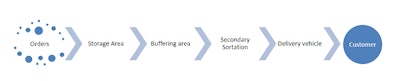
For suppliers that serve customers through regular delivery routes, the efficiency with which they load and unload delivery vehicles can have a tremendous impact on the bottom line. Companies making regular deliveries to convenience stores, grocery stores, restaurants, cafeterias, hospitals, schools and numerous other institutions can benefit greatly by ensuring that their shipments go onto trucks in corresponding order to delivery requirements.
In warehouses with little or no automation, the loading and unloading of delivery vehicles can be a haphazard affair. At each stop, drivers can spend unnecessary time searching and shuffling to pick the goods needed to fulfill the order. In addition to wasting valuable talent, this can reduce the number of daily deliveries, cause delays and introduce error.
Randomly packed delivery vehicles can also create additional order sorting and parsing work on the receiving end, presenting potential possible customer satisfaction issues.
Many companies with automated storage, retrieval and sortation technology are now avoiding such problems by employing technology that automatically arranges deliveries for synchronized loading and unloading. Companies applying automated sequencing can more than triple delivery productivity, reducing costs and increasing customer satisfaction.
Automated Sequencing Overview
Automated sequencing typically involves moving coded items from a storage area to a buffering area where automation storage and retrieval systems (ASRS) or other sortation technology implement sequencing algorithms customized to the shipper’s needs.
The process typically begins with a picklist of items intended for delivery in a specified time period—usually a day. The list would be generated by warehouse management system (WMS) software based on orders from multiple customers or information gathered in previous shipments. With a list in hand, teams of pickers walk through the storage area, selecting cartons, totes or eaches, depending on the size and shape of the product.
This initial picking is blind to the eventual sequencing requirements. Pickers have much ground to cover, so their focus is on optimizing travel time, not loading or delivery. If, for example, 10 orders call for the same product, they could be picked at the same time. Decoupling the picking from the sequencing in this way optimizes the efficiency of each picker’s travel time, eliminates queuing of pickers and consolidates the sequencing itself into a more manageable space.
As new items arrive to the buffering area, case by case, the barcodes are scanned into warehouse execution software (WES), which is programmed with the intended delivery sequence for each order. When each order is fully buffered, a combination of motion control technologies automatically stages it for loading in the proper sequence. The exact configuration of the sequencing technology varies considerably from user to user, depending on a number of factors, including the size of the goods, the volume and each company’s business objectives. Based on these, sequencing architectures involve various combinations of ASRSs and sortation technology.
ASRS Shuttle with Secondary Sortation
One of the most versatile configurations is based on integrating an ASRS shuttle with a secondary sortation system. As operators pick products, the system conveys it into the shuttle buffer. The shuttle stores the product optimally for later sequencing.
When shipments are ready to be loaded into trailers, the shuttle buffer sequences product onto the outbound conveyor. Multiple shipments are then conveyed to a sorter in the dock area. Once sorted, product is conveyed from the sorter to shipping downlines based on the specified route. Orders may be fluid-loaded onto the truck with a semi- or fully automated extendable conveyor, and then hand-loaded into the trailer. Some applications may utilize autonomous robotic truck loaders.
This approach, in which multiple loading docks may share the same sorting system, is very cost-effective in that one shuttle buffer can serve multiple loading docks at once. It may not, however, be ideal for high-volume operations since progress at each dock depends on the efficiencies of other loading docks. If one of the lines backs up, everyone’s access is affected.
Direct-to-Dock Sequencing
One approach to loading is direct-to-dock sequencing. Once a shipment is ready to be loaded into a trailer, the shuttle buffer sequences product onto the outbound conveyor. This conveyor is destined for a single trailer, which eliminates interdependencies among loading docks.
Sequencing with Conveyor Technology Only
Another approach might accomplish the sequencing with no ASRS at all, using only conveyor sortation. A shirt manufacturer producing shirts of various colors and sizes for delivery to local merchants, for example, was grouping orders manually, by route only. Once delivered, it would take as much as five or six hours to reconcile and receive the delivery. Using a three-stage sortation buffering process, Wynright consultants reduced the amount of time it took to reconcile and receive a shipment to less than two hours. As the items moved from one pre-sort area to another, they would be sorted by SKU, color and size, in the exact order that the customer required them. The white shirts, for example, might come out first, ordered in small, medium and large sizes, etc.
Orders could be filled as soon as they were received at the warehouse and ready for loading when the driver arrived. The system also generates a manifest that provides a checklist for each stop. Sequencing without an ASRS can reduce capital investment, but it may require additional synchronization of picking, which must be factored in.
Other Factors Impacting Sequencing
What we described here are relatively standard approaches to sequencing. For most companies, the applications can get complex integration factors that are unique to their business. A company shipping a large variance in product weight might also have requirements that load heavier items at lower tiers on the truck. Algorithms for a company shipping groceries might also reflect Food and Drug Administration (FDA) compliance requirements, like packing beef and chicken meat below produce. Each industry has its own set of unique requirements that affect sequencing.
Getting Started
Whether a solution involves ASRSs, conveyor and sortation, advanced packing algorithms or anything else, of course, depends on the business requirements of each shipper. For most companies, the discussion begins not at the loading dock, but with a discussion of the warehouse automation needs in general. Sequencing needs may factor in as one cost justification for a broader automation strategy.
Within that context, clients usually design their sequencing strategy in collaboration with a warehouse systems integrator or technology vendor who has extensive experience in customizing sequencing. It would typically begin with detailed analysis of the existing shipping and unloading processes, total SKUs, frequency with which each is delivered, truck capacity, average delivery time, numbers of orders that could be processed in a day, etc. It would then work with the shipper to create success metrics and design the process to optimize deliveries to achieve those metrics.
Granted, automation sequencing may not be for everyone. The discussion of whether it would work for you might begin with a calculation of the value of adding additional delivery stops to your drivers’ routes each day. That should give you a pretty good idea of what level of expense might be necessary in order to achieve that benefit. If you are already using ASRS technology, this can be a way to maximize your return. If not, this might be one good reason to consider it.