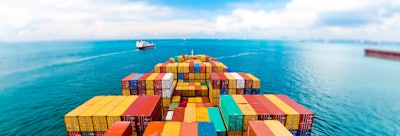
Shippers are spending more time navigating an unusual ocean contract season. Historically, April would have marked the end of contract negotiations, but this year, 2023 ocean strategy discussions stretch onward, creeping closer and closer to another important season – peak season. This is in part due to a softer market which is affording shippers the time and flexibility needed to approach the planning season with extra care, following 2-plus years of a constrained shipping market.
While this year’s balance of supply versus demand in the ocean market has helped reduce shipping costs, prices are not the only thing on shippers’ minds. In a recent global survey of C.H. Robinson shippers, respondents said ‘having enough transportation capacity before the market tightens again’ is one of the top three risks to their supply chain this year. And, when asked what’s critical to their success, nearly half said ‘optimizing my supply chain while the market is softer.’
Understanding evolving ocean market factors and how they impact goals such as these, in the short term and long term, will be key to building a stronger supply chain long term. Here are five key trends to watch this year:
Lower demand across most global trade lanes has many implications. Capacity can still be hard to find, and delays are still common, so plan ahead.
For shippers, planning out their ocean shipments this year may have seemed simple: decreased demand means there is plenty of capacity for weekly services. However, reliability is what shippers should be watching closely. While lower demand across multiple trade lanes has created ample capacity for carriers to work with, it also leads to blank sailings. As many shippers plan for continued low demand through the rest of the year, they should also plan for their freight to potentially be delayed due to parked vessels and/or blank sailings. Delays from blank sailings can add weeks to transit times and create a domino effect of supply chain issues if shippers don’t plan properly.
In addition, slow steaming (when carriers operate cargo ships at slower speeds to lower fuel costs and emissions) can add approximately 3-6 days to transit times. On the EU-Asia trade lane, nine vessels have been introduced to maintain weekly capacity. While these additions improve schedule reliability and may suggest additional capacity, the practice of slow steaming is actually reducing global capacity as vessels will be able to carry fewer containers per year. Overall, shippers, especially those with time-sensitive cargo, should prepare for extended lead times and develop a supply chain strategy with flexibility in mind.
Ports are not immune from disruption. Be ready to shift ports as needed.
Over the last few years, many shippers shifted freight away from the U.S. west coast to the east coast to avoid backlogs and labor negotiations. Statistica reported that the Panama Canal, which is used for Asia- U.S. east coast routes, saw a record number of ships in 2022. As west coast labor negotiations are predicted to end soon, most shippers haven’t gone back, and some may not be planning on it.
Due to drayage issues and costs associated with intermodal transport, shippers with destinations closer to the east coast may not return to their preferred port pre-pandemic. A recent CNBC supply chain survey found that nearly a third of logistics managers at major companies and trade groups didn’t know how much cargo they would return to the west coast when a labor deal had been reached. 18% of respondents said they would only bring back 10% of their diverted trade. As the last few years have proven, ports are not immune to disruption and shippers may find themselves needing to shift ports quickly to maximize efficiencies and lessen the risk of delays.
LCL is still a key strategy to consider.
Less-than-container load (LCL) was a key strategy for many shippers during the pandemic as they tried to keep goods moving via ocean in the height of congestion. Fast forward to post-pandemic, it remained at the top of the shipping playbook as shippers looked to move smaller volumes to address overcrowded warehouses and cost reduction pressures.
As retail peak season approaches, which historically can start as early as August, shippers should look to LCL to support their supply chain strategy as it provides an additional layer of flexibility if they need to quickly pivot. In C.H. Robinson’s 2023 shipper survey, almost two-thirds said they plan to utilize or grow their LCL shipments in 2023 and over half are looking to shipment consolidation to drive freight efficiency. As demand and transit time changes, LCL can help keep goods moving in a cost-effective way.
Shipping strategies must change as supply chains do.
As varying global factors cause manufacturers to re-evaluate their supply chain activities, many are looking to mitigate risks through supplier selection and nearshoring or friend-shoring. As manufacturing centers or suppliers change location, shipping strategies need to be reconsidered. Not all markets are created equal and shipping strategies that worked in one may not work in the other. Considering different shipping options when moving operations is critical to ensure a seamless transition. Working with a supply chain partner can help evaluate the effectiveness of alternative supplier or factory locations because avoiding risks from one location may lead to new risks at another.
Optimizing across modes will bring cost savings.
Shippers went way over budget during the pandemic in the name of compromise. Now that shippers are prioritizing cost savings, leveraging various modes can help optimize spend. Depending on the freight, shippers could select ocean ports based on the location of their distribution centers but use intermodal rail or truck interchangeably based on cost. Another strategy is consolidating freight at its origin and using only one port with the best rate. Looking at strategies like these can bring significant savings, but it requires advanced visibility to effectively plan. Looking to digital tracking tools to ensure they always have the most accurate data to inform an adaptive strategy is key.
After the last few years of supply chain shifts, it’s no surprise that the 2023 contract season is unusual. While many may think the dust has started to settle from contract season, peak season is right around the corner, which could lead to an increase in demand and shippers should keep these trends top of mind as new challenges enter the market.