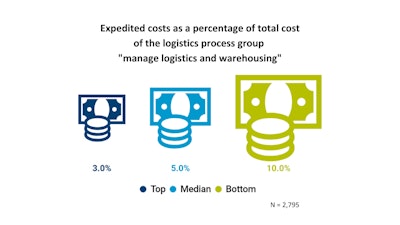
Unexpected spikes in demand may require an organization to expedite orders to meet customer needs. While the causes of expedited orders are sometimes beyond an organization’s control—for example, when a supplier’s truck breaks down—there are meaningful interventions that any organization can make in order to minimize costs related to expediting orders. In this article, we break down what organizations spend on expediting orders and focus on strategies that can help keep expedited logistics costs under control.
Logistics data from APQC’s Open Standards Benchmarking database, illustrated in Figure 1, shows that there is a considerable gap between top and bottom performers when it comes to expediting: While top performers spend 3 percent of the total cost of logistics on expedited costs, bottom performers spend more than three times that amount at 10 percent.
Bottom performers could potentially achieve significant savings by improving their performance on this metric. For example, an organization with $2 billion in annual revenue that spends 2.4 percent of its revenue on managing logistics and warehousing (the median process cost for all companies, per APQC’s Open Standards Benchmarking data) could save $2.4 million dollars on expedited costs by moving from the bottom performer level to the median level. Making improvements to reach top performer status would mean the organization could save $3.4 million on expedited costs per year.
Taking Action
For organizations that want to improve their performance on this metric, understanding the most common causes of expedited orders—along with effective mitigation strategies for each—is a good first step. Figure 2 shows the top five most common causes of expedited orders in APQC's Open Standards Benchmarking data (for bottom performers). The cause of almost half of all expedited orders (49 percent) is inaccurate demand forecasts, followed by raw material shortages. Rounding out the top five is a three-way tie: poor transportation planning, production schedule changes, and unavailable transport equipment.
Strengthen Demand Forecasting
Broadly speaking, expedited orders result from failures that occur in supply chain planning. If an organization’s demand forecast is full of bias or based on poor-quality data, it could fail to order the right amount of material to meet demand.
Sound data management practices and collaboration are critical to meeting the challenge of inaccurate demand forecasts. APQC recommends auditing your data management processes and working to align your organization’s internal functions on how demand data will be aggregated. APQC has also found that increased collaboration among functions (and with customers and suppliers) in sales and operations planning or integrated business planning leads to more reliable forecast inputs. These, in turn, lead to greater forecast accuracy, which can result in fewer expedited orders.
Understand Your Supplier Relationships
An organization confronting a raw material shortage—the second most common cause for expediting—should work to determine the cause of the shortage. If it’s coming from the supplier, understanding the nature of the relationship and working with the right sourcing business model based on that relationship is the key to finding an effective mitigation strategy. For instance, if the supplier is a basic provider (and thus a transactional relationship), averting a raw material shortage would simply be a matter of ensuring the organization can leverage alternate suppliers. For more strategic supplier relationships, on the other hand, the buyer and supplier should collaborate together on a cost management plan and jointly develop a formal risk analysis, management, and mitigation plan with defined tracking and measurement processes. Close collaboration in strategic buyer-supplier relationships helps to reduce the worst impacts of raw material shortages and minimize expediting.
Work to Improve Your Procurement Process
Process thinking promotes standardization and efficiency in all areas of the business, including procurement. If the cause of a raw material shortage is not your supplier, you may want to look more closely at your organization’s procurement process. If you have not done so already, you should begin by defining, documenting, and assessing your processes with a standard process framework. Process frameworks like APQC’s Process Classification Framework (PCF) provide a common language for processes and allow for greater visibility into how work gets done. Mapping your as-is procurement process within a process framework will help your organization pinpoint and prioritize opportunities for improvement.
Along with process mapping and documentation, APQC recommends that organizations track and benchmark performance on a balanced set of KPIs, including cost effectiveness, cycle times, efficiency, and productivity. Doing so can clarify how the organization’s performance compares to others and also reveal where more (or less) resource allocation would be wise in order to bring down costs overall.
Centralize and Digitize Transportation Planning
Poor transportation planning is another common cause of expediting orders. The good news is that many organizations have been able to improve their planning and logistics with centralized transportation planning. A centralized structure enables organizations to more effectively track products, bring down transportation costs, and manage carriers so that the organization can have full visibility into transport, standardize priorities and processes, and negotiate the best rates. Along with centralizing transportation planning processes, organizations have achieved stronger logistics with lower costs and shorter cycle times by leveraging a transportation management system (TMS). Typically sitting between an ERP system and an order management or warehouse management system, this software helps organizations manage inventory flow, vendor relationships and preferred shipper status, and customer expectations. These practices and tools lead to more efficient and effective logistics processes that can lower the likelihood of expedited orders.
Conclusion
Expediting isn’t always avoidable, but organizations can reduce and mitigate the costs associated with expediting orders by making improvements to demand forecasting processes, working collaboratively with suppliers, and looking for opportunities to improve the procurement process itself. Bottom performers could potentially save significant amounts of money if they can reduce their expedited costs, but even top performers can achieve greater process efficiency and stronger supplier relationships by working to bring these costs down.