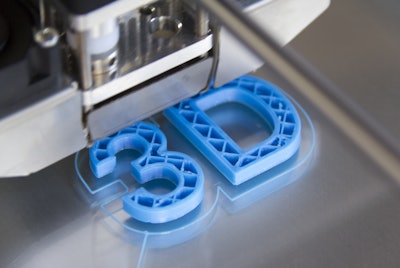
Global supply chains continue to face massive disruptions caused by a growing number of unforeseen events—from a traffic jam at the Suez Canal to myriad natural disasters and a more-than-a-year-long pandemic that upended sourcing, procurement and production worldwide.
Through all these unforeseen events, digital manufacturing has stepped to the forefront as an invaluable solution to meeting the escalating demands for supply chain resilience. In particular, localization and customization—as well as innovations in 3D printing materials, technologies and processes—are closing supply chain holes while speeding the delivery of quality products globally.
Below are five ways that digital manufacturing is elevating supply chain resiliency.
1. Accelerating production without massive manufacturing investments or delays
Digital manufacturing doesn’t require deployment of massive, global supply chains and large-scale manufacturing facilities to achieve economies of scale. Companies also can avoid the high costs of sourcing, procuring and building expensive tools, fixtures and molds associated with traditional manufacturing.
In contrast, digital manufacturing relies on software-driven processes to automate manufacturing workflows that transform digital designs into physical products in days, not months. This faster, more efficient and cost-effective approach is quickly gaining traction over traditional manufacturing, which is characterized by slow, costly and cumbersome manual methods.
2. Fulfilling product needs just-in-time while eliminating inventory stockpiles
The days of maintaining huge warehouses stocked with physical inventories are coming to an end, thanks to the agility with which digital manufacturing can make products on-demand for just-in-time delivery. Once inventory costs exceed the price of on-demand manufacturing, 3D printing becomes a much preferred and highly economical option.
The value of digital manufacturing increases exponentially when dealing with slow-moving inventory or end-of-life products with low turnover rates. It makes little sense to maintain supply chains for these items, especially when replacement parts can be produced digitally and delivered as needed.
3. Localizing production results in faster, more efficient deliveries of parts
Mainstream manufacturers have long touted their ability to build huge global supply chains with millions of components and parts from countless suppliers around the world. Too often, however, these behemoth supply organizations are bogged down by inefficient, manual sourcing and procurement methods.
There are numerous issues with capacity, logistics and carriers as well as customs channels being clogged, most notably in the UK and India. This likely will continue to be a persistent issue as time goes by, and it’s something that can be addressed effectively with digital manufacturing.
Ideally suited for localized production, additive manufacturing capabilities that leverage a distributed network of preferred partners can dramatically reduce the distance between production facilities and end-customers. Utilizing a distributed, digital manufacturing model also can alleviate local capacity constraints.
The ability to switch between suppliers and production partners as production needs and delivery deadlines dictate is another major supply chain benefit facilitated by digital manufacturing.
4. By supporting increasing needs for product personalization and customization
Traditional supply chains have been designed to orchestrate mass production of huge volumes of mostly static product designs. As a result, they fall short when it comes to keeping pace with ever-increasing demands for product personalization and customization. Digital manufacturing, however, is designed specifically for precise and efficient production of made-to-order products.
In an era where consumers are increasingly requesting goods that are made to their exact specifications, 3D printing meets the call. Relying on the just-in-time delivery that is possible with additive manufacturing also means that supply chains are not bogged down with items awaiting delivery yet stuck in warehouses far from their final destinations.
5. Delivering end-to-end automation and workflows to improve supply chain agility, flexibility
While digital manufacturing is poised to improve today’s supply chains, it can present a high barrier to entry for organizations that have been slow to digitize core business and manufacturing processes. It’s critical to simplify digital manufacturing complexities while boosting supply chain resiliency by easing the shift to digital manufacturing.
This is accomplished through an integrated set of end-to-end capabilities, including intuitive material selection, instant quoting, service level options, automated and personalized feedback from design through to printing, post-processing, complete quality checks, fulfillment and distribution.
Looking ahead
When it comes to supply chain resiliency, digital manufacturing has proven to remove barriers while speeding the development and delivery of products that drive significant value for business enterprises worldwide. Digital manufacturing already has made a major mark across different industry segments, such as eyewear, dental, hearing aids and medical. As more companies continue to innovate their product ideas, especially those requiring urgency and customization, 3D printing is poised to transform how game-changing product ideas are brought to life.