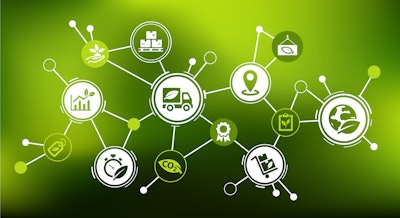
For those of us operating specialized warehouse and co-packing businesses, having a commitment to sustainability is a strategic choice that aligns with our leading customers’ priorities – and their customers’ increasing demands for environmentally sensitive business practices.
Sustainable warehouse initiatives fall into two broad categories:
- Focusing on your facilities and their carbon footprint.
- Reducing waste all throughout the supply chain.
At your facilities
On the physical plant side, the first question is where are you located? Warehouse sites that are in remotely populated rural areas or in big office park settings that require staff to drive long distances are less desirable from a sustainability standpoint. Strategic warehouse placement can:
- Shorten distance to customers getting their product to you.
- Reduce customers’ delivery distance to retail networks, which increases efficiency in transportation.
- Reduce non-highway miles and the related carbon footprint.
- Increase opportunities for freight backhauling, enabling both optimal freight carbon impact and associated freight pricing benefits.
- Cut the commute for your employees. How your team gets to and from work makes a big difference in both employee morale and your Scope 3 environmental footprint. (That’s why we place our facilities as close to worker homes as possible, near bus stops and at locations that can be reached by bicycle).
- Help meet the demands of CPGs that are onshoring, in an effort to limit global supply-chain hiccups and pivot when consumer trends shift.
The second facilities-focused question you should ask is whether there are upgrades you can consider to your physical plants that will boost efficiency and cut your carbon footprint in your day-to-day operations? Two big ones we are seeing are installing LED lighting and using electric forklifts to move product across the warehouse floors.
Trending Materials and Timely Choices
In addition to implementing smart choices about where we site our warehouses and how we invest in upgrades, we believe the greatest impact for sustainability can result from a laser focus on eliminating waste all through the supply chain, from the design of the packaging to the consumer purchase. Best practices include making sure products stay fresh, that boxes are no bigger than they need to be and that material that goes to the landfill is kept to a minimum. Here are some trends we see that support sustainability:
- Efficient Processing and Disposal: Efficiencies can be gained in the co-packing process by reusing master containers, ensuring that products are touched just once and that anything that’s scrapped is properly sorted, recycled and processed by recyclers and municipalities. For one customer in particular, we will soon be receiving WIP product in collapsible plastic totes that when empty will be returnable for washdown and re-use. Recycling is fantastic, but reduction/elimination and reuse are where the big gains are made.
- Expiration Dates: Planning, collaborating and using FEFO (first to expire/first out) or FIFO (first in first out) discipline/track-and-trace system helps ensure that products are not thrown out due to expiration issues that could have been avoided.
- Consumer-Friendly Graphics: Packaging in easy-to-read graphics helps the consumer identify what to recycle, allowing them to do their part when product reaches their hands.
- Consumer Recycling and Disposal: Knowing that over 80% of recyclable materials in product packaging are still placed in waste receptacles by consumers and never recycled, next-gen co-packers are working with their customers to use not only recyclable, but better yet, biodegradable materials.
- Compact Packaging: Designing packaging that fits the most product on each truck means sending fewer trucks on the road and cutting freight costs. Designing consumer packaging, master shipper and pallet patterns in tandem lets you optimize palletization and gain maximum cubing percentages. Given this mindset, we have learned that using a bulk storage philosophy works better than racking in the warehouse, as it allows for pallet sizes that often are not allowed in traditional racks.
- Easy Returns: If there is a need for the consumer to return the purchased item, it makes sense to make it easy for customers to return merchandise in its original packaging. This helps to keep the packaging out of the landfills, and it provides the best protection for the returned merchandise.
Sustainability is an ever-evolving effort for responsible businesses across industry sectors. For those of us on the warehouse and co-packing side, we understand that evaluating best practices and then investing in processes that cut our carbon footprint makes good sense for today and for the future.