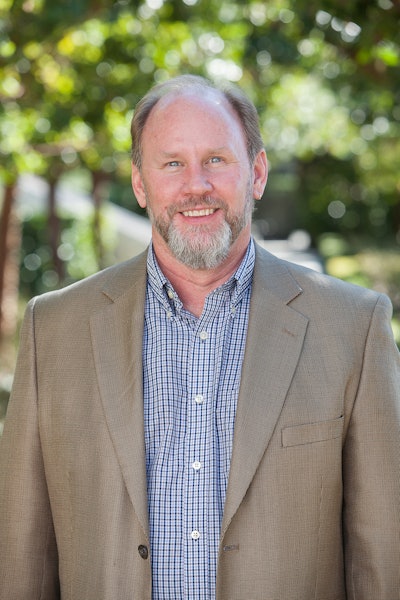
3D printing has played a significant role in transforming the supply chain over the past decade. Its recent sparkle in the public eye is but a glint compared to the effect the technology has behind the scenes on the production floor. It is impacting every stage of the product development lifecycle, from the product itself to packaging, presentation, delivery—you name it. In all the hype, it can be difficult to extract the substantial benefits of the technology from the dreamy, more futuristic tales. The real differences 3D printing is bringing to the supply chain lie within five key areas.
1.) Vetting Out Designs
Instead of taking a 2D design straight to a tooling/molding manufacturer, designers and engineers use 3D printing to prototype and vet out designs. This function was 3D printing’s earliest benefit and was its first purpose starting out in the late 1980s, but it is no less relevant today. More recent materials developments in 3D printing are creating prototypes that not only mimic the look and feel of injection molded thermoplastics, but can even mirror properties for functional testing. From three decades ago to today, 3D printing no longer just reveals designs—it reveals products prior to end production.
Locating design flaws, which would normally only surface once tooling investments were made, and re-prototyping and redesigning more frequently and affordably is leading to more optimum products across aerospace, medical and consumer product industries. Fixing a design flaw doesn’t mean shipping a tool back and forth, or buying and waiting on a new tool; users can simply update the 3D computer-aided design (CAD) file, reprint the design and validate it before ever moving into tooling. 3D printing is helping shorten the supply chain by speeding up product development cycles as well.
2.) Manufacturing Aids
Manufacturing aids, such as jigs, fixtures and other tools that speed up assembly lines, are valuable but can be time-consuming and/or expensive to traditionally develop. The versatility of additive manufacturing and the ease with which it develops durable, accurate parts makes it a go-to resource for assembly lines today. Manufacturing aids, such as custom tube bender dies, jigs and fixtures, cooling patterns, molds, locating templates, and drill and saw guides became perhaps some of the best-kept 3D printing secrets. Using 3D printing manufacturing aids ensures a high level of observable quality management, and helps maintain efficiency and profit.
3.) Packaging
3D printing materials now mirror those used in taxing heat and pressure environments, including high-performance thermoplastics such as polycarbonate and ABS. These materials, coupled with 3D printing, are being used to create custom thermoforming patterns. Custom thermoforming patterns benefit from 3D printing in three ways as the technology can achieve: designs which fluctuate in thickness; patterns with varying sizes; and patterns requiring multiple unique shapes. Packaging industries are finding 3D-printed thermoforming patterns an increasingly more economical and effective solution to challenging product designs.
4.) Production
We can’t stress this enough: Materials developments are changing the face of 3D printing. Thanks to these developments, it’s becoming progressively more common during certain manufacturing processes to use 3D printing as the end product. Rather than transferring from 3D printing into, say, injection molding or mass production, engineers are discovering that the complexities 3D printing embodies are too valuable to dilute by moving to a more conventional production method. 3D printing becomes ideal or essential for production when:
- The design is only achievable through 3D printing. We see this most frequently in the aerospace industries when it comes to ducting and other non-load bearing, multifunctional units, but complex geometries in every field can find niche solutions here.
- The production volume may not justify the expensive overhead cost of tooling, blow molding or other methods. This is especially true in industries that only require 50 to 100 parts a quarter or year. 3D printing is the more economical choice and can meet these low- to medium-volume requirements for complex parts much more effectively, quickly and economically.
- The turnaround is shorter than a conventional production process is capable of achieving. 3D printing is a rapid process; there is no time lost developing a tool or waiting for a first shot off the mold. Design files are sent straight to the printer for fabrication and then post-processed as needed.
5.) Virtual Inventory
We are moving into a more increasingly connected world. Consumer products are continuously communicating with the Internet, perhaps feeding data on consumer use to the manufacturer themselves—at least, that’s the tune of the future. In this future, warehouses holding product and tooling inventory will be a thing of the past.
3D printing is already a part of that manufacturing plant of the future as the technology allows for manufacturers to have virtual inventories. Virtual inventories work like this: Designs are saved as files on computers, on USB drives and, more frequently, uploaded to the cloud. The 3D printing manufacturer then accesses those files, and prints and ships parts back to the designer or straight to the consumer as needed.
While these benefits of 3D printing may not get all the headlines, they are some of the more impactful applications. Supporting the supply chain and the manufacturing floor to boost productivity will have ripple effects throughout any industry. We are going to see more of these advanced efficiencies permeating production activities as 3D printing continues to rise past the hype and into everyday manufacturing.