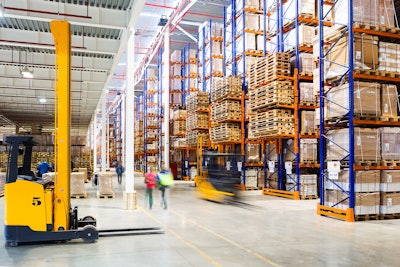
Industrial ventilation and air filtration are important considerations for warehouse design. Here are the terms you need to know—and how to improve the efficiency, effectiveness and sustainability of your ventilation solution.
1. Occupancy Rates and Activities
How many people will be occupying the space, and how much time will they spend there? Proper warehouse ventilation is important to ensure the health, comfort and safety of the human beings who will be working in the space. The higher the occupancy rate, the longer the time people spend in the area, and the more strenuous the work demands, the more critical ventilation will be.
2. Material Storage Requirements
What is being stored in the space? What are the temperature and humidity requirements for proper storage? Some materials—like dry goods, paper products or pharmaceuticals—may require temperatures and humidity levels to stay within a defined range. Other materials, such as construction materials, may be more forgiving. Warehouse ventilation is an important component of maintaining appropriate indoor temperatures and humidity levels.
3. Indoor Air Quality
Indoor air quality (IAQ) refers to the levels of airborne pollutants in the facility air. In a warehouse environment, the largest contributor to indoor pollution is usually exhaust from material handling equipment. Deadly carbon monoxide and dangerous respirable particulate can build up in inadequately ventilated warehouse environments. In some cases, indoor pollutants may be linked to the materials being stored, such as outgassing of volatile organic compounds (VOCs) from foams, paints and plastics, or dust from loose storage of bulk or powder materials.
4. Room Refresh Rates/CFM Requirements
The room refresh rate (or air change rate) refers to the rate at which fresh outdoor air is introduced to the space. It is usually expressed as the air changes per hour (ACH) in a room. Air change rates for warehouses are typically set between 6 – 30 changes per hour. ASHRAE sets minimum ventilation rates for commercial and institutional spaces (expressed in cubic feet per minute (CFM) of airflow per square foot of area) under the ANSI/ASHRAE Standard 62.1 guidelines, based on the space type, occupancy and room size. For warehouses, the ASHRAE minimum ventilation rate is 0.06 CFM per square foot. However, this is a minimum rate and must be adjusted based on occupancy rates, indoor air quality and other factors. For example, if there are excessive fumes from material handling equipment, room refresh rates will need to be higher to compensate. To calculate ACH from ventilation system CFM (or vice versa), use the following formula: ACH = 60Q/Vol. (Q= the CFM of your system and Vol is total air volume of the space in cubic feet.)
5. Layout and Airflow Patterns
Once you figure out your optimal air change rate and CFM for your space, you then need to consider how you want air to flow through the space. Warehouse ventilation generally involves some combination of rooftop or sidewall exhaust fans, rooftop or sidewall supply fans, rooftop gravity vents and wall louvers. These can be positioned to create different airflow patterns in the space. For example, exhaust fans can be placed along one sidewall and supply fans or louvers along the opposite wall to create a continuous crossflow pattern. Another option would be to put exhaust fans along the center roof line and supply fans on both sidewalls to bring cool air in from the sides and exhaust warm air from the ceiling. Airflow patterns should be designed to remove indoor air contaminants from the breathing zone and keep air circulating through all parts of the facility for better temperature and humidity control. In heated or air-conditioned warehouses with high ceilings, additional fans may be needed to combat air stratification, in which warm air rises to the ceiling and cooler air settles to the floor. These fans are located to promote air mixing within the room.
6. Exhaust/Makeup Air Balance
It is important to properly balance exhaust and makeup air rates for the warehouse. If you exhaust more air than you bring in, you will create a negative pressure condition in the warehouse (inside pressure is less than atmospheric pressure). Conversely, if you bring in more air than you exhaust, the warehouse will be under positive pressure (inside pressure is more than atmospheric pressure). If fresh air is coming in primarily through open doorways, windows, and louver systems, the pressure inside the building will balance naturally—the more air you exhaust, the more will be pulled in through these natural openings. If the warehouse is sealed more tightly (for example, to keep heated/cooled air in or keep outdoor pollutants out), you will need a mechanical makeup air system to bring in fresh air to compensate for the air being exhausted. Maintaining a slight positive pressure will reduce the flow of outdoor air into the building if a door or window is opened. In some cases, maintaining a slight negative pressure in some areas may be desirable—for example, to prevent airborne contaminants from migrating from “dirtier” to “cleaner” areas within the facility.
7. Filtration Needs
Does warehouse air need to be filtered? Most warehouses rely on basic industrial ventilation principles to bring fresh air in and exhaust stagnant air to the outside. However, it may be desirable to add filtration options to improve indoor air quality. Filtration can be used with supply fans to remove outdoor contaminants such as dust, pollen or air pollution from intake air. If the warehouse is heated or cooled, this will reduce the strain on HVAC system filters. Warehouses rarely produce enough emissions to require filtration on exhaust fans. However, if excessive fumes and particulate are building up in the breathing zone due to the use of material handling equipment, it may be desirable to use portable air purifiers in areas where humans are working.
8. Energy Consumption
A warehouse ventilation system should be designed with energy efficiency in mind. For example, high-volume, low-speed (HVLS) fans can be used to improve temperature control and reduce the reliance on the HVAC system. The layout and design of your warehouse ventilation system will have a big impact on the overall efficiency and energy consumption.
There is no one-size-fits-all answer for efficient warehouse ventilation system design; the right answer will depend on the facility size and layout, climate conditions, heating and cooling requirements and HVAC system design, indoor air quality and other factors. Ideally, design of the ventilation system will be part of the initial design and engineering process for a new facility; it is much more cost-effective to design the right system from the start than to try to correct or retrofit later. For best results, work with a ventilation and air filtration expert with training in ASHRAE standards and ACGIH guidelines for warehouse ventilation systems.