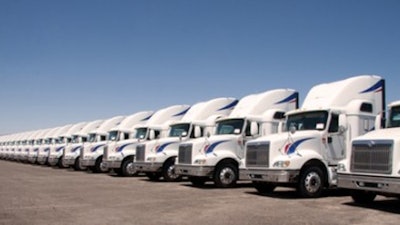
For businesses that ship goods on pallets, the promise of “on-time delivery” is becoming harder to keep. When shipment orders surge during the holiday season, the entire industry faces heightened pressure and scrutiny for accuracy, timeliness and loss and damage.
Given the high stakes and high volume, one might think that the trucks seen on the road this time of year are overflowing, barely keeping up with the hundreds of millions of pounds of freight moving between domestic hubs. Most assume that shippers are boxing each other out to fill a carrier’s 26-pallet capacity, and that every diesel-burning truck on the interstate is packed with inventory.
If only supply and demand worked so simply. In reality, shippers know it’s a fool’s errand to sync their inventories and fulfillment schedules perfectly with demand. The U.S. market for palletized goods has grown exponentially over the last 25 years, but without corresponding innovation to bring multiple shippers and carriers together.
It’s led to the question: Why are half of big trucks still moving only half-full?
The solution to that massive inefficiency is shared truckload (STL). Technology makes it possible to find the most efficient option for pooling every kind of load — not just during a holiday surge, but at the point of sale for every fulfillment, 365 days a year. Filling the empty space in trucks can fundamentally change the way our fragmented industry moves freight.
To see how shippers can take advantage of STL right now, here’s why their traditional options are particularly inefficient during the holiday rush.
Why businesses still pay to ship air
Overworked and underpaid final-mile delivery drivers aren’t at fault for delays during the holidays. In the hub-and-spoke model, every terminal consolidation point introduces a two-in-five chance of damage, delay and loss.
Understandably, as pressures rise to get goods off the shelves and onto trucks, shippers lean toward more reliable options that ensure on-time and damage-free deliveries.
That leaves them with the first of the freight industry’s two traditional offerings: full truckload (FTL), which delivers a 96% on-time success rate. The problem: reserving a whole truck often requires the shipper to buy more space than they need — meaning they’re paying to ship air. At any given time, about half of those trucks are running half-empty.
Alternatively, shippers could opt for less than truckload (LTL), but roll the dice by taking an indirect route. That might save money, but at the cost of on-time delivery and accuracy. When Drive Research polled 200 shippers earlier this year, every single LTL shipper reported freight delays — with some shipments arriving up to six days late. About 100% of LTL shippers also had to replace damaged or missing goods last year.
It’s a trap of two inefficient options. Among FTL and LTL shippers, not one said they were 100% satisfied with their current shipping process. Still, the goods must move. Shippers face constant pressure at the point of sale to deliver on time at all costs (last year, the average shipper’s on-time/in-full fees totaled over $290,000, according to the same Drive Research study). The lack of options pushes businesses to reserve full trucks regardless of whether they can actually fill them.
The freight industry’s empty-truck problem affects more than marginal costs. The most recent data shows that trucking emits 442 million metric tons of CO2 per year. Electric vehicle fleets will alleviate some of the diesel, but without an efficient way to use their full capacity, they’d still be forced to choose between two suboptimal options.
Holiday surges and the climate crisis remind us of a year-round need: a smarter mode that fundamentally changes in the way freight moves. Over the past decade, we’ve built and patented the technology to meet that demand.
Shared truckload: A third mode is a win-win-win for shippers, carriers and the planet
While full truckloads can move one shipper's freight faster, STLs move multiple shippers' freight at the same speed, on the most optimal routes possible. By combining shipments in one truck driven by a single driver all the way to one destination, STL gives shippers the peace of mind for safe, on-time deliveries that they demand.
Having that security matters for businesses of all sizes. Growing up, my family’s freight forwarding businesses mainly focused on moving furniture and other household items, particularly for U.S. service members and their families. That meant that our annual “holiday rush” typically kicked off around summertime. If we had today’s STL options back then, pooling our freight would have alleviated much of the seasonal stress and planning.
Freight brokers have tried for years to pool shipments, but lacked the technology to do it efficiently. Now, we’re able to match data from multiple shippers and carriers who are driving in the same direction. On a daily basis, probabilistic pricing engines and machine learning look at variables like timing, routing, product type, and weight. Unique pooling algorithms can predict inventory opportunities and bundle hundreds of part-size shipments.
Beneath the complex algorithms lies a simple cost incentive for all parties: shippers only pay for the space they need and carriers can earn more from every linear foot of capacity.
While more deliveries are getting where they need to go, when they need to get there, trucks aren’t burning diesel to ship air, and emissions go down by as much as 40%. Here’s an example of STL’s environmental impact at scale:
● During the holidays, individual consumers will produce an additional 1,400 pounds of CO2.
● When truck drivers take fewer left turns, emissions go down by about 100,000 metric tons a year.
● If America’s LTL industry committed to sustainable freight shipping by using STL, market valuations show us that carbon emissions would fall by over 10.5 million metric tons a year.
Given the urgency of the climate crisis, the STL solution is about more than just quality and cost. With every pooled freight fulfillment, we can prove that reducing emissions isn’t a zero-sum game. Everyone benefits from lowering emissions and it doesn’t have to come at a disruptive cost.
A smarter, more sustainable supply chain
After a year defined by unpredictable labor disruptions, diesel fuel shortages, inflation and ongoing uncertainty caused by the pandemic, holiday surges remain as predictable as ever.
And knowing that every industry will need to scale down emissions more aggressively, shippers and carriers can agree that it’s not just financially unjustifiable to keep sending half-empty trucks across the country. If STL helps businesses profit from more sustainable shipping, how can they afford not to?
As electric vehicle fleets come online, make sure they’re filled to capacity as well. Pooling more freight at scale provides a smarter, more sustainable blueprint for all modes across the supply chain. For trucks, that future is here.