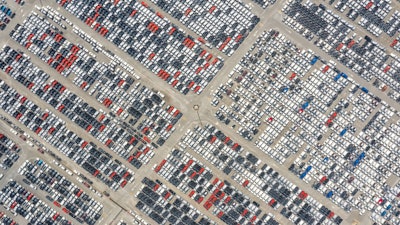
Efficiency is at the heart of any successful supply chain. The automotive industry is no different, relying heavily on efficient transportation and logistics to ensure the timely delivery of vehicles to dealerships and customers. However, one mission-critical element that too frequently presents challenges to automotive original equipment manufacturers (OEMs) is congestion at finished vehicle yards, where vehicles are accessorized and staged for transportation to the dealership. Congestion within the finished vehicle yard and limited visibility causes delays in the outbound logistics, leading to late deliveries and contributing to the ongoing supply chain issues in the automotive industry. To address this, OEMs are leveraging the power of real-time location systems (RTLS) to gain visibility into finished vehicle yard operations and streamline processes for yard workers, as well as truck drivers who haul vehicles to dealers for delivery to customers.
Current Challenges
Finished Vehicle Logistics (FVL) and vehicle processing center (VPC) yards are challenged with complicated operations largely due to the high volume of vehicles and high-tempo movement within the yard. Compounding matters, as cars progress through the finishing process they are often moved multiple times and to various locations based on what is required to ready them for delivery. Sometimes they are moved needlessly, creating extra, non-value added work. Unfortunately, a large-scale lack of real-time visibility into intra-yard vehicle movements results in difficult-to-locate inventory, ineffective allocation of resources (employees can spend hours searching for a single vehicle) and increased congestion—all of which significantly impact the productivity of yard workers and create obstacles for truck drivers who rely on timely access to their loads for delivery.
Similar to a yard at a large distribution center, FVL yards are in a state of constant motion. To solve this challenge, many manufacturers and distribution centers have implemented Yard Management software to help manage the vehicle in the yard. But without knowing trailer locations in real-time, knowing the best way to get vehicles from point A to point B are “best guesses.” While this technology does theoretically help with that task, it lacks automated, real-time location updates, instead requiring manual yard checks or for an RFID reader to patrol the yard to update the new locations of trailers as they are moved. In a small trailer yard, this technology may help with the challenge of locating trailers, but FVL yards can also span hundreds of acres and contain more than 20,000 vehicles, all which move multiple times before leaving the yard. No amount of manual yard checks or patrolling can keep pace with the amount of vehicle movements made, ultimately leading to wasted time and frustrated employees searching for vehicles. In order to help automate the process of location vehicles, many FVL customers are solving this problem with RTLS, which takes traditional real-time visibility technology to the next level – and it’s paying off for OEMs in spades.
The RTLS Advantage
The introduction of real-time location technology to the FVL industry provides exactly the kind of logistical asset visibility OEMs and FVL managers have been missing for far too long. Incorporating a wide array of peripheral technology such as GPS, Radio Frequency Identification (RFID) and Bluetooth, RTLS technology tracks the location and movement of automotive assets in real-time, allowing stakeholders to view accurate and up-to-date information on asset location within the yard–a significant shift from traditional yard management technologies that provided a mostly static view of assets on a screen.
RTLS not only helps mitigate the likelihood of congestion, but features like Bluetooth-enabled asset tags that shine ultra-bright LED lights with the tap of a smartphone, make identifying the vehicles that need to be transported significantly easier at night and in low-visibility weather. This ensures that yard operations can continue seamlessly, irrespective of external conditions, and that truck drivers can access their loads on time, improving overall supply chain efficiency.
With real-time asset tracking, OEMs and FVL yard managers have the ability to monitor and manage vehicle yard operations as they happen, unlocking a level of sophisticated visibility previously unheard of in FVL. This visibility delivers valuable insights–not only into how efficiently assets are being moved within the yard–but also into who, specifically, is moving them. For example, RTLS systems can track and record the time taken for yard workers to move assets from one location to another, providing data on their productivity and performance. This data can be analyzed to identify bottlenecks, inefficiencies and areas of improvement. Using this analysis, yard managers can implement changes in processes, allocate resources more effectively and optimize in-yard asset movement, resulting in reduced congestion, improved worker efficiency and improved outbound logistics metrics, like OTIF.
Impacting Lives of Workers
Streamlining operational processes and boosting efficiency are only part of the RTLS equation. RTLS technology also has a substantially positive impact on the lives of the people doing the day-to-day work in the FVL industry. Yard workers, for instance, play a crucial role in the effective and punctual movement of assets within the yard–and both their bandwidth and productivity are greatly affected by inefficient operations. By providing real-time visibility into yard operations and optimizing processes, RTLS technology can help reduce the amount of physical work and stress levels of workers, creating a happier and more focused work environment.
Arguably the greatest “boots-on-the-ground” benefactors of RTLS are the truck drivers tasked with delivering cars to the dealer network. Largely compensated by the number of deliveries made, drivers need to get in and out of all yards - whether trailer, FVL or VPC as quickly as possible. To that end, drivers will avoid picking up loads at locations where outbound logistics processes are inefficient, instead prioritizing those with technology like RTLS which can make their jobs’ easier. By harnessing the power of real-time asset tracking technology, FVL managers and OEMs acquire invaluable insight into FVL yard operations, allowing for processes to be streamlined and improving the lives of yard workers and truck drivers—the backbone of the automotive supply chain. These insights also make ROI easier to understand and facilitate data-driven decision making. Keeping mistakes and inefficiencies low and morale and ROI high, RTLS will continue to boost efficiency in ways we have yet to even imagine. And in supply chain logistics, this trifecta means everything.