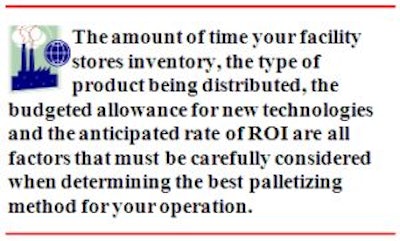
June 10, 2009 — More than 2 billion pallets are in use every day, dominating the landscape in most warehouses and distribution centers, while serving as the interface between the product and the mode of transportation.
In September 2008, the demand for pallets was forecasted to increase, with experts predicting that warehousing will show the most rapid gain, rising 6 percent per year through 2012. Although these figures were before the dramatic affects of the recession and the collapse of the markets, the fact remains: more than ever before, companies will look for ways to increase productivity, minimize manpower, and save money with effective palletization.
Palletization is the task of taking cases and stacking them in layers on pallets for storage and/or transportation. It's how the stacking is done, whether manually, automatically or semi-automatically, that varies from warehouse to warehouse. The amount and type of product being moved often determines which mode of palletizing will be used.
Assessing the Modes
Manual Palletizing is the most basic and also the most widely used method. Typically, workers remove cases from a conveyor line or an existing pallet load and stack them onto a pallet. The pallet resides on a pallet jack, forklift or the floor while being packed. The cases can either be stacked straight up (column stacked) or staggered (interweaving) in order to increase stability and sturdiness.
Semi-automatic Palletizing is used when case weight is a factor and workers are subject to back strain injuries, often resulting from manual palletizing. With a semi-automatic system, a conveyor delivers product to an operator who arranges the cases in layers on a variable height lift table. The operator utilizes a push button or a foot switch to raise and lower the load to the appropriate ergonomic height. This method increases efficiency and decreases back and shoulder injuries. Additionally, outfitting the variable height lift table with a rotating turntable also introduces efficiency and ergonomic benefits. With this feature, after all of the layers are stacked onto the pallet and it is ready for stretch wrapping, an operator can stay stationary and apply the wrapping as the pallet rotates in front of him or her.
Automatic Palletizing provides the fastest, most efficient and most ergonomically friendly method of palletizing. Currently, there are two common methods of automatic palletizing: conventional and robotic systems.
With the conventional method, cases travel along a conveyor and are delivered to a layer-building table, where the cartons are automatically turned and interlocked into the appropriate pattern. The pattern closely resembles a jigsaw puzzle and follows the specification that has been programmed into the equipment, thus eliminating human error. Once a layer is built, it can slide onto a stripper plate (sometimes referred to as a deck or apron); the stripper plate retracts horizontally, dropping each layer of cases onto a pallet load. This method is much like the old magic trick of pulling a tablecloth off without disturbing the dishes. Conventional automatic palletizers offer a broad range of speeds, with rates ranging anywhere from 10 to 200 cases per minute.
With the robotic method, pallets are built by utilizing a robotic arm that has been equipped with an end effector (clamp, vacuum, etc.) to pick cases from one location, often a conveyor, and stack them onto a pallet. The robotic method has become a preferred mode of palletization when employees are required to work in a harsh environment, such as stacking products in a freezer, or when the need calls for "rainbow stacking," which has become increasingly popular, particularly in the beverage industry.
The task of creating rainbow pallets involves combining more than one SKU on a pallet or customizing the pallets with various products. For a sports drink or soda company, it might be a pallet comprised of six or seven different flavors. The robotic arm picks up cases from multiple pallet loads to build layers of cases on one or more pallets while delivering a more accurate count than with manual palletizing.
Rainbow stacking has become increasingly popular with mass retailers such as Wal-Mart, Costco, Sam's Club and many grocery store chains. These retailers are looking to keep their costs down by having distribution centers ship products to them that are already customized to each of their locations. Rainbow stacking provides the retailer with a customized shipment to meet their specific inventory needs. This method is valuable to the retailer because they can order precise amounts of products for a variety of reasons, most notably to match their supply with their expected demand
Although robotic palletizers are the most effective method of building rainbow pallets, many companies have avoided using them due to the high cost and longer return on investment (an entry-level robotic system can cost at least $125,000). But as the technology is refined and prices are dropping, providing a shorter return on investment, robotic palletizers are gaining popularity.
