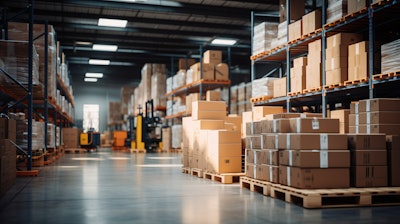
For a variety of reasons, Interest in warehouse robotics remains high. Chief among those factors are continued labor shortages, but cycle time pressure and general interest in adding more automation in the warehouses also are playing a part. With that interest has come an explosion in the number of warehouse robot makers. We count more than 50 operating in the U.S. You have lots of choices, and for many this will mean robots from different vendors operating in a single facility,
In warehousing, interest is especially high in what are termed Autonomous Mobile Robots (AMRs) for a new type of collaborative order picking. In this process, with some variations, the AMR moves itself to where order pickers are waiting or arriving in terms the right inventory location for a pick. There, with an AMR now there, an associate puts the selected item(s) into totes on the robot.
When done with any more picks in this area, the AMR next travels to another location/picker or off to packing area. This significantly reduces the travel time of associates, letting the AMRs to take on much of that costly burden. The warehouse robotics sector is still immature. But as noted above even at this early stage it seems clear that for many firms, the future will involve deployment of heterogeneous robots – meaning different types of robots sourced from different vendors or OEMs operating together in a distribution center.
What is the impact of this likely scenario? These different robots will frequently need to communicate with each other, either directly or indirectly through use of an integration platform, to automate the flow of information and tasks.
This is in general what in the robotics industry called “interoperability,” and is a key concept for companies planning warehouse robotics initiatives. The ultimate goal of interoperability is to build ‘’plug and play” systems in which new robots can much more easily be added to the warehouse floor. Interoperability will also enable much greater flexibility to change distribution processes over time.
Interoperability at Work
We stated above that interoperability is an important concept for companies considering warehouse robotics.
So, let’s look at what should be a common operational scenario going forward. Suppose a given company buys 25 AMRs to support collaborative picking as described above. But a couple of years later, the company has a need for additional AMS due to growth in order volumes as a result of an acquisition.
However, now there is another AMR from a different OEM that the company prefers for cost, design or other reasons. With interoperability, the company would be able keep AMRs it has and seamlessly add the new AMRs to existing fleet.
But here interoperability means even more. In addition to basic integration, a company will want to manage the robots from both manufacturers together in terms visibility, task assignment, performance measurement and more, operating both of them as if it is a single fleet. That’s a good illustration of what robotic interoperability can deliver.
Can Interoperability Standards Help?
There are a few initiatives in the robotics sector to develop cross-vendor integration protocols that will make interoperability much easier. Interestingly, if successful such standards should accelerate the trend of separating the hardware and software decisions.
Those developing standards such as VDA5050 and Mass Robotics 2.0 to date are either not widely used or are still under development. Many vendors have also started offering support for what is called a Robot Operating System (ROS). However, this is a loose open-source framework (not a complete standard) that doesn’t fully address all the challenges of interoperability.
The Robotics Platform Alternative
Given the lack of useful standards, companies will face choices for achieving robotic interoperability.
That includes the traditional method of manually programming interfaces between different robots and robots to software systems such as Warehouse Management, Warehouse Execution and ERP systems. The limits of this approach are clear. That includes elongated development times, high costs and a lack of flexibility over time.
A better choice it to adopt a platform strategy. Which begs the question: what is a robotics platform?
A robotics software platform is generally a Cloud-based ecosystem that provides a broad set of capabilities and services, from integration to fulfillment planning and execution. The platform might be thought of as sitting on top of automation/robotics systems and different types of enterprise software.
The foundation for any robotic platform success is integration. That includes use advanced tools that enable flexible “no code/low code” approaches to connecting robot fleets. An advanced platform can also more quickly integrate with WMS or other software applications through use of AI to greatly accelerate the difficult data mapping process.
The good news: Once the WMS is connected to the platform, then robots also connected to the platform now have real-time access to the WMS data.
A platform also delivers interoperability across robot types and connects different automated processes. A likely example would be communication from the platform to a robot that it needs move inventory from receiving to reserve storage, where another robot is made aware via the platform that there is a new put away task ready for completion, and it moves to begin and end its work.
Additional Interoperability Considerations
To maximize interoperability opportunities, companies should consider the following interoperability-related capabilities that may be available from a given robotics platform:
Flexibility in integration based on robot maturity: Different robot vendors come with software at different levels of maturity. An interoperability platform should be able to work with robotic vendors at any level of software development, ensuring flexibility in robot selection.
Flexible communication protocols: A platform should provide support for different protocols – APIs, socket communication, web services, ROS, VDA5050 etc.)
User experience consistency: For interoperability to be functionally effective, the user interface across robotic-enabled processes should be consistent, so that users can easily switch which tasks they are working on.
Observability: AMRs especially will generate huge of amount of data on their movements and activities that can be used for analytics, with the opportunity to normalize data packets from different vendors to create a unified dashboard.
Safety and risk mitigation: To achieve safety across different types of robots requires understanding the safety protocols of different machines and coming up with a common set up rules in an extended fleet manager running in the platform that sits on top of the fleet managers of each individual AMR provider.
While some of these capabilities may not be relevant in a company’s early years in warehouse robotics, they could prove valuable down the road. Therefore, give them some consideration today.
Interoperability Use Cases
We’ve already covered a couple of common robotic interoperability use cases:
(1) Adding new robots of the same type but from a different vendor and having all operate together as a single fleet.
(2) Connecting different types of robots or automation to support multi-step process flows (e.g., receiving to putaway).
Here is another one to consider: We’ve spoken to a global consumer goods company that wants to heavily automate distribution processes but give individual regions or countries they operate in the flexibility to select the vendor for a specific type of robot (e.g., a layer picker) and be able to easily plug that specific equipment into the larger platform infrastructure. This enables a centralized automation strategy with local execution.
Robotics Interoperability Matters
For a significant and growing number of companies, the future on the warehouse floor will be robotics of multiple types and vendors. To maximize flow and productivity, these heterogeneous environments must adopt interoperability strategies, enabling systems of different types to operate as if a single fleet. While standards to help with all this are being developed, for now a robotics integration and execution software platform will provide an attractive alternative to traditional programming-heavy approaches.