palletizing applications are excellent options for accessible point solutions, such as inbound and outbound palletizing and inbound mixed-case depalletizing. Robotic sortation is another accessible point solution consisting of independent-moving robots that transport products across a raised platform from an induction station to a designated divert. A good alternative to traditional sorters with fast implementation, the flexibility to add robots and induction stations as needed, with a lower capital cost compared to conventional sortation systems.
Maximizing the capabilities of a robotic point solution depends upon: a) programming the robot to perform the specific functions needed; and b) how smoothly the robot is integrated into a singular, optimized process line.
End-of-Line Automation
An increasingly frequent request from end-of-line packagers, particularly of e-commerce products, is their need to reduce operator interaction. The more complex the interaction for the operator, the higher the chance of human error in the process.
Automation that allows operators to start and run a case forming, packing and sealing process, for example, with minimal or no need to make manual adjustments, will increase order fulfillment accuracy, uptime and throughput. End-of-line vertical shrink-wrapping technology can greatly reduce the need for manual manipulation of vertically oriented products, like bottles, when providing secondary wrapping in multi-packs. Specialized conveyors designed to singulate and accumulate and provide precise positioning of products into and out of end-of-line machinery using laser vision systems, virtually eliminates product jam-ups, keeping throughput high.
End-of-line automated point solutions, such as these, are flexible, scalable and provide sustained high throughput, while reducing freight costs and minimizing the use of packaging materials. These solutions are highly discrete systems which can be easily integrated into any end-of-line process.
Goods-to-Person Systems
Goods-to-person automation can deliver a tremendous capability as a point solution. These systems have so many benefits when upgrading from a manual picking operation. Not surprisingly, many distribution executives have embraced a goods-to-person fulfillment approach as a solution to achieve more efficiency in their picking processes.
Low-barrier entry goods-to-person systems, such as AMR-based solutions, can be positioned as point solutions connecting more traditional, high-capital fixed automation.
The goods-to-person concept is simple: Incoming goods are removed from pallets, either manually or automatically. The cartons and/or pieces are then placed into totes for smaller goods or into trays for larger goods, and stored in high-density automated storage and retrieval systems, carousels or robotic systems. As orders are required to be fulfilled SKUs are automatically retrieved from storage and brought to the picker, either at a pick station where the operator picks into an order container or to an ergonomic palletizing station where items are packed onto a pallet. Since the picker does not have to walk, the focus at the pick stations and pack stations is on ergonomics and high productivity.
Medium and slow SKU movers are often the best candidates for goods-to-person automated systems. Because these are the SKUs that the picker, in a traditional person-to-goods picking environment, will have to walk multiple aisles between picks. Eliminating this significant walk element with a goods-to-person solution is where the automated systems deliver their greatest pick and cost efficiencies.
A key point is the design flexibility to easily expand as volumes increase – particularly with the capability to independently scale throughput and inventory, both at the time of the initial investment and over the life of the system. A further key point is that orders can be stored and retrieved simultaneously, as opposed to sequentially. This capability can make a significant difference in the speed and efficiency for optimum handling of orders on a high-throughput basis.
More Accessible Finance Options
By their very nature, point solutions do not demand the large amounts of capital required upfront as is for bigger, more permanent distribution systems. These discrete systems also permit capital expenditures to be aligned with company growth. Only finance what is needed for the current and/or short-term expected level of production. Growth beyond this point can then be financed as needed.
From a financing standpoint, there are more options available today for capitalizing automated point solutions than available before. Some material handling companies even help arrange financing for the systems they are providing. This contributes to making automated point solutions a more accessible option.
Technical Support
As brick-and-mortar retailers integrate e-commerce and transform into omni-channel fulfillment organizations, they increasingly seek to leverage the material handling systems in their supply chains. Retail store orders may involve shipping full, or mixed pallets of product to arrive within a one-week to two-week delivery window, while an e-commerce order might consist of several, different-category single items wrapped in a custom package delivered within one to two days.
Inevitably, this will include the addition of automated point solutions to facilitate their operations.
Evaluating what technologies should be considered that best fit the process needs, and integrating the point solution to the existing operation, these are the key points to be considered when implementing a successful point solution.
Distribution facilities, however, may not possess the skilled personnel and in-depth experience needed to evaluate and specify the technology, and integrate a successful point solution. Therefore, it is best to designate a single point of responsibility to evaluate process needs, specify equipment, and integrate the point solution. Ideally, one that is also fully equipped to provide technical support on-site, 24/7/365.
For distribution executives, using an independent distribution integrator, versus a system manufacturer or supply chain consultant, is a better solution to ensure the set-up and running of the point solution is managed in the most efficient and cost-effective way possible. Five critical consulting strategies differentiate the methodologies of independent distribution integrators from systems manufacturers and supply chain consultants: 1) single-point responsibility for all aspects of managing selection and integration of the point solution; 2) in-depth analytics and conceptual design; 3) assessing process needs before automation selection; 4) objectivity in automation selection to assess all options; and 5) comprehensive change management to ensure complete integration and operation. This gives the best guarantee that the point solution will operate as designed and meet the throughput levels and expected system efficiencies when the system goes live.