Stretch Wrapping Success
Placing cartons on a pallet and moving it from Point A to Point B seems simple. Making sure the cartons stay on the pallet, however, is another matter, especially as the demands for increased throughput become a factor. Stretch wrapping is the most cost-effective way to keep loads secured on a pallet.
Just as with palletizing, there are several methods of stretch wrapping The method that is best for your operation depends on desired speed and available budget.
Manual Stretch Wrapping. This is the perfect method when the budget calls for a $40 roll of film and a $3 utility knife. Simply put, a worker grabs the end of the stretch wrap and walks around the pallet. It's slow, labor-intensive and inefficient, but it gets the job done.
Semi-Automatic Stretch Wrapping. If a company is stretch wrapping more than 15 loads per day, then chances are that some level of automation is needed to lower labor and film costs, as well as reduce the number of back injuries. There are two options.
With the first option, a pallet load is manually placed (via forklift or pallet jack) onto a turntable; as the pallet rotates, the stretch wrap is wound around the cases. In the second option, the pallet remains stationary and a rotary arm spins around the pallet, encasing it in film. Although not always the case, the stretch wrap is often applied and cut automatically, eliminating the need for a worker to hook a corner of the wrap to the pallet and cut it upon completion.
Both options are more efficient and cost-effective solutions when compared to manual stretch wrapping. In some cases, semi-automated stretch wrapping pulls the film so much tighter than its manual counterpart that it can triple the life of a roll of film.
Automatic Stretch Wrapping. These systems incorporate conveyors in which the pallet load automatically passes through the stretch wrapping machine. As the pallet load approaches the stretch wrapping machine, photoelectric eyes detect the load and instruct the system to automatically perform various tasks, including indexing the load, attaching and cutting the film, wrapping, etc. In automatic systems, very little worker assistance is required.
Coding the Load
In the distant past, the only way anyone knew what was on a pallet was to write the information on a piece of paper and tape it to the cases, either before or after stretch wrapping. But that inefficient system changed with the introduction of label printing and bar-coding in the late-1970s.
The principle of bar-coding is simple: a scanner differentiates the black bars from the white spaces and sends a decoded message to a computer. By identifying what's on a pallet, you know exactly where it is going and when it is received at its destination. It also gives distribution centers better control over their inventory by knowing precisely what product is coming into the building, where the product is stored, when the product is moved out of the building and when it has reached its destination.
Wood or Plastic?
Palletization is basically a three-step operation: stacking the cases, securing the cases and coding the load. Aside from advancements in technology, another change that may occur in the future is a shift from wood to plastic pallets, as companies look to keep long-term costs down and reduce worker injuries due to damaged pallets, splinters and protruding nails.
Ninety percent of the U.S. pallet market remains wood. However, plastic pallets continue to make inroads, particularly in the pharmaceutical, food and beverage, and grocery industries, because they are more durable, reusable and cost effective, and they weigh significantly less.
It's estimated that there will be 50 million plastic pallets in use by 2012, and that number could increase as more companies turn to automation to increase precision. A traditional 48"x40" wood pallet weighs about 50 pounds and can bear a load of 3,000 pounds, while a plastic pallet weighs around 35 pounds and can hold a 4,000-pound load.
Plastic pallets, however, can cost two to three times more than wood pallets. The advantage is that a plastic pallet has a longer "shelf life," an important factor when you consider that 700 million wood pallets either have to be made or repaired each year, due in part to what is believed to be a decline in wood quality. In fact, some companies have departments that do nothing but repair damaged wood pallets.
Still, there are advantages to both: wood works well with a forklift, while plastic works best on a conveyor. There are also issues when using wood with pallet flow, particularly when you have a long train of pallets in the pallet flow lane and a wood pallet breaks or splinters somewhere in the middle.
Conclusion
One of the key elements in creating the most efficient distribution center is utilizing proper palletizing methods to suit your specific needs. The amount of time your facility stores inventory, the type of product being distributed, the budgeted allowance for new technologies and the anticipated rate of ROI are all factors that must be carefully considered when determining the best palletizing method for your operation.
After diligent deliberation of the palletizing plan, other warehouse necessities like stretch wrapping techniques and the physical makeup of the pallet material can be selected. The future of palletizing technology is sure to grow along with the increasing demand for pallets.
