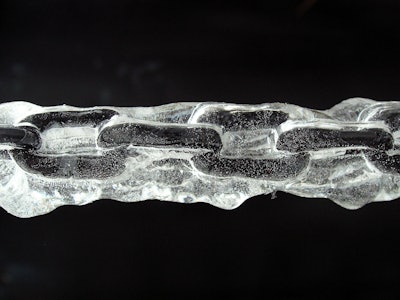
This summer, many people across the country were impacted by the intense heat.
And for certain cold supply chains – which encompass the manufacturing, storage and distribution of temperature-controlled products – extreme weather can be cause for great concern. Specifically in the pharmaceutical industry, transporting medications that require cold chain capabilities is a logistical challenge on its own, but the addition of extreme temperatures presents new obstacles that can make the process even more difficult to manage.
Cold supply chains are necessary to ensure the efficacy of certain medications, vaccines and other biopharmaceutical products. Most recently, the pandemic brought heightened awareness to this cold chain process with the COVID-19 vaccine rollout, which required the storage and transportation of millions of vaccines in extremely cold temperatures. During this time, everyone experienced firsthand the importance of cold supply chains and the various challenges facing its key players.
Cold Chain Complications
Major shifts in weather can cause significant challenges for the cold supply chain, with spikes in either direction often creating a heightened sense of uncertainty and even anxiety. This is especially true in the specialty pharmaceutical industry, as patients are awaiting the arrival of potentially life-sustaining and life-saving drugs. These therapies must be delivered to the right place, at the right time and in the right condition– all of which is dependent on cold supply chains working as intended.
It’s important to note that cold supply chains don’t just keep medications cool. Most therapies that require a cold supply chain must stay within an optimal and narrow temperature range to avoid spoilage. This complex requirement can have far-reaching impacts if not properly adhered to, including loss of time, money and resources. Additionally, any deviation from the parameters may cause the medication to spoil, which could lead to dire circumstances for patients on the receiving end.
With this, the primary concern with pharmaceutical cold chains is almost always delays. Even the smallest hiccup can affect the efficacy of the products being transported, leaving room for significant error if each step is not executed properly. Every cog in the wheel plays an important role in the transportation and arrival of specialty drugs, including refrigerated trucks and planes. So, if a truck or plane is delayed due to extreme weather conditions, the entire chain of events is disrupted, impacting providers, patients and others.
Specifically in the summer months, there are additional obstacles that emerge when the outside temperature surpasses 100 degrees Fahrenheit. Refrigerated container condensers must work harder to regulate the desired temperature, which can result in complications in the form of threshold alerts and failures, more maintenance, increased costs and delays.
Avoiding Disruptions
It’s imperative for pharmaceutical manufacturers and distributors to always look a few steps ahead. To avoid the need for reactive or impulsive decision-making, proactive inventory management and ordering are critical. For distributors, this proactivity can be achieved by working closely with your partners and customers to anticipate what they will need tomorrow– and ordering for it today.
Smooth cold chain operations have strong standard operating procedures and team training materials in place year-round, allowing for ample planning time and strategizing before extreme weather hits.
In anticipation of a heat wave, it is critical to ensure that refrigerated gel packs and other materials are qualified to withstand high temperatures for 48 hours. This allows for enough time to quickly move products to backup storage options and refrigeration spaces if, for instance, there is a power outage or brown out. On the other hand, in anticipation of an ice storm, it’s important to consider the possibility of certain roads or even entire transportation companies shutting down and having an alternative plan ready.
With these complications, it’s important for pharmaceutical manufacturers and distributors to keep in mind that there is always a patient in need on the receiving end of any medication. This reality can guide us as we make tough decisions to ensure that therapies arrive safely to patients, no matter the conditions.
Looking Ahead to Future Advancements
In the future, there will be improvements in packaging, storage management, warehouse automation and more. Technology-driven automation will become increasingly important to driving efficiency, accuracy and speed within cold chain distribution. One key example is robotics assisting with inventory management to improve accuracy in moving products from a warehouse to the shipping zone.
Additionally, the internet of things (IoT) will continue to play a role in the live measurement and monitoring of shipments. This critical technology alerts manufacturers and distributors of a shipment that is starting to reach the boundaries of its optimal temperature range, allowing them to act quickly to avoid spoilage.
In terms of cold chain packaging, we will likely see groundbreaking innovations in green initiatives, which have long been a challenge in distribution. These developments will not only be great for the cold supply chain, but they will also be beneficial for the environment.
We have no doubt that these technologies and areas of focus will allow the pharmaceutical supply chain to further perfect the ability to transport temperature-sensitive medications quickly and efficiently, especially in extreme weather conditions, providing patients with the care they need.