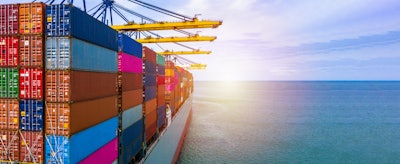
U.S. ports made headlines this year as an unprecedented volume of incoming ocean vessels stalled along the East and West coasts creating severe delays. This caused major delays for importers and shippers with already disrupted supply chains, but the last few years have not been easy for exports either.
Moving cargo abroad has been challenging for quite some time due to varying reasons. Whether its vessel capacity, changing receiving windows at ports or drayage congestion due to limited rail and chassis availability, the challenges have been evolving but constant.
What’s behind the disruption
Shippers know that the export market can be volatile. Just a few years ago, the U.S. export market was competing for vessel space as ocean carriers were prioritizing bringing empty containers back to Asia to meet the demands of their booming export growth. As carriers returned empty containers back to Asia instead of U.S. exports, global capacity also tightened as they diverted ships from other markets to meet the growing demands.
Fast forward to 2022 and ocean capacity has begun to open again, but the challenges for exporters remain.
U.S. East and Gulf coast port congestion continues to make planning difficult for shippers. As vessels are left waiting for berths, their expected sailing dates shift and the earliest receiving dates (ERD), which shipments are planned around, are shifting with them. This had made planning incredibly difficult. ERD delays can lead to increased costs, for example, container pull and yard storage charges, daily chassis rental costs, and detention fees. While detention fees can sometimes be waived depending on when the ERD changes, most fees will not be.
Rail service disruptions have also impacted export schedule reliability. There is a shortage of containers moving from ports to inland rail yards, which in turn creates a shortage of empty containers at inland points. This combined with the ongoing chassis shortage has reduced inbound rail activity, which in turn limits outbound rail volume as most rail carriers are looking to book round trip moves.
What can exporters do?
The good news is there are options for adapting export strategies to address these challenges, while still meeting existing delivery and budgetary expectations. Considering factors like location, budget and distribution capabilities will ensure you are picking the option that’s right for you.
Inventory transfer: Reducing your reliance on rail can help you better control shifting ERD timelines and manage the availability of empty equipment. If your distribution system is substantially domestic, take advantage by relocating cargo to warehouses that are closer to your port. This allows you to load containers at those locations and dray directly to the port, where there is normally an influx of empty containers.
Truck and transload: While I wouldn’t recommend this strategy as a first choice, this is an option if you can’t move cargo closer to the port. Truck and transload service can be expensive as warehouses are filled and the risk for potential damage to cargo increases as it requires rehandling between different modes.
Truck to port: Markets that are within a day’s drive to a port (such as Dallas, Atlanta or even Cleveland) allow for long-haul drayage as an option to move cargo to the port without relying on rail. While it can be costly compared to a rail-truck solution, some shippers are willing to pay for a truck-to-port solution as it can save them some of the disruption that comes with today’s rail landscape.
Additionally, some players in the logistics industry are realizing that third-party chassis ownership is contributing to the chassis shortage. In response, they’re building a network of truckers who own chassis. There are not enough truckers making this chassis investment to meet the need currently but using such a network can help to bring stability to your truck-to-port solution.
Alternate rail ramps: If draying directly to a port is not an option, you can always shift to another rail ramp.
Rail ramps across the Midwest have an assortment of issues right now – not unlike other modes – such as chassis shortages, insufficient empty containers and reduced outbound rail traffic.
This strategy can raise trucking costs depending on the distance to the ideal rail ramp. Before assessing alternate rail ramps, you should determine whether you prefer a higher shipping cost or risk of delay from a strained rail ramp.
Plan and forecast
As we’ve learned in 2022, we cannot plan for disruption going away. While chassis shortages and port congestion may ease in 2023, it’s hard to predict what other factors could impact capacity and delays. To get ahead, either way, you should forecast and plan shipments three to four weeks out. This, in combination with the best export strategy for your budget and objectives, will help you keep cargo moving until we see relief in the export market.