About the Author: Paul Hansen is a senior project engineer for Lakeland, Fla.-based TriFactor LLC (www.trifactor.com), an integrator of material handling systems. Hansen has more than 10 years experience in the industry and holds a B.S. in Mechanical Engineering from the University of South Florida. He can be contacted at [email protected].
In September 2008, the demand for pallets was forecasted to increase, with experts predicting that warehousing will show the most rapid gain, rising 6 percent per year through 2012. Although these figures were before the dramatic affects of the recession and the collapse of the markets, the fact remains: more than ever before, companies will look for ways to increase productivity, minimize manpower, and save money with effective palletization.
Palletization is the task of taking cases and stacking them in layers on pallets for storage and/or transportation. It's how the stacking is done, whether manually, automatically or semi-automatically, that varies from warehouse to warehouse. The amount and type of product being moved often determines which mode of palletizing will be used.
Assessing the Modes
Manual Palletizing is the most basic and also the most widely used method. Typically, workers remove cases from a conveyor line or an existing pallet load and stack them onto a pallet. The pallet resides on a pallet jack, forklift or the floor while being packed. The cases can either be stacked straight up (column stacked) or staggered (interweaving) in order to increase stability and sturdiness.
Semi-automatic Palletizing is used when case weight is a factor and workers are subject to back strain injuries, often resulting from manual palletizing. With a semi-automatic system, a conveyor delivers product to an operator who arranges the cases in layers on a variable height lift table. The operator utilizes a push button or a foot switch to raise and lower the load to the appropriate ergonomic height. This method increases efficiency and decreases back and shoulder injuries. Additionally, outfitting the variable height lift table with a rotating turntable also introduces efficiency and ergonomic benefits. With this feature, after all of the layers are stacked onto the pallet and it is ready for stretch wrapping, an operator can stay stationary and apply the wrapping as the pallet rotates in front of him or her.
Automatic Palletizing provides the fastest, most efficient and most ergonomically friendly method of palletizing. Currently, there are two common methods of automatic palletizing: conventional and robotic systems.
With the conventional method, cases travel along a conveyor and are delivered to a layer-building table, where the cartons are automatically turned and interlocked into the appropriate pattern. The pattern closely resembles a jigsaw puzzle and follows the specification that has been programmed into the equipment, thus eliminating human error. Once a layer is built, it can slide onto a stripper plate (sometimes referred to as a deck or apron); the stripper plate retracts horizontally, dropping each layer of cases onto a pallet load. This method is much like the old magic trick of pulling a tablecloth off without disturbing the dishes. Conventional automatic palletizers offer a broad range of speeds, with rates ranging anywhere from 10 to 200 cases per minute.
With the robotic method, pallets are built by utilizing a robotic arm that has been equipped with an end effector (clamp, vacuum, etc.) to pick cases from one location, often a conveyor, and stack them onto a pallet. The robotic method has become a preferred mode of palletization when employees are required to work in a harsh environment, such as stacking products in a freezer, or when the need calls for "rainbow stacking," which has become increasingly popular, particularly in the beverage industry.
The task of creating rainbow pallets involves combining more than one SKU on a pallet or customizing the pallets with various products. For a sports drink or soda company, it might be a pallet comprised of six or seven different flavors. The robotic arm picks up cases from multiple pallet loads to build layers of cases on one or more pallets while delivering a more accurate count than with manual palletizing.
Rainbow stacking has become increasingly popular with mass retailers such as Wal-Mart, Costco, Sam's Club and many grocery store chains. These retailers are looking to keep their costs down by having distribution centers ship products to them that are already customized to each of their locations. Rainbow stacking provides the retailer with a customized shipment to meet their specific inventory needs. This method is valuable to the retailer because they can order precise amounts of products for a variety of reasons, most notably to match their supply with their expected demand
Although robotic palletizers are the most effective method of building rainbow pallets, many companies have avoided using them due to the high cost and longer return on investment (an entry-level robotic system can cost at least $125,000). But as the technology is refined and prices are dropping, providing a shorter return on investment, robotic palletizers are gaining popularity.
Stretch Wrapping Success
Placing cartons on a pallet and moving it from Point A to Point B seems simple. Making sure the cartons stay on the pallet, however, is another matter, especially as the demands for increased throughput become a factor. Stretch wrapping is the most cost-effective way to keep loads secured on a pallet.
