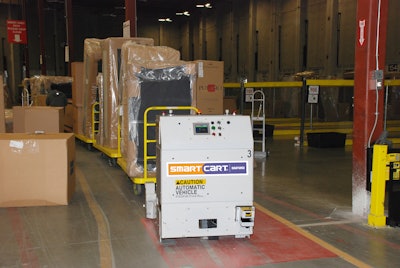
According to Consumer Reports magazine, the number of people buying appliances online has risen from 11 percent in 2015 to 14 percent in 2017. Another survey published last year by online payment processor Future Pay reported that 37 percent of respondents were planning to purchase appliances online. This confirms what we have been hearing from retailers: the items that people are purchasing online are getting bigger and bulkier, requiring managers to rethink the way they are staffing and structuring operations. In addition to appliances, online purchases now include items as large as fitness equipment, riding lawn mowers and furniture. Buyers are also expecting the same quick turnaround they get from their small purchases of books and toasters.
Staffing up
For warehouses designed around small parcel handling, manual handling of large items is usually the only immediate option. This is problematic for many reasons. Given the current low unemployment rate, finding qualified people to staff warehouses is not easy, especially during peak seasons. People capable of handling large items with warehouse experience are rare.
Compounding the problem is the fact that handling these items manually requires extensive bending, lifting and other motions that present ergonomic, safety and fatigue challenges. These requirements make it even more difficult to staff appropriately. Even with the most capable people on the job, some SKUs are difficult to handle without mechanical assistance.
All of this leaves warehouse operators with the choice of either rethinking their operations or losing revenue by not offering bigger ticket items. For most, the business opportunity is too great to pass up, as they look for ways to transition less labor-intensive solutions for handling larger, bulkier more efficiently.
Inverting the Pick Process
One of the most valuable process modifications that improve handling of large and bulky items has been inverting the traditional operating paradigm: bringing goods to the pickers instead of sending them out to find the goods. Automating the process eliminates the many miles the picker might otherwise travel around the warehouse transporting a small number of large items. It also frees them to devote more time to the less strenuous task of transferring items to outbound pallets for shipment and planning for the next delivery. Three of the most common means of transporting large items to pickers are automated or rail guided vehicles (AGVs and RGVs), tuggers and large conveyors.
- AGV/RGV: AGVs are transport vehicles guided by magnetic strips, RF/laser guidance or 3D mapping technology. RGVs are installed on travel and power rails within a facility. The guided vehicles receive direction from the warehouse management system and travel on their own to the storage area. AGV/RGVs are often designed to spec for the loads they are carrying in the warehouse and can be designed to handle loads up to several tons. They may be equipped with forks or robotic arms that pull pallets or cartons from automated storage and retrieval systems (ASRS) and bring them to a picker who will supervise transfer of the goods to the appropriate technology for shipping. While the picker is then processing that order, the AGV/RGV is simultaneously working on the next.
- Tuggers: Tuggers are a specialized subset of AGVs that use a set of carts to haul multiple pallets. Because tuggers can haul large volumes of items, they can be especially valuable for large warehouses with many SKUs. Once the person transfers the order from the tugger to an outbound pallet, they push a release button sending it back for the next pick, delivering the same efficiency benefits of parallel operations as AGV/RGVs.
- Conveyor: Powered by rollers or drive chains, conveyors can be an efficient means of transporting large and bulky items. Because they require relatively permanent installation, conveyors are most suitable for established lines that are processed continuously in a relatively compact layout. As the storage area grows in size, it may be more efficient to use AGV/RGVs or tuggers to bring goods to pickers.
Automating Pallet Management
In addition to inverting the process by which pickers receive large goods, pallet-loading or unloading might also be enhanced for handling larger items. Adding vacuum assists or mechanical grippers to robotic arms can help in lifting and moving of larger objects. An arm equipped with a vacuum head, for example, might help lift a carton from the top, while other arms clamp around the sides.
Rising to the Challenge
The proliferation of large SKUs compromises warehouse space as well. At the same time as they are automating storage and retrieval, some large retailers are launching initiatives to reduce area dramatically, while others are building up. Instead of the 35- to 40-foot ceilings typical of warehouses, some retailers are deploying ASRSs with ceiling heights of more than 120 feet.
Selecting the Right Technology
As the mix of larger objects changes, most warehouses will transition to various combinations of manual, semi-automated or fully automated operations. Determining the right mix starts with a data analysis, such as an ABC analysis. The analysis begins with identifying “A” movers, rated by velocity and cubic volume, followed by the “B” and “C” movers and so on. This results in a Pareto curve, which typically follows the 80/20 rule, with the extremely fast and slow moving SKUs at each end of the curve and most in the middle. When mapped to the levels of automation now being deployed, analysis of those curves can help determine where automation improvements could make a difference.
Optimization through Software
Fully-integrated supervisory control and data acqusition (SCADA), warehouse management, control and execution systems can further optimize the handling of large and bulky items. A warehouse execution system (WES), for example, can assist in analyzing data from the warehouse control system (WCS) and WMS, to sequence orders based on their weight and dimension, maximizing the number of items that can be handled safely per pick, pallet and picker.
Orders can be grouped by ABC classification, size, delivery method or whichever parameters drive company KPIs. These can help determine which items might be more suitable for automation, which are more suitable for manual handling and which might require a hybrid approach. Optimization can be refined through integration with SCADA systems that track where each order is at in the system, whether it is in storage, at a pick station or on the shipping platform. WES analysis can then spot trends and bottlenecks for correction and see which areas correlate with larger SKU handling. These systems can also capture data and pass it back to order management systems, which can potentially evaluate cost and benefits of large item handling strategies.
Bigger Things to Come
As consumers grow to trust online retailers and warehouses ramp up delivery with the speed they expect, ordering big tickets online will continue unabated for years to come. Innovations that bring automation to the forefront will become the norm, and the results will be a safer, more efficient load handling.