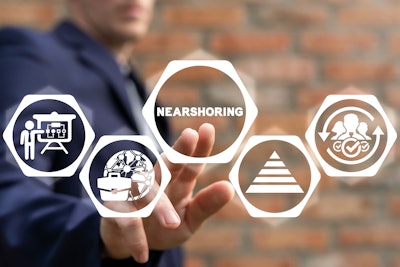
Last year, China and Hong Kong together supplied more than 40% of imports to the United States. It’s a telling figure that U.S. trade experts are eyeing with trepidation given some of the supply chain issues that have plagued the Asia-Pacific region in recent years.
Major ports in China are facing big delays, up to a 34% increase in ship waiting times in the last year. This is due to a combination of labor shortages and power rationing dictated by Beijing. And shipping fuel costs were up 66 percent in nearby Singapore, a major refueling hub for trans-Pacific shipping routes. Disruptions and increased costs have led to shortages of critical goods in the United States, for example, the lithium batteries that power smartphones and laptop computers.
Fortunately, advancements in logistics technology have paved the way for a decentralization of production and freight. For advanced economies like those of the U.S. and Europe, this means they can be less dependent on the flow of goods from China by instead re-anchoring supply chains in their own backyards.
For the U.S., this emerging practice of nearshoring will necessitate significant investment in Mexico-based manufacturing and freight hubs. But these efforts have the potential to pay for themselves and more in massive dividends. By diversifying the methods by which foreign goods reach the U.S., we can lessen supply chains’ susceptibility to any single geographic disruption. And we can also reduce costs associated with overseas shipping by pivoting to cheaper, quicker overland freight.
Localizing Logistics
To effectively implement nearshoring in Mexico and successfully leverage the country’s supply chains, it’s essential that U.S. importers build relationships with local logistics providers. These are professionals who understand with native fluency the nuances of Mexican customs, regulations, and infrastructure.
Importers should conduct thorough research to identify reputable logistics providers in Mexico with strong track records of successfully handling cross-border shipments. But it’s important to look even more closely at those potential partners that have experience with the specific goods they plan to import.
For example, importers dealing in food items should probably tailor their research to logistics providers that have adequate refrigerated-shipping capabilities. Likewise, there may be certain tariffs or fees attached to the shipment of specific goods, such as car parts. Car part dealers looking to import from Mexico should hire logistics providers that have experience navigating these fees.
A great way to find good local providers is by attending trade events and networking functions in Mexico itself. Major cities like Mexico City and Monterrey will play host to a variety of trade shows, conferences, and other events at which U.S. importers can meet potential logistics providers face-to-face.
Importers can complement on-the-ground reconnaissance with word-of-mouth referrals, too. Using platforms like LinkedIn, they can reach out to U.S. businesses that have experience with cross-border logistics in Mexico and ask for recommendations. They can also utilize international groups like global logistics networks, which offer a more streamlined process for identifying contacts, although these networks are often only accessible after paying a membership fee.
Upgrading Supply Chain Visibility
Importers should also assess potential Mexican logistics partners on the basis of whether they’ve integrated certain new technological developments into their freight operations. Internet of Things (IoT) devices and sensors, for example, can be used for real-time location tracking of goods. Installed in containers or embedded with shipments, these sensors can detect and alert importers and exporters of potential risks, like delays, route deviations, or adverse transportation conditions. Armed with this information, importers are better equipped to communicate realistic delivery timelines to vendors and other stakeholders.
These sensors can also monitor environmental conditions of freight containers, tracking temperature and humidity levels, for example. This data helps identify deviations from optimal conditions en route and allows importers to take quick corrective action to maintain product quality. For example, truckers can be notified immediately when refrigeration units break down so they can pull over to have the equipment serviced. This could potentially save importers a lot of headache and money spent dealing with lost inventory.
Blockchain technology can also contribute to supply chain visibility. Blockchain provides an immutable and transparent record of every transaction and movement in the supply chain, thus creating trust among stakeholders and helping to prevent fraudulent activities or unauthorized changes to records. Blockchain's decentralized nature allows secure data sharing and collaboration among supply chain partners without the need for a central authority. This facilitates seamless information exchange and reduces the possibility that a single mistake or unauthorized modification can taint the record.
Blockchain can also help both importers and exporters meet regulatory requirements in the U.S. and Mexico by providing a comprehensive audit trail of products' journey from Point A to Point B. This traceability is particularly crucial for industries with strict trade compliance standards, such as pharmaceuticals and food. Finally, IoT-enabled tracking devices and blockchain's transparent records can ultimately expedite customs clearance processes, reducing delays and potential bottlenecks at the border.
Predicting and Mitigating Problems
Even where technology can expedite import processes or reduce delays, it’s important that importers nearshoring in Mexico establish robust contingency plans to handle other disruptions. For instance, labor shortages on either side of the border can mean fewer truck drivers on the road, or fewer customs officials processing cross-border traffic. Political instability, weather events, and public health crises can likewise shut down U.S.-Mexico border crossings. These shutdowns, even brief ones, can have major implications for importers’ business operations.
Importers should therefore be sure to diversify manufacturers and logistics partners even within Mexico. Relying on a single source of goods or a single manufacturing location can be risky, and diversification reduces the impact of isolated disruptions on the entire operation. Importers should also keep a safety stock of critical inventory, if possible, at strategic locations to ensure continuity of supply. Safety stock can bridge the gap between demand and supply when unforeseen events affect production or transport.
Importers should work with nearshoring partners to identify and establish alternative transportation routes too. This can help avoid disruptions caused by natural disasters, road closures, or other issues. Having backup transportation options ensures goods can be delivered even in the middle of a disaster.
Just as we can count on the oceanic tides changing day in and day out, we can expect the global center of gravity in trade to shift too. But we are perhaps standing at an inflection point in this evolutionary chain. Nearshoring presents an opportunity to totally rethink how we approach global shipping and trade.
We can move away from systems that relied on big, dominant trade powers, and towards a decentralized network that allows advanced economies to help develop the supply markets in their own neighborhoods. And with the right contacts, technology and planning, U.S. importers and their Mexican partners stand to benefit in big ways.