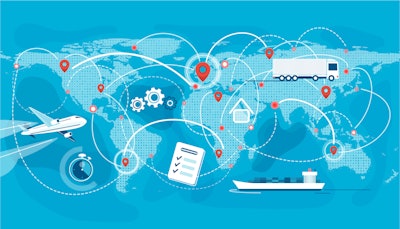
Decarbonizing the supply chain is a critical component of achieving Net Zero CO2 reduction goals. More than 90% of the typical organization’s greenhouse gas emissions come from supply chains, which means that supply chain decarbonization is also a potential area for big wins in the short term and over the longer horizon. Up to 95% of companies say they’ll be impacted by the need to reduce their supply chain’s carbon footprint, but many aren’t ready to do so while maintaining or improving their customer experience (CX).
Solving for sustainability and CX in the supply chain is a must, because in addition to the hard limits imposed by our atmosphere, customers also increasingly expect sustainable products. Investors are weighing in, too. Nearly a quarter (23%) of global companies surveyed by the MIT Center for Transportation & Logistics in 2022 said they feel an “increase in pressure from investors” to make their supply chains more sustainable.
These combined requirements and expectations require businesses to find ways to reduce their supply chains’ carbon footprint without causing a decline in product quality, service delivery and other elements of the customer experience. A strategy that uses data analytics, hardware improvements and process optimization can meet carbon reduction goals in a way that meets all stakeholders’ standards.
Setting Supply Chain Sustainability Goals
A 2022 MIT survey found that climate change mitigation was the most often-cited focus of corporations’ supply chain sustainability (SCS) goals, followed closely by natural resource and biodiversity conservation and supply chain circularity. Of course, each organization has unique supply chain requirements and investor and customer expectations, so every organization needs to plan its own strategy for improving SCS.
A good starting point is to audit and map or diagram your current supply chain so that you have a view of all suppliers. MIT found that 46% of organizations audit suppliers and 38% map their supply chains as part of their SCS practices. Without this information it’s impossible to quantify your current SC carbon footprint, so it’s worth investing as much time and effort as it takes to get the most comprehensive and up-to-date visibility you can, even if you can’t get a complete 360-degree view. Another survey found that “very few” B2B organizations are currently able to implement “end-to-end transparency and visibility.”
When you’ve clarified your supply chain to the best of your current ability, it’s time to quantify your current greenhouse gas emissions and other environmental impacts based on data from each supplier as well as the costs and emissions impact of transport for raw materials, components, suppliers and finished goods. You’ll also need a clear understanding of what sustainability improvements matter most to your customers. Are they most concerned about CO2 emissions reduction, the use of recyclable materials and packaging, circular product life cycles or something else?
Identifying Carbon Footprint Reduction Opportunities
While it’s important to center customer preferences at this stage, it’s also wise to focus on changes that can have the largest impact, rather than simply adopting practices that are trendy. For example, recyclable packaging is popular with consumers and should be implemented wherever possible. But if a company’s products are more resource-intensive than they need to be, fixing the packaging should come after more impactful changes to maximize impact reduction
Take a look at hardware across your supply chain. Can you automate any of your supply chain processes for better efficiency and less resource consumption? Are there processes where robotics could increase operational efficiency or reduce production waste? Do your suppliers and transporters (and your own plants) use smart equipment or equipment retrofitted with temperature and vibration sensors for data analytics and predictive maintenance programs that can reduce unplanned downtime and optimize resource use?
You can also analyze your products to understand what you can change to improve your carbon footprint without impacting CX. Those changes might require changes in your supply chain. For example, can you move to sustainably sourced or recycled materials without compromising the quality of your product or pushing the overall cost too high for your customers? Can you implement an end-of-life product management program that accepts and recycles or refurbishes your products?
Are there components that can be standardized across your products? One industrial tools and consumer hardware maker is undertaking a standardization program “to create economies of scale with key suppliers.” This approach can simplify the supply chain, reduce transportation and manufacturing resources required and create efficiency gains and cost savings while also making it easier to bring new products to market faster.
As you identify possible supply chain improvements, it’s wise to analyze each potential change in terms of its requirements and impact across several dimensions, including process and product quality, customer experience, supplier availability and ROI. For example, if you’re considering adding recycled materials to the manufacturing process, carefully consider the material science requirements you’ll need to make sure the materials you’re considering are right for the finished product in terms of durability and quality. Also consider the impact of the process of working with those materials–will their inclusion be a net positive or will it increase carbon emissions? Finally, understand how many times those materials can be recycled so you can quantify the long-term potential impact of using them, especially if you also plan to implement a circularity program.
Supplier availability can be another factor to weigh. For example, the closer that sustainable raw materials are to your processing or manufacturing plants, the greater the overall benefit of switching to them. On the other hand, if sourcing sustainable materials will require more resource-intensive transportation, you’ll need to identify the cutoff point at which obtaining those materials becomes a net negative in sustainability terms.
A Greener Supply Chain That Meets Or Exceeds CX Expectations
Once you implement a supply chain change like automation, predictive hardware maintenance, working with recycled materials or standardizing components, communicate with your customers about the changes you’re making and why. Then carefully monitor your customer feedback along with operational and emissions data. The information you gather on each improvement will help you determine which changes have the biggest net-positive impact. That information can serve as a map for ongoing sustainability improvements across your supply chain, so you can keep reducing your environmental impact and meeting customers’ expectations.