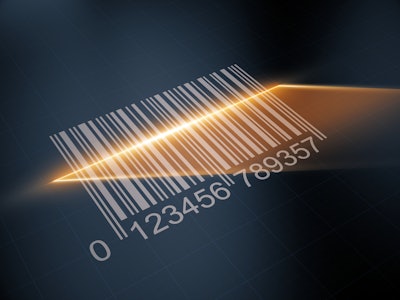
As shortages of different products continue to strain the supply chain and frustrate consumers, the need for hyper-accurate inventory visibility and predictive analytics grows. Demand strain across some manufacturing lines right now is a direct result of the Coronavirus disease (COVID-19) and its impact on consumer habits. The change in consumption patterns has stressed the supply chain on multiple levels.
The bullwhip effect that stems from modifications in consumer demand can leave manufacturers across industries with uncertainty and surprises.
Managing inventory throughout the supply chain with demand fluctuation and associated shortages brings challenges. Barcode technology is commonly leveraged for critical transactional and inventory management functions such as advanced shipping notice (ASN) creation, goods receipt, put-away and material localization.
Building supply chain resilience with advanced technology
Manufacturers have virtually no visibility into what is moving in and out of their facilities without labels. Labels identify what’s in packaging, the quantity of material, as well as the production stage (raw material, work in progress, finished good, etc.). The data acquired from these labels are critical to the production process.
Barcode labeling is precise, concentrated and detailed. However, the state of the world has forced us to ask this question -- is it enough? We’ve seen how quickly circumstances can change and how companies can be affected nearly overnight. In fact, one of the most broadly accepted conclusions about the COVID-19 pandemic is the way it revealed how broken the supply chain is.
Further digitalization of the supply chain with Internet of Things (IoT) sensor technology, like RFID, as a counterpart to barcodes can help prepare manufacturers for the remaining effects of the pandemic and any future circumstances.
The chaos and confusion that comes with irregular demand makes timing and seconds allocated to tasks even more important than usual. Barcodes, in most cases, require human interaction or process, both of which add time and introduce the opportunity for failure. RFID technology allows for the reallocation of employee time to value-add activities and infuses an unprecedented degree of accuracy.
Less hunting, more problem solving
Barcode labels are also leveraged for more than just inventory management. For example, these labels remain the sole identifier of key material and process details leveraged in reverse searches in locating assets or managing a recall. These use cases are further examples of enabling these labels with smart technology such as RFID to make the entire process more seamless. Advancements in technology bring localization of material through smart labels down to precise X, Y and Z coordinates.
Enhanced data brings enhanced possibilities. By infusing technology into the process, the investigation phase can be a thing of the past. Critical inventory data including real-time shipment notifications, precise material localization and in-transit information can lessen the impact of material shortages by allowing the supply chain to be proactive and not reactive.
Technology for more than just parts
The recent chip shortage that has made its way to various industries creates an unprepared manufacturing environment. As companies are forced to idle plants while they wait for chips, the demand building up in the background will eventually force manufactures to kick production into high gear. Necessary time and cost-saving technology will make the difference between plants that survive and those that do not.
It is at this challenging time where all manufacturers are looking to do more, sometimes with less. Technology can replace antiquated processes, streamline efficiencies, and drive unparalleled visibility. This can all happen with a very small change. Dramatic improvements in sensor-based technology such as RFID can flip the paradigm in terms of the art of what is possible with previously standard barcode labels.