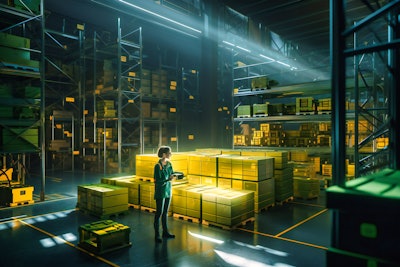
Effective warehouse management is critical for companies of all sizes. It enables fast and accurate order processing, efficient use of warehouse space, and reduced costs for storage and transportation. Warehouse management systems (WMS) and warehouse optimization are two important components of successful warehouse management.
Warehouse Management Systems (WMS)
WMS are software applications specifically designed to manage and control warehouse inventory in companies. Implementing a WMS can provide a variety of benefits, including better control over inventory levels, optimization of warehouse space and greater efficiency in picking and delivering goods.
One of the main functions of a WMS is to track and manage inventory levels. It captures all data associated with the storage and movement of goods, including item number, quantity, storage location and expiration date. This information can then be used to make decisions, such as reordering inventory or identifying items that are expired or damaged.
Another important aspect of a WMS is optimizing warehouse space. The system can automatically calculate the best storage location for each item to ensure that the available space is used optimally. In addition, the system can also optimize processes such as putaway, picking and delivery of goods to ensure they are done quickly and efficiently.
Another function of a WMS is to monitor and control deliveries and orders. The system can track order status and automatically send alerts when an order needs to be picked up, packed or shipped. It can also track the shipping process and automatically generate tracking numbers to keep track of deliveries.
Implementing a WMS can also reduce errors in picking and delivering goods. By using automated processes and reducing manual intervention, human error can be minimized. In addition, the system can also track inventory in real time to ensure that there is always enough merchandise on hand and that orders can be processed quickly and accurately.
Overall, then, implementing a WMS can help companies manage inventory more effectively, optimize warehouse space, and increase efficiency in picking and delivering goods. With a wide range of features and applications, a WMS can help automate warehouse processes, reduce errors and improve customer satisfaction.
Warehouse Optimization
Warehouse optimization is a process for improving warehouse efficiency and productivity. It involves optimizing processes, layout and storage to maximize the flow of goods in the warehouse and minimize bottlenecks. By optimizing warehouse processes, companies can improve accuracy and efficiency in the warehouse and reduce storage and transportation costs.
Steps to Warehouse Optimization:
Warehouse process analysis: A detailed analysis of warehouse processes is an important first step to optimization. This identifies bottlenecks and highlights opportunities for improvement.
Optimization of layout: The layout of the warehouse has a major impact on efficiency and productivity. By optimizing the layout, routes can be reduced and bottlenecks minimized.
Use of technology: the use of technology such as barcode scanners and automated storage systems can further increase efficiency in the warehouse.
Training employees: training employees can help increase efficiency and accuracy in the warehouse.
Risks in the warehouse optimization process:
Overtaxing employees: The optimization process can be overtaxing for warehouse employees. New processes and technologies may take time to adapt and may require training and education for employees. It is also important for supervisors to be understanding of their employees in this regard and to guide and support them through the process of transition.
Cost: Even though the warehouse optimization process is intended to result in cost optimization, it may initially involve high costs, especially if new technology or machinery is required. Companies need to ensure that the cost of optimization is commensurate with the expected benefits. In addition, tracking costs is an important tool to keep spending on schedule along the optimization process.
Disruption of processes: During the optimization process, processes in the warehouse can be interrupted, which can lead to delays and bottlenecks. Companies need to ensure they have a plan in place to minimize interruptions to minimize the impact on operations.
Loss of data: The optimization process often requires the use of software and technology. In this process, data can be lost or corrupted when it is restructured to another system, which can cause significant problems in the warehouse. Companies must therefore ensure that their data is kept secure and can be used until the new system can be put into operation.
Possible future developments in warehouse optimization:
Foreseeable future developments in this area are related to ongoing digitization, which is fundamentally changing the business world and is therefore here to stay.
AI-driven warehouse management: With the increasing prevalence of artificial intelligence (AI), companies will be able to use warehouse management systems based on AI algorithms in the future. These systems can use data from various sources, such as orders, inventory levels and weather forecasts, to improve warehouse efficiency.
Automated storage and robotics: automated storage systems and robotics may play a larger role in the warehouse in the future. Robots can be used to sort and manage inventory, minimizing human error.
Augmented Reality (AR): Augmented reality technology can be used in the future to optimize warehouse layout and help employees better navigate the warehouse. AR can also be used in training scenarios to teach employees new processes and procedures.
Warehouse management systems and warehouse optimization in context
Warehouse management systems and warehouse optimization go hand in hand to maximize warehouse efficiency and increase productivity. WMS systems provide a comprehensive solution for managing inventory, while warehouse optimization aims to improve warehouse operations. So only by integrating Warehouse Optimization and WMS can successful warehouse management be achieved.