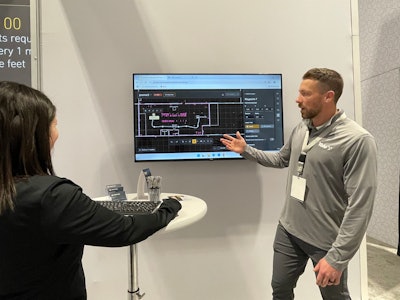
Yale Lift Truck Technologies announced Yale Relay, an intuitive drag-and-drop portal that replaces the complex software coding requirements typically associated with automation.
The new portal enables easy set up and on-the-fly changes without the need for custom programming, allowing warehouses to reduce their dependence on scarce warehouse labor without software engineering resources.
“This new solution represents a reboot of automated lift trucks, positioned to more efficiently meet demand for mobile automation by avoiding the labor and capital constraints of today’s market,” says Kyle Smart, sales manager, emerging technology, Yale Lift Truck Technologies. “Not only does Yale Relay address challenges sourcing lift truck operators and software programmers, it completely changes the financial commitment necessary for end users to deploy automation. Rather than a major capital expense, warehouses can simply pay by the month through a rental agreement and avoid the major upfront costs of purchasing equipment.”
Key takeaways:
- Yale Relay automated lift trucks are backed by training, parts and maintenance through a single, local source – the Yale dealer network.
- The drag-and-drop portal allows for significantly faster startup than traditional approaches, enabling implementation in as little as 1 day.
- Mapping the facility is as simple as manually operating the lift truck along the desired route, dropping waypoints in the portal, and making changes by selecting a waypoint and dragging it to a new location. The portal provides cloud-based access that enables easy, efficient management of automated lift trucks across multiple facilities, and reduces the need for on-site interventions with remote monitoring and update capabilities.
- It is designed with the ability to integrate with other common warehouse systems like facility fire alarms, interactive input boxes, programmable logic controllers, warehouse management systems and more.