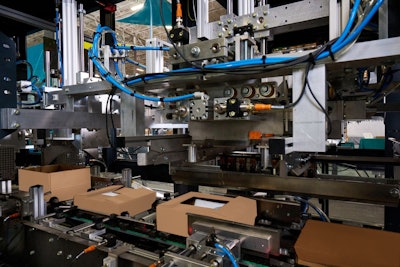
As fulfillment businesses eye profitability, the factors that influence their success look different from a few years ago. The market downturn continues to impact future forecasts. More customers expect faster shipping, for free, which increases the burden on businesses. Employees aren’t quite as hard to find, but retention remains an issue.
To stay competitive and profitable, reliability and consistency are more important than ever. To stand up to these challenges, forward-thinking fulfillment centers are tapping into new automation strategies. They’re designing automation not only around traditional factors like efficiency, speed and the bottom line, but also where they drive a positive ROI (return on investment) that keeps them competitive long into the future.
Three Competitive Advantages of Scalable Automation
To make the most of automation, it must be scalable or capable of being easily adapted based on changing needs. In some cases, automation’s ROI may be measured by daily pack station performance. In others, it may be measured by the total cost of a machine over its lifetime, including repairs and service.
In general, there are three areas where scalable automation can contribute to ROI and lead to a competitive edge in today’s fulfillment landscape: accelerating speed to ship, improving labor efficiency, and supporting long-term business goals. Here is a closer look at how each area can help businesses create future-ready fulfillment.
Competitive Advantage #1: Accelerating Speed to Ship with Scalable Automation
Speed to ship is one of the key metrics in any fulfillment center, whether you’re shipping an e-commerce order for a T-shirt or a pallet of hardware to a home improvement store. It’s an important metric to stay competitive amid market shifts.
Automation can help you build the most efficient way to get from pick to pack to ship. Consistency and throughput are two critical areas where scalable automation typically delivers results, regardless of application. Companies who opt for automation often improve consistency of their packs and processes.
For example, automated bagging systems eliminate the need for employees to manually pull mailers and guess which size is best for certain products. Similarly, material insertion systems paired with automated box rightsizing systems take the guesswork out of how much cushioning or void fill to use, which helps avoid over- or underpackaging. This supports cube optimization, reduces dimensional (DIM) weight, and helps prevent product damage, which are all essential for controlling e-commerce fulfillment costs.
Improved throughput is another area where companies see benefits at all levels of automation, from entry-level to fully integrated. When scaled the right way, with a focus on your process and needs, automation allows you to do more in less time. And that can positively impact how quickly products get out the door.
We also can’t ignore the growing interest in digital capabilities to power better consistency and throughput. Companies are looking for new ways to use the data that powers automation to deliver actionable business insights. For example, data can be stored and then downloaded directly from machines to review or be connected to centralized dashboards for real-time views of performance.
In some fulfillment centers, we’re seeing data from automated box rightsizing systems seamlessly shared for monitoring and process control. This connection gives companies a detailed and up-to-the-minute view of what’s happening on a line. The collected and stored data can be analyzed to see trends over time, including variations in throughput and consistency that can affect speed to ship.
The options for connected data will only continue to grow and reshape the way we do things. While right now this is in the early stages of adoption—primarily with large, complex fulfillment operations—this type of connectivity is going to be critical in fulfillment centers of the future.
Competitive Advantage #2: Improving Labor Efficiency and Worker Satisfaction
While some of the labor crunch from the past few years has eased, there are still struggles to recruit and retain labor in fulfillment centers. Automation can help you make the most of the labor available to you in a few ways.
One way is a shift from physical labor to managing a process. Team members can work on higher-level tasks, such as managing machine throughput, and let automation take on more tedious manual processes, such as printing and applying labels or inserting void fill and cushioning materials. These examples can lead to better satisfaction at work, which in turn can improve retention.
Another benefit is improving the use of temporary labor during peak season. Automation can make tasks less complex, which can make it easier to train new employees.
One example is a packing station with an automated bagging system. Traditionally, an employee would need to look at the product then manually pick a bag size and print and apply a shipping label. Instead, a semiautomated bagging process feeds and opens bags automatically, applies the label, then seals the bag, so an employee simply scans an order, hits a button to start a cycle and the rest is done.
Competitive Advantage #3: Delivering Results Today While Improving Operations for the Future
When scaled appropriately, automation can positively impact your company’s ability to improve its operational efficiency and sustainability for long-term results. Even better, changes made today can also deliver immediate benefits.
Efficiency Impact
Any level of automation can improve efficiency, from entry-level, semiautomated bagging machines to fully automated box rightsizing systems. One of the ways this happens is through digital capabilities that improve consistency and reduce manual effort.
In industrial applications, one of the common entry points to automation is a semiautomated bagging system for kitting components, such as screws or hardware.
Manually, it might be possible to bag, label, and seal one or two bags per minute. But with the help of a semiautomated machine—and preprogrammed buttons that store data for easy recall—a single operator could increase throughput to 10-12 bags per minute, achieving a full day’s throughput in only a few hours. This efficiency boost allows those extra hours to be used for other tasks.
In e-commerce applications, automated box rightsizing systems continue to improve efficiency and throughput. In addition to automatically scanning and rightsizing cartons to the products inside, these systems use in-line and print-on-demand labeling. Shipping information is fed directly to the equipment for labeling, removing a separate labeling step from the fulfillment process.
Regardless of your level of automation, having a process to manage spare parts and a strong service partner is another essential piece to ensure efficiency and minimize downtime. Being proactive and prepared can avoid disruptions and maintain reliability.
Sustainability Impact
Looking at the full life cycle of packaging, automation touches on nearly every aspect of sustainability: better energy use, better or lower material use, and better use of shipping space to reduce your carbon footprint.
- Better energy use: Machines can be programmed to increase or decrease utilization to optimize energy use.
- Better or lower material use: Automated processes like box rightsizing help you use less packaging material by reducing void fill, while on-pack printing eliminates additional materials like printed labels.
- Better use of shipping space: Optimizing inbound and outbound shipping space can help lower your carbon footprint. Automating fulfillment with bags and rightsized boxes can reduce DIM weight while also improving packing efficiency.
The packaging industry is also evolving automated technology to use more curbside-recyclable materials when they can deliver similar performance. One example is a high-speed bagging and printing system that runs paper mailers ideal for apparel and soft goods, which are easier for consumers to recycle at home.
Adopt Scalable Automation for Long-Term Success
By defining what the ROI of automation looks like to you, it’s possible to pinpoint where automation makes sense and where it doesn’t so you can make a smart investment for the future.
Companies who take a proactive approach to scalable automation can equip themselves for what the future holds. With reliable equipment, materials and service, and the right packaging supplier, it’s possible to build a future-ready process that delivers consistent results with benefits that pass through to your customers.