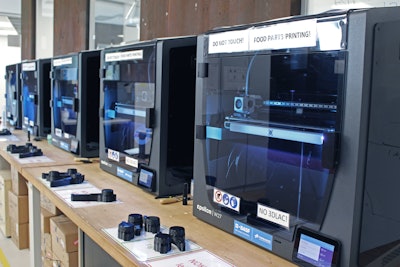
The fragility of the supply chain has been brought to light by recent disruptions exacerbated by the COVID-19 pandemic. Through the use of digitization and algorithms, the supply chain has been optimized with time. However, this has proven to be insufficient in recent years. Now apparent to all, including end customers, is the need to utilize alternative supply chain solutions. With OEMs competing on a global scale, ensuring prompt and budget delivery of goods is paramount. OEMs must look to reduce inventory costs while maintaining fast service for the end user in order to expand their profit margins.
Reducing supply chain risks
When a part is needed urgently, every hour can cost manufacturers hundreds and thousands of dollars with the cost of the spare part itself often negligible compared to the economic and reputational damage caused by its absence. Increasing the buffer in warehouses could minimize the risk of supply gaps, but counteracts previous efforts to reduce inventory and increases tied up capital, warehousing costs and obsolescence.
Another option is to source from several suppliers in multiple locations; should one supplier fail, others can cover the demand. However, interconnected global supply chains are often dependent upon a few suppliers of basic materials. Subsequently, for specific parts or components, all worldwide suppliers might be affected by the material shortage. A better solution is not only supplier diversification, but also in material alternatives.
A third way to improve the resilience of the supply chain is to return to localized manufacturing – as witnessed at the beginning of the COVID-19 pandemic. This saw many manufacturers 3D print critical parts needed to fight COVID-19 – such as face shields or valves for respiratory devices. This manufacturing philosophy, named bridge manufacturing, can be used as a blueprint to generally improve supply chain resilience.
Essentially, bridge manufacturing means having a technically viable alternative to bridge a gap. This gap can be economic if other technologies are too expensive, or an availability gap, if parts produced in another manufacturing technology are unavailable. Bridge manufacturing requires a manufacturing alternative for the part that allows on-demand, decentralized production. This ensures the part can easily be made available anywhere globally in the event of a sudden unexpected shortage. Consequently, should supply chains be disrupted, the OEM or supplier has alternative options, potentially saving money and reputation. As a concept, bridge manufacturing comprises three different types: provisional solution, equivalent manufacturing solution, and ramp-up/phase-out bridging.
Click here to hear more about emerging technology in supply chains:
Provisional solutions
Well known in dentistry, this is where a transitional prosthesis – using a different material and a different technology – is provided as a makeshift solution while the actual prosthesis is manufactured. Requirements for a makeshift solution are often lesser than for the original, making bridge manufacturing a second-best alternative from a technological standpoint.
Whether a part is used as a stop-gap until the ‘original’ spare part is delivered, or until it breaks down and is replaced by the ‘original’ spare part, bridge manufacturing of the part takes place in parallel to ordering a standard ‘original’ spare part. Like this, the machine downtime is reduced in the same way, saving the OEM money and reputation.
Equivalent Manufacturing
However, bridge manufacturing can meet all requirements and specifications of the ‘original’ part. In this case, bridge manufacturing might be more expensive in a regular supply chain situation, making it inappropriate for standard production, but it might have certain advantages when other constraints occur. For example, a polymer part could be manufactured at low cost per part in large quantities in a central location.
In the event of a global supply chain disruption and the part is needed overseas, this can be bridged by localized 3D printing close to where it’s needed in the required (probably low) quantity. If the manufacturing alternative was set up conforming to specifications, a part produced correspondingly might last as long as an ‘original’, eliminating the need to parallel order the ‘original’ spare part.
Ramp-up/phase-out bridging
Change in demand over a product’s lifecycle can vary drastically and upon launch, it’s hard to forecast future demand. It could boom or stay at moderate volume. For small and mid-volume series, additive manufacturing is an attractive option throughout the whole lifecycle.
If product demand rises quickly, manufacturing methods like injection molding are best from a price-per-part standpoint. Once manufacturing alternatives are in place, bridge manufacturing enables companies to switch as needed to optimize manufacturing costs.
3D printing is often favorable upon a product’s launch when only small quantities are needed, but when demand increases the OEM would benefit from another manufacturing method. Towards the end of the lifecycle, when demand decreases, the OEM can easily switch back to 3D printing.
With bridge manufacturing, it is important the technology does not need significant ramp-up time, is flexible insofar as quantities and is location-independent. Few manufacturing technologies meet these criteria; injection molding, requires high tooling investments and ramp-up-time before production can start. Milling can be very expensive and material-intense, and is limited regarding geometries and complex structures.
Adding value with additive manufacturing
The most viable option for bridging is additive manufacturing and in the last years 3D printing has become increasingly popular, especially for industrial applications.
Once a part is qualified and print parameters are set, it does not need any ramp up but can simply be sent securely to a 3D print service bureau for fast, cost-effective production. That’s to say, exactly where the part is needed, when it is needed and in the precise quantity needed – even a lot size of just one. It is these basic principles of 3D printing that continue to make it an agile and benefit-enhancing option for low-volume manufacturing requirements among OEMs large and small.