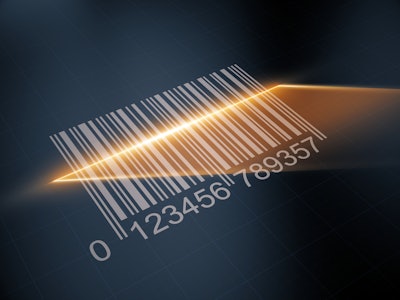
When it comes to your barcode labeling software solution, implementing lean labeling and continuous improvement principles to your labeling environment reduces waste in label printing and saves you money. Lean Labeling and sustainability go hand in hand by eliminating waste in your labeling processes. This helps create a more sustainable barcode labeling environment while reducing resource use. By following the lean labeling process, companies can trim their barcode labeling process down to use only the time, materials and energy that are truly required.
What is Lean Labeling?
Lean Labeling can be defined as, “A method to minimize waste within a label printing system without sacrificing productivity.”
If your current labeling environment looks like a scattered mess, you’re not alone. 100% of respondents from a TEKLYNX poll said their labeling environment was not completely lean; while 43% of respondents said they needed to make significant improvements to have a lean labeling environment.
Here are five basic steps to apply lean labeling and continuous improvement principles to your labeling environment to eliminate label printing waste.
Step 1: Identify waste
Waste takes on many forms in label printing, such as misprinted label stock or workforce waste when staff must manage thousands of label files. Waste typically comes from three areas in a business' label printing environment:
- Maintenance: Maintenance waste includes the salaries of your IT staff while they spend time installing your label software licenses on individual workstations. In addition, this includes time users spend searching for the desired label template out of potentially thousands of files.
- Process: Process waste occurs when steps could be automated but are currently carried out manually with human interaction. Not only do humans take longer to enter data and print labels, but they are highly prone to making errors - Yes, surprisingly humans make mistakes!
- Inaccurate Labels: Waste from inaccurate labels could be as small as a few wasted labels, or as massive as hundreds of thousands of dollars spent on a product recall.
Step 2: Analyze the root cause
Once waste in the label printing process has been identified, it’s time to take a closer look at why it’s occurring. You’ll want to ask yourself these seven questions:
- Are the barcode labels created and stored haphazardly?
Many companies start with a small directory of labels, but that quickly becomes unmanageable as the number of different labels grows.
- How do you make an update that affects all your labels?
Changes like a new company logo or change of address could take hours to implement on hundreds of label files.
- Is your barcode label software licensed on a single-user basis?
Software maintenance costs balloon when licenses are not centrally managed via a network. Check out our licensing options to see what will fit with your lean labeling environment.
- How was the error made? Does the user need freedom to decide in this step?
If the user is entering data that is available in another system, or if they’re entering a calculable value (i.e., an expiration date), this step can be automated.
- Where does the correct data reside in your business system?
Often, your business system already houses the data that is required on your labels.
- What needs to happen to the data when it is added to the label?
Can the expiration date be determined by adding a set amount of time to the manufacture date? Should the quantity be determined by the order number? Can these decisions be made by the system instead of the user?
- How many steps are in the label printing process, and how long does each step take?
If the user must search through many folders every time, they want to open a label or they must manually enter data, those steps add time to the label printing processes. Remember, printing labels isn’t your user’s primary job. Every time they must print labels, it means they are stopping their primary responsibilities.
Step 3: Solve the root cause
Solving the root cause of labeling printing waste doesn't have to be difficult.
If the waste was due to maintenance, consider:
- Network licensing
- Smart label templates with database connections
- Label storage software
If the waste was due to process, consider:
- Print-only licenses
- Label approval software
- Print automation software
If the waste was due to inaccurate labels, consider:
- Smart label templates with formulas
- Database integration
- Enterprise label management software
Step 4: Measure results
Key Performance Indicators (KPIs) are excellent tools to show the results of a lean labeling initiative. KPIs provide concrete numbers that you can use to determine if your project was successful or not. Simply calculate these KPIs and share them with your boss to prove the value and ROI of your project. Below are some example KPI targets:
- 90% or more print jobs that use a label template
- 5 or fewer standalone workstations with barcode label design software connected directly to a printer
- 3 or fewer input fields required to be manually updated by the print user
- 100% utilization of input masks that require a specific format for field inputs
- 100% utilization of warning messages
- 5 seconds or less required for the print user to launch a print job
- 1 second or less required for the system to process a label and start to print job
Step 5: Repeat!
Move on to the next source of label printing waste and repeat the lean labeling process to save time and money.
The goal of lean labeling is to minimize waste within your labeling environment. Less waste means greater productivity and ultimately a more profitable business. Labeling experts and barcode labeling providers can help you identify waste, and the root cause and come up with a solution to streamline your labeling.
* KPIs and target values developed by Dave Klement, Principal at Efficient Business Integrators.