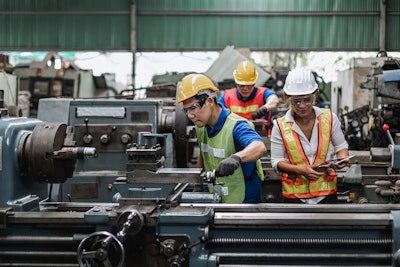
Amid the buzz surrounding artificial intelligence, a false mentality has emerged: technology versus employees. Headlines often paint a future where machines replace human workers; however, this outlook misses the purpose of AI entirely. The transformative potential of AI paired with mobile and connected worker technology for frontline operations isn't about replacement, but augmentation. By viewing AI as a tool to enhance human capabilities, organizations effectively address critical training and skills challenges while empowering their workforce.
This approach is particularly crucial for the supply chain and manufacturing sectors, which are grappling with an unprecedented skilled labor crisis. The rapid pace of technological change, coupled with an aging workforce and evolving job requirements, has created a perfect storm. A joint talent study by Deloitte and The Manufacturing Institute projects that 3.8 million net new employees will be needed between 2024 and 2033, with nearly half of those positions likely to remain unfilled.
The crisis is already critical, with 48 states reporting manufacturing labor shortages, some facing job deficits as high as 89%. As the 'great resignation' has morphed into the 'great reshuffle,' manufacturers have struggled to retain workers, leading to supply chain disruptions and decreased productivity.
As traditional training methods prove too slow, inflexible and insufficient to meet these challenges, connected worker platforms built on an AI foundation provide enhanced frontline worker augmentation, and deliver tangible ROI. The future of frontline work will be shaped not by AI alone, but by its strategic integration with human expertise and continuous improvement, creating a more capable, efficient and adaptable workforce across the entire supply chain ecosystem.
AI-Powered Personalized Learning
AI-powered connected worker technologies transform how supply chain and manufacturing organizations approach workforce development. These innovative tools analyze vast amounts of operational data to create personalized learning experiences that support workers throughout their entire lifecycle – from hiring and onboarding to ongoing training, worker engagement, and retention.
The impact of AI-driven learning solutions is significant. According to a report by McKinsey, companies embracing AI-powered learning reduced training time by up to 50% and improved learning outcomes by up to 60%. When paired with purpose-built connected worker solutions to analyze vast amounts of operational data these systems can provide insights that were previously unattainable, creating personalized learning experiences for each worker.
Additionally, instead of relying on one-size-fits-all training programs, AI can tailor instruction to individual needs, learning styles and job roles. For instance, a new manufacturing assembly line worker might receive step-by-step guidance on equipment operation and safety protocols, while a seasoned machine operator might ask for help on advanced troubleshooting scenarios for complex machinery breakdowns.
One of the most significant challenges facing organizations with large frontline workforces is the loss of institutional knowledge as experienced workers retire or move on. AI-driven connected worker platforms offer a solution by capturing and digitizing this valuable expertise. AI analytics and software can transform years of experience into accessible, shareable assets that can be used to train the next generation of workers.
AI doesn't just facilitate initial training; it supports continuous learning and improvement. By analyzing performance data in real-time, these systems identify areas where workers might be struggling and provide immediate, contextualized support. Smart connected worker platforms deliver just-in-time personalized instructions, video tutorials or even connect the worker with subject matter experts for informed guidance.
Enhancing Frontline Capabilities and Continuous Improvement
Implementing AI-powered connected worker technology goes beyond just preserving knowledge; it's about continually enhancing frontline worker capabilities and fostering a culture of continuous improvement. Advanced digital assistants that leverage Generative AI, often deployed using tablets manufacturing workers carry, guide staff through complex procedures, answer questions on the spot, instantly provide references to training manuals and even predict potential production issues before they occur. This not only improves efficiency but also reduces errors and enhances worker safety on plant floors.
These modern tools also play a vital role in retention by providing opportunities for growth and development. AI can analyze performance data to identify individual strengths and areas for improvement, suggesting personalized training paths and career development opportunities. This data-driven approach to talent management ensures that workers feel valued and see a clear path for advancement within the organization. Smart connected worker systems encourage workers to constantly refine their skills and processes. AI-powered analytics can use performance data to identify bottlenecks or inefficiencies that might not be apparent to human observers, and then suggest process improvements or additional training to enhance overall productivity. This creates a virtuous cycle of learning and improvement, where both workers and processes become more efficient over time.
The Symbiosis of Tech and Talent
While the benefits of AI in frontline workforce development are clear, it's crucial to remember that the technology is a developing tool, not a fix-all. The most successful implementations of AI are those that recognize and value the irreplaceable human elements of critical thinking, hands-on expertise, and adaptability.
AI-powered tools can provide data and insights, but it takes human judgment to interpret this information in the context of broader organizational goals and worker needs. It can suggest improvements, but it takes human creativity to innovate and implement new solutions. And while AI can facilitate learning, it's human curiosity and successful management that fuel the desire for continuous improvement.
As we look to the future of frontline work across industries, it's clear that success will not come from choosing between technology and employees, but from creating a symbiosis between the two. By leveraging AI to augment worker abilities, organizations create frontline workers that are more skilled, highly adaptable, and better equipped to meet the challenges of an ever-changing business landscape. The smart workplaces of the future will be created – not through automation alone, but through the powerful combination of cutting-edge technology and human ingenuity.