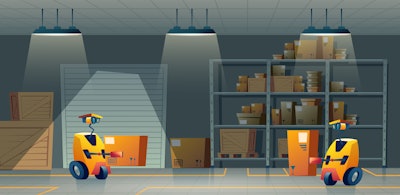
Take a step back in time to 2016. The iPhone 7 was brand new, Pokémon Go briefly took over city streets with folks hoping to “catch ‘em all,” Hamilton established itself as a phenomenon on and off Broadway, and Post Malone released his first studio album.
In Atlanta, MODEX took over the Georgia World Congress Center, and as it will again at this year’s show, automation played a central role. But the type of robotic technology, its adoption and state of maturity in 2024 is a testament to how much can change in a little less than a decade.
In the mid 2010s, the industry still had the omnipresent, formative forces of labor challenges and e-commerce growth, but the high level of investment, lack of flexibility associated with traditional ‘fixed’ automation and yet-to-be-proven condition of emerging robotic technology produced a much different robotics landscape. Operations evaluating robots wanted to see them working in the real world, not just trade show booths. Cost barriers made small and medium-sized projects difficult candidates to justify.
But today’s landscape is much different.
Here are four key developments that have shifted warehouse robotics from expensive, bleeding-edge endeavors to more accessible, proven options that can serve the needs of both small-to-medium size projects and the most well-resourced, complex logistics facilities.
1. Capability Proven in the Real World
Vision systems, gripping mechanisms and software have matured and established suppliers have emerged with solid track records for high performance and minimal downtime. Applications that may have been promising but unproven in the real-world, such as robotic each picking, now have a track record of successful implementations. But the value is not just the functional capability of dense automated storage systems and pick-and-place robots. Making various automation components work together as a cohesive system – not just individual islands of automation – comes from warehouse execution software and integration. This packaging of robotics technologies with software and other automation to address common warehouse workflows enables the top-line business results that deliver return on investment.
2. No Need to Start from Scratch
Designing and engineering highly complex solutions from scratch creates major barriers to entry for smaller and medium-size projects in terms of cost and speed to deploy. But as technology and software has matured, applications that were experimental in 2016 are not only proven as capable, but being refined and packaged as a standardized, modular solutions that can be configured according to the needs of the project.
One example of this warehouse-ready approach would be automated order fulfillment packages that combine advanced robotic picking, traditional conveyor and sortation and software to provide a cohesive, base solution that can be configured according to the needs of the project, whether e-commerce fulfillment, automotive distribution or another application. This approach enables lower upfront investment and faster deployment compared to approaching each project from scratch with a custom, one-off approach.
3. Flexibility and Limited Risk
Flexibility is more than taking the base robotic solution and adapting it for the needs of different industries. The ability to scale on an as-needed basis limits risk, giving businesses the ability to implement automation in a phased approach and at their own pace. To illustrate this value, contrast today’s robotics to an older automation paradigm. Consider the miles of conveyor and sorters installed in automated warehouses, together with traditional AS/RS technology like shuttle systems and cranes. This approach requires a lot of space, a lot of money and perhaps most importantly, commitment to a 10-year vision of capacity and workflow that is very difficult reconfigure even as operational realities change.
But what if operations could reconfigure systems with minimal cost and downtime, and boost capacity to match real changes in demand? Robotics allow decisionmakers to purchase what they need, with flexibility to add capacity later. For example, they can begin with 20 robots and the option to expand as demand requires – but if that demand never materializes, they do not have the burden of excess automation infrastructure. That reality takes significant pressure off decisionmakers and allows them to avoid the risk of mortgaging their future on a static system built on far-reaching projections.
4. A Broader, Labor-Based Business Case
Conversations to justify automation used to be dominated by direct labor savings, but other factors now play an important role. One example is managing the risks of an increasingly challenging labor market. Can you risk insufficient capacity to handle holiday demand by leaning on seasonal temp labor to scale up for peak season? Not only that, intense competition for the limited workforce that is available has warehouses using automation investment to help attract, retain and get the most out of labor.
Ergonomics and safety are key inputs that affect the business case, and implementing robotics can help reduce bending, twisting, lifting and other physical strains on employees. A simple but prominent example is walking – some facilities may be set up to have employees walk nearly 10 miles each shift and industry estimates commonly note pickers spending as much as 60-70% of their shift walking, rather than picking. But strategically using robotics in certain workflows can significantly reduce walk time, and investing in the work environment to help them work most efficiently can improve engagement. According to a GALLUP study, organizations with better employee engagement achieve higher performance, including substantially better retention, fewer accidents and increased productivity.
The Path Forward
Of course, the more things change, the more some things stay the same. While Pokémon Go possessed a distinct lack of staying power, Post Malone is still a prominent force in the music business, fresh off a performance of America the Beautiful at the Super Bowl. E-commerce growth and labor challenges have shown similar staying power, laying the foundation for an industry with a greater appetite for automation. But with more operations considering robotics for the first time, what should they know before taking the plunge?
Maintenance and support. Particularly for operations going from an entirely manual operation to robotics, they must plan for everything from basic building blocks like maintenance routine, training, monitoring and troubleshooting, to advanced industrial engineering capability. Another important element is operational discipline and work planning. Rather than simply throwing extra personnel at a pick module to push through the day’s work, bear in mind that robotics are designed for a specific throughput, and operations must balance work day-to-day for proper utilization.
Looking ahead, artificial intelligence (AI) has great potential to enhance the efficiency and capability of automation over the next 5-10 years. Just look at how machine learning algorithms have improved robotic pick-and-place solutions. Now, in addition to enabling task execution, imagine AI applied to plan work throughout the facility or predictive maintenance that can prevent a major downtime event by flagging a small, but important change. Just as the last decade saw truly transformative change in warehouse-ready robotics, continued advances dot the horizon.