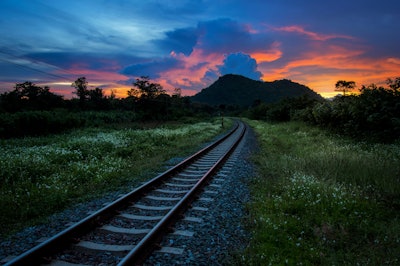
The country is breathing a collective sigh of relief as a rail strike was narrowly avoided this past year. While we were able to steer clear of it this time, it got many people thinking about what could have been if the strike ensued and the potential for something similar to happen in the future.
This consequential event was a wakeup call for many, especially those involved in supply chain and logistics. Right now, the best thing supply chain professionals can do is take this time to prepare and plan for disturbances or disruptions like this, as such an event would have significant impacts and far-reaching implications on the supply chain, economy and ultimately each one of us.
The potential impact of a rail strike
If a rail strike were to take place, the entire country would feel the impact almost immediately in one way or another. The United States is already facing a massive shortage of approximately 80,000 truckers. If the rail system shut down, it would take about 467,000 additional long-haul trucks per day to compensate and move all railroad freight. Supply chain players must be ready for this very real threat and understand how it would impact logistics.
Additionally, a rail strike would affect all industries on a micro and macro level. The chemical, pulp and paper industries all rely heavily on rail transportation. The pharmaceutical industry relies on these other industries for the manufacturing of medications and packaging. In this specific case, the impacts on consumers would be severe as it can result in patients receiving a potentially lifesaving or life-sustaining medication late or not at all. Other industries would face similar challenges, but the end result would be less dire. Such as a customer not receiving their new pair of jeans or a book in the mail. Each industry would face its own unique set of challenges, and each would have to work through what preparedness looks like for their specific business model, needs and customer base.
Preparing for the future
There are many ways to prepare and establish processes right now that would help reduce impacts in the event of a future rail strike. Some examples include being ready and able to shift away from the use of just-in-time models, avoiding reliance on a single sourcing of products, investing in a specialty third-party logistics partner, changing shipment quantities and locations, and implementing robust business continuity and disaster preparedness plans.
First, stakeholders need to voice concerns immediately and develop contingency plans. Supply chain professionals must consider immediate impacts and contemplate possible implications for materials. Evaluations of current process and heightened communication amongst leaders will be critical. Take extra time and care to build out new plans, ensuring that they consider even the smallest details and carefully think through each step. If a business typically ships a high volume of products to a few select locations throughout the country, then create a detailed plan that maps out what it would take to pivot shipping a smaller quantity of products to many locations.
The most important thing supply chain professionals can do to prepare is to ensure that the business is not overly reliant on a single component, whether it be packaging, products, manufacturers or modes of transportation. Creating relationships with different vendors and utilizing multiple contracts is a great strategy to invest in. Sourcing multiple vendors takes a significant amount of time and resources due to conducting initial research, building and nurturing business relationships and finalizing any necessary contracts. This is one of the many reasons why companies should use this business-as-usual period to implement these protocols and create preparedness plans with a sense of urgency.
To ensure smooth supply chain operations during unstable and unpredictable times, manufacturers and distributors must think outside the box and take steps right now to address and predict future impacts to mitigate effects when a crisis does arise. This highlights the need for all stakeholders across industries to be aware of possible disruptions, the need to be innovative and the importance of providing leadership.0