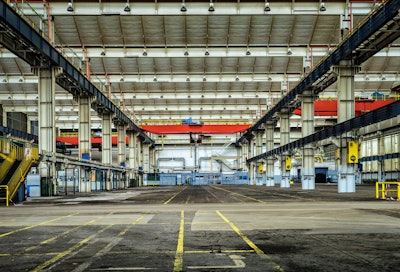
We live in an age where automation is advancing across nearly every industry. Self-driving trucks are being tested on our highways, drones are delivering packages, kitchen robots can whip up your favorite dish and robotic surgeons are performing complex surgeries. Along with these innovations come mounting fears over the future of the workforce. Some experts have predicted widespread unemployment in the coming years, with human workers being replaced by robotic counterparts and once-vital careers becoming obsolete.
Automation, however, can have quite the opposite effect on industries experiencing major labor shortages. Technology can fill existing gaps in the workforce by taking over repetitive, strenuous or dangerous tasks—ultimately creating safer, more productive work environments for employees and driving the emergence of new, tech-driven job roles. In short, automation is not eliminating jobs; it’s improving them.
Understaffed warehouses and overworked employees
This is particularly true in the warehousing industry where available labor is scarce. Many of today’s facilities are struggling to retain staff as aging baby boomers retire in droves and young jobseekers show declining interest in material handling careers. In the 2019 MHI Annual Industry Report, 65 percent of survey respondents cited hiring qualified workers as extremely or very challenging, while an overwhelming 91 percent ranked it as at least somewhat challenging.
Warehouse staffing shortages are further compounded by operational challenges surrounding e-commerce demands, SKU proliferation and seasonal order peaks. Altogether, these issues are particularly taxing on manual warehouses where all orders are picked, packed and shipped by hand. Existing staff need to work harder and faster, sometimes taking on extra hours and overnight shifts, just to keeps orders flowing out the door on time.
The ergonomic risks involved in manual handling
In a field where on-the-job danger is a daily reality, added strain on manual warehouse workers raises the risk of injury even higher. According to the U.S. Bureau of Labor Statistics, 5.1 out of every 100 warehouse and storage workers experience injuries or work-related illnesses each year, and many of these cases result in days away from work, job restrictions or transfers.
For manual order pickers, the most common safety risk is injury to muscles, joints, tendons and nerves, caused by repetitive, strenuous motions (twisting, bending, reaching, heavy lifting, etc.). Injuries can range from minor sprains, strains and pulled muscles to chronic conditions like repetitive stress injuries, repetitive motion injuries, musculoskeletal disorders, cumulative trauma disorders and cumulative trauma injuries.
Considering these safety risks, it’s no wonder that facilities have difficulty recruiting new workers to fill vacant positions.
Automated solutions to reduce risk while boosting productivity
Warehouse managers can protect their employees to an extent through preventative measures like proper ergonomics training and adherence to health and safety regulations outlined by OSHA. While better education and regulatory compliance minimize some risk, facilities can invest in automation to drastically improve ergonomic conditions, alleviate labor issues and enhance overall productivity.
Robotic hardware controlled by advanced software can take over the many demanding tasks of order fulfillment. From conveyers and automated guided vehicles (AGVs) to automated storage and retrieval systems (AS/RSs) and order picking systems, these systems run with utmost efficiency, fulfill orders with complete accuracy, and use significantly less space than a traditional, manual layout. Facilities can thereby keep up with increased fulfillment demands without putting humans at risk.
An automated layer picking solution, for example, combines gantry robots, a picking tool, and sophisticated software to pick goods in layered quantities from products stacked on the warehouse floor. The system can pick up one layer, multiple layers to create rainbow pallets, or entire pallet loads—completely eliminating manual labor from picking and pallet building. And due to its speed and flexibility, the system enables warehouses to easily keep up with the flood of orders during peak periods.
Further, a goods-to-man picking solution can automate the movement of goods stored in totes, bins or trays. An AS/RS, shuttle device and high-speed conveyor system work together to transport goods directly to workers at ergonomic picking stations where they can rapidly pick the required items for an order. This type of system can be up to six times more efficient than a manual operation, and its speed makes it an ideal solution for e-commerce fulfillment.
In the automated warehouse, humans are still key
With automation running 24/7, existing staff no longer have to risk injury by performing repetitive, physical labor or overexert themselves working overtime hours and overnight shifts.
Instead, tasks for employees are elevated into more sophisticated roles ranging from supervising automated operations and equipment maintenance to analyzing performance data and managing products with special handling requirements. Ultimately, the need for this kind of expertise will create new, tech-driven—and safe—warehouse positions that will attract a whole new generation of tech-savvy jobseekers.
Martin’s Famous Pastry Shoppe, Inc.® prioritizes safety and efficiency
Martin’s Famous Pastry Shoppe, Inc.® in Chambersburg, Pennsylvania previously used a completely manual process for fulfilling orders of its popular bread, rolls and baked goods. All products were picked by hand, so warehouse staff had to plan and prep orders hours in advance of dispatch. This process involved safety risks for staff who had to manually move products around the warehouse, and resulted in inefficiencies as order spiked during the busy summer season. Today, Martin’s Famous Pastry Shoppe, Inc.® has a fully automated order fulfillment process from storage to palletizing and loading. The facility can now schedule and prepare orders within just one hour of a truck’s arrival and is fully equipped to keep up during seasonal peaks—without compromising employee safety.
Industry 4.0 and innovation for the future
Today’s warehouses and distribution centers can leverage new technologies made possible by the dawn of the fourth Industrial Revolution, or “Industry 4.0.” By embracing automation, they can transition into more modern facilities where humans, robotics and intelligent software collaborate to cultivate a greater culture of safety and productivity. With numerous automated systems available today, look to a systems provider that can analyze your current operations and identify the best fit for your facility. The right solution will help you safely overcome the challenges of today and easily meet the demands of tomorrow.