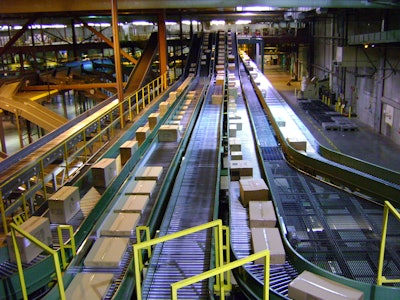
Warehouses are like snowflakes—no two warehouses are perfectly alike, nor should they be. Because warehouses are the perfect example of form following function, every warehouse should have a unique design based on its workflows, material requirements, staffing, and need for omnichannel flexibility and scalability. Like the design of a warehouse, the reasons for updating or designing a new distribution center (DC) are also many and multifaceted.
Jason Minghini, vice president of best practices at Kenco Logistics, cites omnichannel as one of the main drivers for changing customer order patterns and, as a result, changing needs for the warehouse or DC. Because of the rapid rise of e-commerce and m-commerce, more companies are looking to cut out the middleman and go direct to consumers through the Internet to compete with Amazon and similar industry titans, which is increasing consumer preferences for fast delivery times and impeccable customer service.
As a result, many DCs must reinvent themselves to stay relevant in the marketplace. This also means there are more single items as opposed to full pallets, further complicating order picking and slowing down the order fulfillment process. All of this change is happening, while the pressure to minimize costs, and maximize service levels and profits remains a constant. Another factor for redesigning or retrofitting a warehouse is the prevalence of automation technology in the face of a talent shortage. Due to a lack of workers, automation’s return on investment is skyrocketing and making more economical sense.
Getting your warehouse design right the first time is almost as important as getting your warehouse design right. An organization should first determine what goals it needs to accomplish with the retrofit or new design, conduct analyses and then execute, or there will be a high price to pay. Minghini warns, “It costs a lot of money, time and resources to retrofit or change the design of a facility. If you don’t get it right the first time, you will have wasted a lot of the organization’s money and potentially impacted the customer’s experience with their clients.”
What’s Hemming Your Warehouse in?
The options to update or design new warehouses are infinite, so the best way to start to determine warehouse optimization is by identifying the constraints of the existing or prospective warehouse space. There are many constraints to evaluate before ever hitting the drawing board. According to Joe Hutter, senior vice president of business development, and Chris Graver, director of intralogistics design at Wynright Corporation, these include:
• Capital. Companies need to know their budget limits for a new or retrofit project.
• Space. Existing buildings typically have physical limitations that impact the decision to retrofit or build new. The need for more inventory to support distribution may require more space than exists or can be built on an existing site.
• Availability of labor. If labor availability is a constraint, then the organization may search for a different location within a region where labor conditions are more favorable.
• Technical ability of labor. Is the current technical ability of the operations and maintenance teams in line with the planned level of technology? Is additional training required if additional levels of technology are planned?
• Information systems. Are there gaps in functionality, connectivity and visibility of the current business and information system versus the requirements for the new system?
• Age of existing assets. Are the mechanical, control and software systems all currently supported, and able to be updated with current technology? What is the reliability of the current equipment?
Data and Metrics to Validate Your Retrofit or New Design
Hutter and Graver summarize the steps to determine the optimal warehouse design—by defining the best design and minimizing design risk—as follows:
• Data analysis, which includes data validation.
• Understanding current process and future plans.
• Developing the design criteria for the new DC.
• Evaluating applicable technology, which can include conventional and automated technology.
• Space and capacity planning.
• Determining viable operating scenarios.
• Testing and evaluating alternative concept(s).
• Simulating the concept(s) to further validate the design.
• Selecting the optimal solution.
Simulation is a common warehouse design tool as it facilitates visualization and can model what-if scenarios, including whether the design can accommodate future growth, which decreases the risk of the project’s success. Hutter and Graver explain, “Simulations are typically developed in 3D and then animated to reflect the dynamics of the design concept. The animation provides the organization with a view of the future and team members can quickly identify areas that may require further design. Operations are complex and, typically, static spreadsheet models cannot adequately identify constraints or logic and controls issues.
“Simulations provide organizations the ability to model their future operation by inputting actual or synthetic order information, and then determine whether the solution they selected will meet future needs. In addition to the enhanced graphics and animation, simulations generate output data over the simulation run, which can be analyzed to determine the future performance of a design.”
Minghini concurs that simulations should be performed before design implementation, so organizations can analyze the impact of different designs on key performance indicators (KPIs), such as material flow, congestion, travel distance, velocity of the product, order profiles, product segments, storage density requirements, regulatory and/or government requirements, and service requirements from the customer. He says, “By doing simulation work, the best possible design can be chosen to match current order profiles.”
Hutter and Graver also suggest using historic data to inform future decisions, such as transaction details from previous years—customer orders, receiving data and inventory profiles, to name just a few. Other key metrics to consider include growth projections, head count, customer service levels, order accuracy and total productivity.
