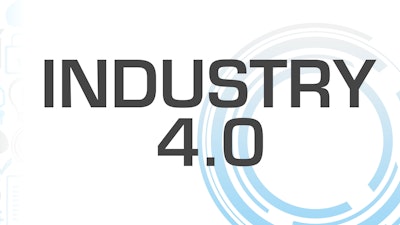
Automation and robotics have both proved to be invaluable in recent years, with the benefits of using advanced technologies far more wide-ranging and able to offer a significant competitive advantage over more traditional methods of production.
A knowledge of smart technologies can optimize production by improving quality and delivering it consistently, while also lowering cost and reducing downtime. Therefore, manufacturers must find ways to improve their entire operation. In doing this, they can attract customers seeking manufacturing partners who can speed time to market, quickly ramp new production, reduce waste and improve quality. Many are also looking to advanced Industry 4.0 technologies to create digital factories, what some call the factory of the future.
At the Heart of Industry 4.0 is Data
Digitalization enables data to be shared between machines, within a factory and between factories, suppliers and customers. This allows a much higher level of visibility and efficiency to be achieved, benefiting every stage of the product life cycle.
For example, the process of setting up a production line can be significantly improved using simulation and modelling technology. At the early stages of production planning, an entire production line can be simulated virtually and allow customization of multiple factors including the design plan, production layout, human resources needed and materials used.
Testing different methods and configurations in a virtual world can save the time, cost and material waste of experimenting in the real world. It also allows the optimized production data to be shared with product designers, customers and the production team. If a change is needed, it is simple to run a new simulation model that allows analysis on multiple layers for each function.
The ability to digitize the entire lifecycle of a product and the production configuration greatly increases real time decision making, efficiency and quality.
Driving Adoption
For the past 10 years, manufacturers have been focused on testing the promise of Industry 4.0 for many applications. For machine maintenance, advanced digitized systems can use artificial intelligence (AI), big data analytics and Industrial Internet of Things (IIoT) sensors to monitor and anticipate maintenance and resolve failures before they can occur.
Advanced digital factories rely on implementing interconnectivity, automation, real time data and other innovative technologies to help drive throughput, optimize processes and streamline efficiencies.
The massive supply chain disruptions over the past few years have also encouraged European governments to push for greater localization of the supply base to make manufacturing faster and closer.
It is not uncommon to make the same product at multiple sites around the world, so that products are closer to the end customer. To achieve consistent quality and production volumes, make use of automation and robotics. These technologies can streamline repetitive assembly tasks, reduce variability and the possibility for error, while increasing safety and freeing up workers for more valuable work.
The Human Factor
Upskilling people in this working environment is important too. For example, with automation and digitization, systems-thinking becomes incredibly important. With so many connected machines, employees need to understand the ripple effect of their actions. For example, when they change something on one section of the line, it won’t have a negative downstream impact on another area.
Continuously developing the capabilities of operators, line technicians and automation experts to operate equipment will help streamline the introduction of new technologies and keep operations running smoothly. Collaboration between workers at other sites is also facilitated by technology.
At an advanced level, teams can use augmented reality to enable colleagues across the world to work together to troubleshoot issues on equipment or production lines. At the simpler end, video conference applications are commonly used to connect production staff and allow organic knowledge sharing.
The Road Ahead
Industry 4.0 technologies represent a much-needed step forward that helps to improve efficiency and quality. The increased and detailed data helps people at every level of business make better decisions, more quickly.
The right time to think about implementing or expanding Industry 4.0 technologies is now. If you are just beginning your journey, look for solutions that:
- Simplify repeatable dangerous, dull, dirty, or difficult tasks and free up workers’ time for higher level, more complex activities
- Empower employees from the shop floor to the corner office with real-time data that can enable quicker decisions
- Drive communication, flexibility and ensure resilience throughout the entire manufacturing process
While technology may drive innovation, people are still at the heart of manufacturing and are the critical ingredient to implementing, analyzing and managing the technology in place.