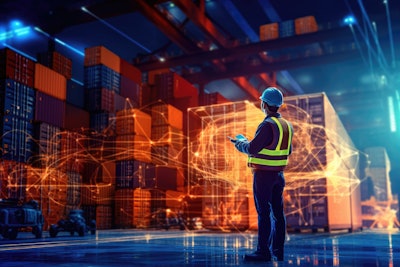
Rapidly evolving competitive landscape, labor shortage, financial constraints, increased e-commerce demand and market instability: the confluence of all these factors can make things feel more than a little uncomfortable for warehouse workers and executives.
In response to these challenges, the supply chain industry is looking for opportunities to better equip their teams with affordable and easily deployable technologies that help them optimize workflow.
Understaffed and Overwhelmed
Despite discussions of automation potentially mitigating labor shortages, the industry is not at a point of achieving universally dark warehouses. The value of skilled warehouse workers remains undeniable, however, providing them the resources to excel in their roles needs to be prioritized.
A recent survey of supply chain workers unveils a stark reality — labor shortages loom as the most pressing issue for respondents (57%), with an expectation of things getting worse rather than better. In other words, the outlook isn’t great.
In response to the shortage, warehouse executives are navigating uncharted territories as they explore avenues to enhance employee experience, eradicate inefficiencies and do more with less.
Better, Faster, Stronger: The Power of Business Process Automation (BPA)
In light of these challenges, Business Process Automation (BPA) is a transformative approach that can reshape the warehouse worker experience, revamp operational efficiencies and boost productivity — all without overburdening the existing workforce. The core principle of BPA lies in the automation of routine business tasks, liberating valuable worker time and elevating overall productivity. This solution is easy to configure and requires little training to get workers up to speed – providing an incredibly fast time to value.
Here’s a look at three ways BPA can support operational objectives while enhancing the warehouse worker experience.
1. Combat Dual Pressures
Do more with less — sound familiar? Warehouse workers are grappling with the dual pressure of increased workload (due to a seemingly interminable rise in e-commerce) yet reduced staff.
While important, filling out paperwork can take employees away from their workflow, add more work to their plate and slow down operations. By leveraging BPA, the various forms used every day can be electronically sent to the appropriate recipient immediately – helping to streamline operations. Additionally, given forms can be built into task workflows, they can be set to mandatory which ensures a safe working environment. For employees, this means less worry about ensuring paperwork is completed accurately and timely, along with less time spent walking the form to the manager’s office for processing.
Since BPA streamlines the form process, it can liberate an employee’s time and therefore, help ease their workload – even amid the staffing shortage.
2. Elevate Employee Experience & Optimize Workflow
Rarely do operations run smoothly in a warehouse – employees are constantly being pulled into numerous directions. When things inevitably go awry in the warehouse such as damaged goods and barcodes, employees (especially new ones) need to report the incident, redetermine the priority workflow and inquire with numerous colleagues for a solution. This can be a frustrating process since it tacks on time to report and resolve the issue – leading to extra hours of work and burnout.
With BPA, employees can fill out a form to report the scenario from their device(s) and easily determine the next steps. By doing this, they can stay focused on priority tasks and not waste time trying to troubleshoot a problem. Employees can go on with their day instead of filling out paper forms and aimlessly walking around looking for someone with the answer to their problem.
Imagine being able to streamline workflows, address bottlenecks quickly and enhance accuracy — without placing burdensome demands on your staff. That’s the power of BPA. And it makes for a significantly more robust, agile supply chain — plus happier workers.
3. Certainty, Consistency and Cost-Efficiency
Anyone pitching to an investor or sharing a report with the board wants to be able to highlight these three Cs: certainty, consistency and cost-efficiency. BPA facilitates all three.
Done right, BPA generates a wealth of data that can be harnessed for smart decision-making. From demand forecasting to inventory management, the availability of accurate, real-time data empowers executives to make the right choices. Digital forms via BPA make it easier to archive, sort and search among the countless files. By having an electronic database, you can ensure the required safety checks and inspections are completed routinely and save countless hours archiving forms.
A Glimpse into the Future
As the supply chain industry navigates the path ahead, savvy warehouse executives are investing in resources that will deliver major ROI and help them adapt to whatever comes next. While we can’t know exactly what’s coming down the road, we do know that surviving — and thriving — will hinge on innovation, efficient operations and cost-savings. And BPA delivers just that.
By embracing BPA, warehouses can usher in an era of automated routine tasks, amplified efficiency and a revolutionized worker experience. Instead of just wondering what lies ahead, forward-thinking leaders can build a competitive supply chain ecosystem and ensure that they’re leading from the front.