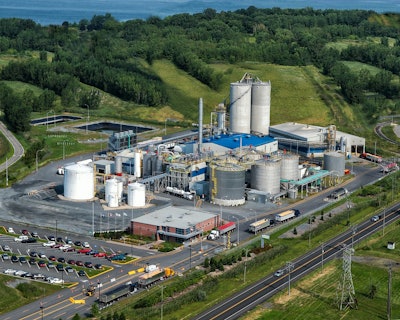
The novel coronavirus (COVID-19) disease is novel in more ways than just pertaining to health. It is also fundamentally changing our way of life as a society, not just for consumers but also for business operations. With shelter-in-place orders happening all through the United States and the world, many manufacturers are unable to normally operate production-wise due to restrictions or less of a need for their specific sector of goods. But, as non-essential goods are in less demand, other items such as personal protective equipment (PPE), ventilators, sanitizers and other essentials are drastically under-available.
Considering this situation, manufacturers have switched their production lines around to provide important items that the medical industry and consumers at home are in desperate need of. Automakers are manufacturing ventilators, clothing brands are making PPE, cosmetic brands are creating disinfectants and those that have teams of scientists for product development have turned to researching lifesaving drugs, testing kits and vaccines to fight the virus. While the decisions to switch products were likely made with the main driver being a want to help, the idea also helps these businesses stay afloat and maintain their employees when otherwise they might not have been able to. In some cases, stock in these companies is even rising a little bit in the markets.
But, how are these manufacturers able to make this change and what does this mean for the supply chain? The ability to change the products a large company makes, especially some that are heritage brands and have been in operation for almost 100 years, can be difficult in such a quick turnaround. But, these brands are doing it, and on top of that, are dealing with the production and shipments of large quantities of these new products.
One of the most important aspects of the product turnaround is practicality. Most of these brands are producing items not too far off from the products they were already creating, allowing them to keep their raw material supply chains the same as well as their logistics operations.
“The medical product needs due to the COVID-19 crisis are very specific and most manufacturers are responding via outreach to their communities and working with customer and distribution stakeholders to ensure supply under the current operating constraints,” says Cindy Bolt, senior vice president, Salesforce Industries. “However, some manufacturers are able to respond with products - either by an expansion of existing products or a pivot of manufacturing capability to meet current healthcare needs. Some common themes we are hearing include the repurpose of existing manufacturing and supply chain capabilities to their medical counterparts - companies that make products like filter medium, safety products, portable building structures are examples.”
Raw material providers are stepping up to make sure that their supply to these manufacturers remains steady in an effort to limit disruption. New partnerships between manufacturers and raw material providers are also being forged, and companies are finding ways to streamline and speed up the onboarding process to limit disruption as well.
“Leveraging existing suppliers is critical to ensure a smooth supply of raw materials and components,” says from Sanjay Rajan, supply chain expert and head of manufacturing at Tamr. “With the intense focus of governments in various countries, such as the defense production act in the United States, raw material suppliers have stepped forward and ensured this smooth supply. Qualification processes and supplier onboarding have also been sped up to help companies meet the demand.”
Keeping Safe
The industry is coming together to do what needs to be done, with competitors even partnering to help get important medical devices out the door.
But, as these companies work to scale out new products or operate in a new capacity, safety remains a concern. The safety and effectiveness of these items need to be maintained in addition to production safety and keeping employees healthy against the virus. How are they able to do this while also increasing their manufacturing capacities?
One company, Greenfield Global, known for making ethanol for the petroleum industry, has switched to provide alcohol for companies creating sanitizers. Greenfield has been taking precautions to keep its supply chain moving at its highest capacity while maintaining its products' and employees' safety.
Efforts such as prohibiting travel between facilities and keeping those who can working from home are important to keeping Greenfield’s business moving.
“We will not, under any scenario, fall below the product quality standards set by regulators, nor cut corners on the safety regulations in place for the production, packaging and transport of what is a highly flammable chemical,” says John Wilkinson, board of directors of Greenfield Global. “Moreover, beginning in March, Greenfield Global activated a company-wide response to the global pandemic. We ensured all staff who can work at home are doing so, including all administration and corporate functions. Previous investments in global corporate connectivity are reinforcing the digital infrastructure investment decisions we have made over the past four years.
“We also eliminated all employee travel, including between our production and packaging plants," he adds. "Our operations have been deemed ‘essential’ by the provinces of Ontario and Québec. Our employees have collectively dedicated themselves to following the advice of our public health authorities by keeping themselves, their families and fellow workers safe. This allows us to be there for the other essential service workers who are on the very front line of the battle against COVID-19. The bravery of these front line health care workers and other essential service providers inspire us every day.”
Technology During a Pandemic
While all this change is happening, regulations are also changing. Government organizations are working to relax some ordinances and regulations that are less important during the COVID-19 outbreak while creating new ones to help mitigate the spread. For instance, environmental restrictions have become more relaxed and restrictions on trucking weights for various CDL holders have been lifted, but social distances orders are still in order and non-essential businesses are still closed.
Compliance has become another factor that companies need to pay attention to even more.
The National Association of Manufacturers is one of many organizations working to make sure the new rules are clear, to help address the needs of all sides of the supply chain and create a clear line of communication with government agencies. On top of associations, technology has also become an important tool, opening the lines of communication, so that all members of the supply chain and manufacturing business are aware of what needs to be done and what cannot be done.
“It has also been exciting to see the use of our technologies in these efforts - we’ve seen some amazing examples of digital investments enabling manufactures to pivot in their response,” adds Bolt. “Maker of N95 masks are rapidly deploying our Quip collaboration platform across the value chain to manage the allocation of constrained supply. A commercial truck manufacturer is using our Quip collaboration platform to communicate directly with plant level employees on company policies and compliance in a rapidly changing environment. Another manufacturer that keeps our essential services like power plants working has leveraged digital engagement tools from Service Cloud to keep their technicians and field workers informed of new compliance policies as they perform work in the new COVID-19 world.”
Another technology that companies rely on to help produce these new products is 3D printing, helping manufacturers make parts of these items without needing much infrastructure. Other technology is improving communication beyond compliance, helping with allocation management and chatbots are even growing to help manage financial aspects of the operations. Many warehouses are also increasing the usage of robotics, to help protect their employees from contracting the virus.
A Post-Pandemic World
Because technology has been able to fill the gaps during this emergency, it is likely that following the pandemic there will be an increased usage of these tools, given that businesses have already needed to integrate these systems.
Other processes will change, like keeping partnerships within the United States or its country of business to help reduce the impact that another event like this can cause in the future.
“When it comes to manufacturing, we can expect more investment in automation especially with cheaper interest rates and access to capital,” says Rajan. “Artificial intelligence and machine learning adoption will accelerate along with automation. Organizations will also focus on reshoring, driven by the thought that the cost of offshoring is not worth the risk, especially for critical materials and components like chemicals, metals, and electronics. We also anticipate that the U.S. government will actively increase the list of critical materials that need to be produced self-sufficiently.
“Finally, with a decrease in consumer spending we can expect companies to focus less on product features, and more on maximizing total cost of ownership,” he adds.
The future of the supply chain might very well look significantly different than it did pre-pandemic. Businesses and lives have changed dramatically in this short time frame. Hopefully, everyone will continue working together to help keep things moving and deliver the items in need until life returns to normal. Until then, technology can help reduce the negative impact caused by COVID-19 and keep things moving.