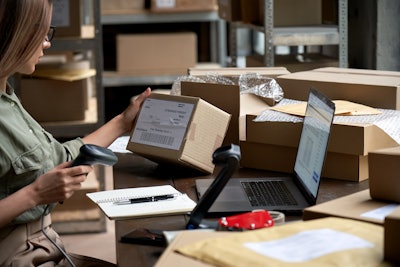
The global supply chain has never been easy to navigate. Unfortunately, the complexities continue to loom thanks to difficulties experienced around the world over the last 18 months. From a public global health emergency to war, the supply chain has shown that many supply chains are brittle — and have been overextended like a rubber band. However, the supply chain had many fractures before the onset of COVID-19 — it just happened to be a pandemic that brought it to its knees. Outdated methodologies like manual documentation have been problematic for decades.
Thanks to the explosion in e-commerce as a consequence of lockdowns and a major consumer buying behavior shift, Amazon surpassed FedEx in parcel volume shipping for the first time two years ago. Satisfying high consumer demand has been a struggle regardless of industry, and increased volume translates to decreased capacity and increased prices. From ocean freight to last mile parcel carriers, carrier capacity has struggled to keep up with the demanding market. Not only does the lack of carrier capacity negatively impact shipping businesses, it also has great potential to be problematic for end customers with organizations passing the higher costs of shipping onto the shopper themselves.
With hundreds of countries participating in global trade, from sourcing to delivery to end customers, it's nearly impossible to stay compliant and efficient without digitizing some processes like labeling and documentation. While labeling may seem like “no big deal”, getting it wrong is easy. Carriers are incredibly strict when it comes to correct labeling. They have to be in order to process shipments quickly and efficiently through their networks.
Carrier compliant labeling: a multi carrier strategy
The ability to rate shop different carriers is a true advantage compared to single carrier strategies. In fact, in today's gritty global market, a single carrier strategy is an explicit disadvantage. Unfortunately, a multi carrier strategy goes hand in hand with more potential for documentation and labeling mistakes without automating the processes. However, with the right transportation execution solution, organizations have the flexibility to choose from multiple carriers to compare rates, routes, and service levels within a single system.
There are tremendous risks associated with having incorrect labeling and documentation that can turn into hard consequences like expensive fines and even being blacklisted. For example, the United States is experiencing a baby formula shortage, but the American Food and Drug Administration (FDA) will not accept shipments from outside countries without compliance of strict regulation. This includes not only FDA standards, but also appropriate routing codes, customs documentation, and other bureaucratic hoops to jump through to streamline shipping processes. Without proper labeling, baby formula can sit in ports and spoil, never making proper entry into the country and into the hands of desperate customers.
Small bar codes, big information
Depending on shipping mode, whether it be air, maritime, or truck freight, proper labeling and documentation is essential for smooth and cost efficient shipping on the global stage. Automating the labeling and documentation process ensures that all commercial invoices are accurate and localized to specific destinations regardless of language barriers.
Even shipping under free trade agreements like the USMCA requires the management of appropriate documentation. For example, many carriers have moved to paperless invoicing for international shipments. These paperless documents also contain barcodes of embedded information relating to global trade, including origin for goods that qualify under a free trade agreement. Ensuring all this information is present and correct allows you to take advantage of paperless services to speed along the shipping process, as well as avoiding potential delays at ports and remaining compliant and efficient through customs.
Not only does smart, automated labeling eliminate data and communication silos surrounding the movement of products in the international market and ensure smooth movement through customs and ports, it also provides complete supply chain visibility to customers. Thanks to dynamics like the Amazon Effect, customer standards dictate a high level of visibility, and proper labeling is essential for a transparent, real-time analytics chain.
Cost control
Overall, total compliant labeling and documentation saves time, money, and logistical headaches like shipments idling in ports or warehouses. Even in a rapidly increasing digitized world, there are still only a handful of third-party logistics companies that provide an entire paperless process, including paperless invoicing. Having proper labels and documentation provided electronically proves to be cost effective through:
- Elimination of labeling at cross docks
- Significant savings on labor (by up to 50%)
- Strong supplier relationships
- Reduced spoilage on products with limited shelf life
- Avoidance of bullwhip effects and additional surcharges like demurrage and overage shortage and damage (OSD)
- Data integrity checks
Ultimately, streamlining labeling and documentation via automation with a strong software partner alleviates many global logistical pain points. Integration with customs agencies and appropriate classification avoids fines, penalties, and turns customers into advocates.