Just as with palletizing, there are several methods of stretch wrapping The method that is best for your operation depends on desired speed and available budget.
Manual Stretch Wrapping. This is the perfect method when the budget calls for a $40 roll of film and a $3 utility knife. Simply put, a worker grabs the end of the stretch wrap and walks around the pallet. It's slow, labor-intensive and inefficient, but it gets the job done.
Semi-Automatic Stretch Wrapping. If a company is stretch wrapping more than 15 loads per day, then chances are that some level of automation is needed to lower labor and film costs, as well as reduce the number of back injuries. There are two options.
With the first option, a pallet load is manually placed (via forklift or pallet jack) onto a turntable; as the pallet rotates, the stretch wrap is wound around the cases. In the second option, the pallet remains stationary and a rotary arm spins around the pallet, encasing it in film. Although not always the case, the stretch wrap is often applied and cut automatically, eliminating the need for a worker to hook a corner of the wrap to the pallet and cut it upon completion.
Both options are more efficient and cost-effective solutions when compared to manual stretch wrapping. In some cases, semi-automated stretch wrapping pulls the film so much tighter than its manual counterpart that it can triple the life of a roll of film.
Automatic Stretch Wrapping. These systems incorporate conveyors in which the pallet load automatically passes through the stretch wrapping machine. As the pallet load approaches the stretch wrapping machine, photoelectric eyes detect the load and instruct the system to automatically perform various tasks, including indexing the load, attaching and cutting the film, wrapping, etc. In automatic systems, very little worker assistance is required.
Coding the Load
In the distant past, the only way anyone knew what was on a pallet was to write the information on a piece of paper and tape it to the cases, either before or after stretch wrapping. But that inefficient system changed with the introduction of label printing and bar-coding in the late-1970s.
The principle of bar-coding is simple: a scanner differentiates the black bars from the white spaces and sends a decoded message to a computer. By identifying what's on a pallet, you know exactly where it is going and when it is received at its destination. It also gives distribution centers better control over their inventory by knowing precisely what product is coming into the building, where the product is stored, when the product is moved out of the building and when it has reached its destination.
Wood or Plastic?
Palletization is basically a three-step operation: stacking the cases, securing the cases and coding the load. Aside from advancements in technology, another change that may occur in the future is a shift from wood to plastic pallets, as companies look to keep long-term costs down and reduce worker injuries due to damaged pallets, splinters and protruding nails.
Ninety percent of the U.S. pallet market remains wood. However, plastic pallets continue to make inroads, particularly in the pharmaceutical, food and beverage, and grocery industries, because they are more durable, reusable and cost effective, and they weigh significantly less.
It's estimated that there will be 50 million plastic pallets in use by 2012, and that number could increase as more companies turn to automation to increase precision. A traditional 48"x40" wood pallet weighs about 50 pounds and can bear a load of 3,000 pounds, while a plastic pallet weighs around 35 pounds and can hold a 4,000-pound load.
Plastic pallets, however, can cost two to three times more than wood pallets. The advantage is that a plastic pallet has a longer "shelf life," an important factor when you consider that 700 million wood pallets either have to be made or repaired each year, due in part to what is believed to be a decline in wood quality. In fact, some companies have departments that do nothing but repair damaged wood pallets.
Still, there are advantages to both: wood works well with a forklift, while plastic works best on a conveyor. There are also issues when using wood with pallet flow, particularly when you have a long train of pallets in the pallet flow lane and a wood pallet breaks or splinters somewhere in the middle.
Conclusion
One of the key elements in creating the most efficient distribution center is utilizing proper palletizing methods to suit your specific needs. The amount of time your facility stores inventory, the type of product being distributed, the budgeted allowance for new technologies and the anticipated rate of ROI are all factors that must be carefully considered when determining the best palletizing method for your operation.
After diligent deliberation of the palletizing plan, other warehouse necessities like stretch wrapping techniques and the physical makeup of the pallet material can be selected. The future of palletizing technology is sure to grow along with the increasing demand for pallets.
About the Author: Paul Hansen is a senior project engineer for Lakeland, Fla.-based TriFactor LLC (www.trifactor.com), an integrator of material handling systems. Hansen has more than 10 years experience in the industry and holds a B.S. in Mechanical Engineering from the University of South Florida. He can be contacted at [email protected].