Why Retrofit or Redesign?
While there are myriad reasons to retrofit or redesign an existing warehouse, the primary drivers, according to Joe Hutter, senior vice president of business development, and Chris Graver, director of intralogistics design at Wynright Corporation, are:
• Lease negotiations. If a building lease is going to expire in the next 18 to 24 months, then organizations may partner with real estate professionals to begin searching for alternate sites to ensure that they are in a position to minimize their future cost per square foot, whether they renegotiate to stay in their existing facility or relocate.
• Labor costs. There is renewed pressure for minimum wage increases, which is affecting decisions regarding location and automation. Companies may evaluate higher levels of automation to offset rising labor costs.
• Labor availability and skill levels. There are concentrated areas of distribution centers throughout the country because these areas are ideal for optimizing supply chain costs. Companies are facing issues of labor shortage, and therefore, may look toward retrofitting or greenfield options that require less labor.
• Growth. Companies may run out of space due to sales growth and the number of SKUs they need to carry in inventory.
• Sales channels. Many distributors are confronting challenges due to changes in order types. For example, retailers are shifting more of their capital to e-commerce as sales are increasing in this channel much faster than for brick-and-mortar stores. E-commerce demand is dynamic and driving high service levels, in addition to increasing the handling costs of unit level orders.
• Safety. Safety is of increasing importance in the workplace to improve associates’ well-being and productivity. Related to safety is the drive to eliminate hazardous and repetitive work, and to improve ergonomics.
• Inventory. There is a continuous effort to optimize inventory levels across all industries. In distribution, inventory management tries to balance the countervailing metrics of lower days of inventory on hand and higher order fill rates, along with managing replenishment methods and cycles.
The Powers that Be Can Be Omnipresent
Uninterruptible power supply systems condition incoming power to eliminate the risk of power disruptions and keep equipment fully operational.
By Todd Kiehn
In mission-critical operations, even the slightest power disruption can have major consequences in terms of time, money and resources. These disruptions are becoming more of an issue as today’s industrial and manufacturing facilities turn digital with ever-increasing levels of automation being put in place. To address these issues, uninterruptible power supply (UPS) systems condition incoming power to eliminate the risk of power disruptions and, in the event of a power failure, keep equipment fully operational until the critical load can be transferred to a generator.
Every facility has a unique set of needs, so there isn’t a one-size-fits-all solution. Several factors should be considered when selecting a UPS, including system performance, reliability, environmental impact, maintenance and replacement cycles, cooling requirements and, of course, total cost of ownership (TCO), which includes initial and operating costs over the product’s useful life. Before selecting a UPS, operators should do their research and ask for spec sheets, customer references and third-party product comparisons.
A number of energy storage technologies are available for use in UPS applications, including conventional batteries, as well as less common options, such as flywheels and diesel rotary devices. Battery-based UPS systems typically use valve-regulated lead-acid (VRLA) batteries to store energy, whereas flywheel and rotary systems use kinetic energy.
Battery-based solutions are the traditional choice because these systems have been deployed in mission-critical environments for more than 50 years. There’s a perception that selecting a battery UPS is less of a risk. Batteries can also provide five to 30 minutes of backup time, which provides a psychological benefit to customers. However, that backup time has significant costs, including initial cost, lifetime operating cost and environmental impact, and is becoming less important with advances in electrical infrastructure. As a result, more and more users are looking for ways to reduce their dependency on batteries.
There are many risks involved with battery UPSs. Batteries are comprised mainly of toxic lead acid, which can be harmful to both people and the environment. Additionally, these systems must be housed in cabinets that take up a great deal of space, and do not fare well in environments without precisely controlled temperatures. The maintenance and cooling involved with battery UPSs increases the overall cost of operation and carbon footprint. Batteries also degrade over time, and require replacements every four to six years or sooner depending on usage.
Flywheel UPS systems have high operating efficiency and permanent energy storage, meaning the flywheel never has to be replaced during its 20-year life span. These two inherent advantages are the main reasons the product delivers up to 40 percent in TCO savings and produces 90 percent less carbon emissions than battery UPSs. The systems are also proven to be 12 times less likely to fail than conventional offerings. Flywheel UPS products can also operate in higher ambient temperatures and are more space efficient, meaning operators can place a system directly on the shop floor closer to the load it’s protecting. This also eliminates the need for dedicated UPS and battery rooms.
As concerns over pollution and global warming grow, interest in cleaner, sustainable technologies will also increase. Flywheel technology is more efficient and environmentally friendly than conventional battery UPSs. Plus, square footage is always a premium in industrial settings, which bodes well for flywheel UPSs and other hardware that is more compact. No matter what kind of UPS system is selected, however, your facility will be powered, eliminating the risk of downtime.