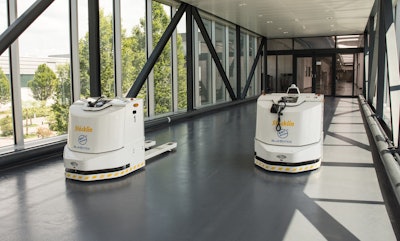
If considering investing in automated guided vehicles (AGVs), here’s how your company can ensure to get an optimum solution and quick return on investment for your application.
What navigation system do I need?
Once you have established what type of vehicle you need, be that a pallet jack, tugger, automated guided cart (AGC) or forklift, you need to make sure you choose an AGV with the appropriate navigation technology onboard. There is no single “right” solution here. How you use a vehicle will influence this technology selection, in terms of the accuracy, robustness and flexibility required for the application. Take magnetic tape navigation, for example. This is a form of physical “line following,” whereby the AGV follows tape laid down on the shopfloor. It is simple and precise, so if routes on-site never change and never will, it could be an excellent solution. A vehicle’s initial installation and any future modifications can, however, take time and therefore cost. Note that if multiple vehicles are required, fleet and traffic management when there are lines on the floor that cross each other can become difficult.
Another navigation option uses tags. Whether these are QR codes, RFID tags or magnetic points in the floor, the vehicle follows the route defined by the tags (similar in fact to following tape). Again, this navigation option – often used in e-commerce environments – is reliable and robust, but it can take time to install and is time-consuming to modify.
Laser triangulation navigation meanwhile uses a laser on top of the vehicle. This bounces laser beams off reflective targets that must be professionally around the site and routes are programmed using software (nothing is laid or installed in the floor). This option offers good accuracy and vehicle speed, and requires less maintenance than line or tag navigation. However, long design and installation times are common. As the vehicle’s laser needs to be positioned up high, this approach does not suit AGCs.
Vision guidance, where vehicles use cameras and a 3D map to calculate their position, are easy to install and maintain, and their routes can be readily modified. Changing light conditions, however, can affect system accuracy and thus reliability.
The other option for AGVs is so-called “natural navigation.” This can be based on “scan matching” or “feature matching” methodologies. Both typically use a vehicle’s onboard safety lasers to create a 2D site map and then position the vehicle with reference to this, but scan matching products often need an additional sensor on top to be precise and robust. With scan matching, each scan needs to be extremely accurate and any slight changes in the environment can create problems. Feature matching meanwhile uses permanent features on site - such as walls, columns or fixed machinery - as references to position a vehicle. Even if only a few references are visible to the scanners at one time, this is enough to ensure accurate vehicle positioning. Feature matched natural navigation requires minimal on-site installation (no infrastructure changes), is easy to maintain, reliable and is well suited to managing large fleets of AGVs.
Is path following or obstacle avoidance better?
Within the natural navigation approaches available today, the way in which routes are followed varies. Either virtual path following, where a vehicle stops in case of a blockage or obstacle avoidance, which sees a vehicle dynamically leave a blocked path to try and find a better route through the site. Which is the best approach? Again, it depends on the application!
Path following is typically (yet counter-intuitively) more efficient and therefore ideal for busy industrial installations. In automotive production environments, for example, space to move around objects may be limited, and there could be tens of AGVs operating in a larger fleet, so the time an AGV spends navigating around one and then possible more new obstacles and other vehicles can have a significantly detrimental impact on productivity. However, when adopting a virtual path following strategy, staff training is key, so that blocking obstacles, such as pallets, are removed quickly from an AGV’s path.
If, however, a vehicle is small and there are likely to be many people or moving obstacles, such as in the case of a cleaning robot working its way through an airport concourse or commercial center, path following might not be the best fit. It could mean the vehicle might never finish its route. In this case, obstacle avoidance, would almost certainly offer better efficiency.
Maximizing ROI
Ultimately, companies employ AGVs to reduce costs and increase efficiency. There are several points that should be considered to optimize return on your investment (ROI). Firstly, an effective and extensive simulation of your future AGV operation will enable you to identify the most efficient routes, test different vehicle actions (lifting forks, docking to recharge, changing direction etc.) and thus identify problems prior to installation. Fixing problems and oversights before a system is installed by its producer or a third-party integrator will save you both money and headaches down the line.
Next, be sure to consider what you might need in future. You may just be looking at starting with a single AGV to test your project, but if it has the effect you hope, how easily will you be able to add extra vehicles next month or next year? Does the AGV you are considering tie you to only purchasing more from the same manufacturer or is its autonomous navigation system, say “cross-platform,” giving you the flexibility to add different brand of AGV and control this fleet via the same management software? It is important to ensure the system you can adapt and grow with your needs.
Additional questions to ask include: Do you need your AGV to communicate with other on-site systems, such as a warehouse management system, mechanical, electrical and plumbing, enterprise resource planning and more? If so, how will it be integrated? Have you ensured the vehicle fits with your site layout, including the width of its aisles? Ensure you have allowed a small margin for error, especially with elements such as mechanical guides for AGV docking. And, as much as possible, make sure you have fully evaluated your selected system, not just run it for a single day. Finally, run the AGVs. The more you use them, the quicker the return on investment!
Summary
AGVs offer exciting opportunities in broad ranging applications to increase efficiency, enhance worker safety and reduce material handling costs. It is because they can be applied in so many different settings however that it is important to understand the options available and gauge correctly how these fit with your organization’s specific needs – both today and into the future.