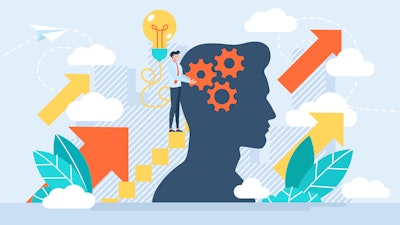
The pipeline of supply chain and procurement talent may not be broken, but it’s certainly leaking.
The emphasis on digital transformation and rapid adoption of artificial intelligence across industries has, in many cases, moved faster than the existing workforce could keep up. Compounding the issue, too few young, technologically savvy young professionals are joining the supply chain and procurement field to drive these initiatives forward.
The solution, then, lies in upskilling or reskilling current employees to create new efficiencies, reduce costs, and mitigate risk for supply chain and procurement organizations. While this does involve becoming familiar with AI and other cutting-edge technologies, old-school relationship building is still a crucial piece of our industry.
In order to upskill or reskill employees, organizations should consider developing training programs around three key pillars — digital skills, soft skills and technical skills.
Digital Skills
As a first step in an upskilling initiative, supply chain and procurement organizations should analyze the use and adoption of each technology in their current tech stack to determine whether and how employees can more effectively leverage them — for example, using additional modules within already-licensed software instead of purchasing a new one. If any existing technologies are underutilized, this exercise will help uncover the root cause.
To help identify which existing technologies might be a good fit for stronger adoption across the team, look for platforms that:
- Have a user-friendly interface,
- Require lower engagement with the IT team for use,
- Integrate seamlessly with other tools in your tech stack,
- Provide analytics and reporting capabilities,
- Have automated workflow capabilities, and
- Include robust customer support from the technology provider.
Engage employees in this technology evaluation to start their upskilling early. By seeking and incorporating their feedback in the process of selecting which tools in the tech stack will be prioritized, organizations can help their teams feel a real sense of ownership in their training. Starting with a thorough assessment of those tools will also prevent employees from being trained on a technology that might soon be outdated or eliminated from the tech stack altogether.
After completing the technology assessment, companies should perform a skill-gap analysis of their workforce to determine what training is needed to improve productivity using their specified technologies. Incentivize employees for completing trainings and for utilizing the technology during the early phases, and take the time to develop internal SMEs that can coach other team members.
To avoid becoming overwhelmed by the volume of upskilling that you think might be needed, consider role-based training. Not every employee needs to be trained on every technology nor every function of a particular technology. Focus on training that is needed for a particular employee to perform their day-to-day tasks with lower efforts.
However, training employees on digital tools alone won’t suffice. The ability to take real-world action from the information surfaced by technology is a critical advantage for today’s supply chain and procurement professionals.
Soft Skills
Supply chain and procurement technologies can tell us what’s happening with materials and parts out in the global supply chain, but it takes effective communication and stakeholder relationship management to actually do something about those data points. Outside of technology, a robust supplier relationship management (SRM) program is one of the most critical steps an organization can take to future-proof itself in this rapidly changing market.
During the pandemic, companies that had a strong SRM program faced the fewest procurement challenges. Because they had built trust over long-term relationships, they were often able to secure the materials and components they needed from key suppliers. This led to more organizations emphasizing a focus on developing supplier relationships to mitigate the risk of future disruptions.
Organizations must also ensure their supply chain and procurement workforce is skilled at building relationships with their internal stakeholders. The role of supply chain and procurement has changed drastically in the past five years. This function now has a seat at the table, if not the C-suite.
Supply chain and procurement is now a strategic partner to departments across the organization, not just a buying center. They are no longer expected just to reduce costs but also to secure supply and drive innovation in business-critical areas like sustainability and ESG compliance.
To meet this responsibility and truly prepare for the future — where the global supply chain only becomes more disrupted — organizations must think outside the box when it comes to the skills needed to work in supply chain and procurement.
Technical Skills
As the demands placed on supply chain and procurement organizations have shifted, so too has the “typical” job description for a supply chain or procurement professional.
Roles like strategic relationship managers, risk management advisors, sustainability officers, digital transformation leaders, change management leaders, project managers, and even data scientists are being introduced within these organizations to drive compliance, risk mitigation, sustainability, and organizational transformation. This opens a lane for individuals who may never have considered supply chain and procurement as a career path, and it creates opportunities for current professionals to learn new skills that might be considered non-traditional in the field.
For example, a basic understanding of data and analytics is critical for enabling faster, fact-based decision-making. A strong grasp of data analysis will also support employees’ understanding of AI and machine learning — probably the most important skillset a supply chain and procurement professional could have today.
Be transparent with your workforce about which AI technologies are available to them and how the tools can improve their productivity. Then, provide training to support use of the tools. This will help reduce employees’ hesitation around AI and improve individual adoption.
Additionally, supply chain and procurement employees can be upskilled to support the function’s growing scope and goals in areas like cybersecurity, measuring sustainability metrics and basic finance, such as cost analysis, budgeting, and forecasting. While most members of the supply chain and procurement team will not focus on these areas as a main function of their role, this shared knowledge and effort across the broader team can help the organization meet its larger goals more efficiently.
What Companies Can Do to Upskill their Supply Chain and Procurement Workforce
As the global supply chain evolves, organizations must ensure their workforce is evolving alongside it. Training and skill gap analyses should be ongoing efforts to meet changing needs, with training part of general employee onboarding and targeted to address specific skill gaps. Other ways to help employees retrain or learn new skills include:
- Providing access to online learning platforms for relevant courses and certifications,
- Organizing in-house workshops and seminars led by industry experts,
- Establishing mentorship and on-the-job training programs to facilitate hands-on learning,
- Leveraging flexible e-learning platforms and simulation tools for realistic practice scenarios,
- Collaborating with universities for advanced courses and executive education, and
- Making training hours a mandatory part of teams’ key results areas.
An external partner that specializes in supply chain and procurement can assist with strategic assessments of an organization’s existing technology and workforce, collaborating with internal stakeholders to develop robust strategies for their digital transformation and training that align with business goals. These partners can provide industry benchmarks, best practices, as well as specialized recommendations or even management of specific processes until in-house employees are fully trained.
Supply chain and procurement organizations — and their employees — are understandably feeling challenged on all sides. Technology is changing on a weekly, or even daily, basis, while disruptions are occurring almost as quickly. However, by focusing on the tools you already have at your disposal, doubling down on relationships and encouraging supply chain and procurement team members to grow their skills in new areas, companies can become more prepared for whatever lies ahead.