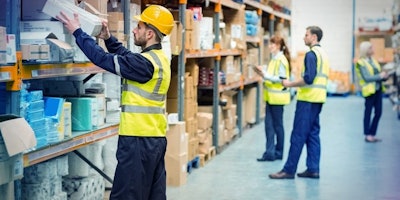
The average U.S. warehouse wastes 6.9 weeks a year on unnecessary motion—costing the industry $4.3 billion, or 265 million hours of labor annually, according to data from the U.S. Census Bureau.
Unnecessary motion is often difficult to comprehend and recognize. It’s ingrained in our habits, and many times it’s hard to understand how it indicates a larger problem on the floor. For example, walking to a fixed computer or printer is an activity warehouse staff have been doing for years. For many, it may not be viewed as waste of time, just simply a part of the job. It doesn’t happen all at once either. It’s 20 seconds here, or 10 seconds there. It may not seem like much, but even a few extra steps add up.
California’s largest supplier of fresh berries can offload 18 truckloads of produce a day in one single facility. By monitoring wasted motion, the supplier could then implement new practices, reducing processing time for each truck from 45 minutes to 30 minutes. That is a total of 4.5 hours per day – or 1,170 hours per year - translating into a savings of about $22,000 per year.
For example, Direct Relief receives thousands of donated pharmaceutical and medical supplies a day to their 24,000 square-foot warehouse. As a non-profit, they must work smart. Every dollar they save in distribution can be re-directed to those who most benefit from their work.
As a part of their continuous improvement plan, Direct Relief implemented a paperless system, reducing the amount of time spent walking to printers and scanners. They deployed mobile powered carts equipped with a laptop, monitor, scanner, printer, an electronic scale, supplies and a wastebasket. Both the carts and medicines are now wheeled to storage locations or forward picking bins for direct put-away.
In the first month, Direct Relief experienced a 40 percent increase in the number of batches received. They did it more accurately and in 20 percent less time. Direct Relief was also able to cut the time it takes to pack and ship by almost 70 percent.
Here’s a few ways you too can monitor wasted motion and learn how much it’s costing your warehouse:
· Fitness trackers and warehouse personnel trackers:
o Although the extensive data provided from these devices can prove to be very valuable, they do come at a cost—both literally and figuratively. They can be expensive to implement and can counteract the steps you have taken to build a strong rapport with your employees. Recently, Amazon patented a warehouse personnel tracker in the form of a wristband.
· Time-trial software:
o These software programs provide an in-depth look at each process but can be time consuming and expensive to implement. However, employees can find these systems to be less intrusive than other means of tracking.
· The MotionMeter App:
o Recently, Newcastle Systems released the MotionMeter app to assist warehouse managers in running easy, quick time studies. The app can be deployed in minutes and generates a comprehensive overview showing how much the wasted steps are costing you and how much can be saved annually if the wasted steps are eliminated. It can also be exported as a PDF and emailed directly to the app user or supervisors within the organization.
Regardless of the method, it’s important to continually study warehouse processes and work to find the most efficient way of completing necessary tasks. Small efficiencies can make or break a business as they add up to high costs and wasted time.