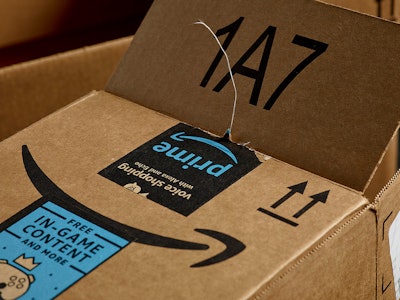
One of the year's biggest e-commerce days kicks off today. Amazon's annual Prime Day features deep discounts for Amazon Prime and members and will generate sales to rival those of the holiday season, even during of the year's lowest sales periods. In fact, sales have grown more than 60 percent year-over-year since 2016.
Retailers supplying the more than 560 million items available every day on Amazon in the United States are upping their game with the help of technology to meet expectations for quick deliveries and excellent service by optimizing their shipments and improving visibility.
Dan Clark, founder and president of Kuebix, the creator of a transportation management system (TMS) that delivers what it calls true freight intelligence, says “Amazon Prime Day is like Black Friday, only in July, and demonstrates how consumers’ adoption of e-commerce shopping is growing at a pace that far exceeds expectations.
"E-tailers shipping into Amazon fulfillment distribution centers (FDCs) are focusing on improving efficiencies within their supply chains and streamlining operations to keep pace with the increased volume. By leveraging the power of technology, retailers are lowering transportation costs, finding needed capacity and gaining visibility into operations to ensure customer service expectations are met,” Clark adds.
Prime Day comes at a time of year that has been traditionally slow for the supply chain industry. There aren’t any major holidays, and back-to-school hasn’t quite started. However, the popularity of the event, coupled with the capacity crisis and driver shortage, are causing roadblocks for some retailers who haven’t already optimized their supply chains. According to Clark, to keep up with the heightened order volume, retailers must streamline internal processes, ship products more efficiently and maintain a heightened level of visibility to order line items.
Clark notes that retailers are, in turn, turning to technology to improve their internal processes through order integration, rate-comparison and freight pay and audit features. Global logistics communities are uniting carriers and shippers to find optimal routes to share assets and fill empty miles. Powerful optimization tools are consolidating loads and planning the most efficient routes to cut down on transit time as well as costs. All these processes are being made possible by technology and are helping to combat the capacity crunch by making shipping more efficient and utilizing assets to their fullest.
“Amazon has set the bar high in terms of order visibility. Companies are now taking advantage of technology to gain visibility into their supply chains, resulting in superior customer service and more efficient operations. The adoption of technology like tracking devices, on-board computers, and cloud-based portals means that retailers can collaborate with carriers to improve performance,” continues Clark. “Carriers can provide an updated status of their delivery so that retailers know where goods are at all times and when to expect their arrival. If a delay is going to happen, the customer can be alerted, which improves satisfaction.”
The industry is braced for “Christmas in July” as the countdown to Prime Day draws to a close. The deep discounts on more than 1 million items, both Amazon-branded products as well as items from third-party sellers, are guaranteed to have a large impact on the supply chain this year. In order to keep up with increased order volume and inventory turns, shippers are turning to technology to improve their processes and speed up delivery.