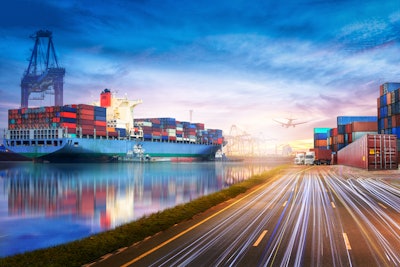
During the last two years, the pandemic has been a disruptive factor that has affected supply chains and suppliers’ production capacity. Now, the Russian invasion of Ukraine and recent factory closures in Shanghai due to prolonged COVID-19 lockdowns, are further disrupting global supply chains. Since the beginning of the invasion, the world has experienced impacts on raw materials, precious metals, oil prices and logistics challenges.
As rising commodity prices have already shown, the war in Ukraine is constraining the short-term supply of natural resources and other raw materials vital to businesses around the world, and there are fears of worse to come in the months ahead. One reason why the war is so impactful on the global supply chain is because a large percentage of finished metals are sourced and manufactured in the countries involved, especially aluminum.
Many companies are implementing their business continuity plans to establish the immediate risk from suppliers in Ukraine, Russia, and the neighboring countries along with a second order effect of suppliers. All of these decisions are set against the backdrop of many new import/export restrictions and government trade policies to move supplies into and out of the affected region.
Ongoing disruptions and volatility in global logistics have exacerbated component shortages, impacting major trade lines across all transportation modes (air, ocean, rail, and courier). This domino effect has led to a considerable rise in prices due to capacity constraints caused by the virus outbreak and geopolitical situations.
The current market situation: overwhelming demand is outstripping supply, and manufacturers are no longer able to support orders with short lead times. Order backlogs average three to four months, while the backlog for automotive grade Multilayer Ceramic Capacitors (MLCCs) is over five to six months.
Every quarter, Jabil highlights its market vision as a result of managing 27,000+ suppliers and over 700,000 parts in its product development processes. Some of our insights show that the most significant declines in production have been seen in the automotive sector, which is also reflected in the number of businesses reporting input shortages as a factor hindering production.
Here is a snapshot of Jabil’s forecast:
- Compounding Supply Challenges: Many semiconductor product families are already experiencing lead times of 40+ weeks, with some suppliers now quoting 64-week lead times. Suppliers across many commodities continue to EOL legacy product families and are investing in newer, more profitable technologies.
- Raw Materials: As Ukraine is a country rich in raw materials, the world is experiencing an immediate impact on pricing for gold, zinc, nickel, copper and aluminum. These metals, all used in various electronic components, were already at elevated levels prior to the Russian invasion. Neon gas is a critical material used in semiconductor manufacturing and primarily supplied from Ukraine. Most integrated device manufacturers and foundries have up to a years’ worth of inventory, which should buffer the supply situation in the short term. However, it could become a problem in the months ahead if supply continues to be disrupted – especially with the current elevated demand.
- COVID-19 and geopolitical tensions cause uncertainties: Oil prices spiked to over $110 per barrel following the Russian invasion, causing immediate impacts on land, air and sea logistics. Some of Europe’s largest metal suppliers saw their energy prices nearly double within days of the invasion, on top of costs that were already increasing before the war began. Additionally, COVID-19 lockdowns in China are continuing to create unplanned production and logistics disruptions with ramifications on global supply, component lead times and material costs.
As suppliers adopt different product development and capacity expansion plans based on their focused business strategies, it is essential to align the technology needs and supplier selection to enable the most effective sourcing strategy.
Furthermore, according to an industry report from Supplyframe, the intelligence platform for the global electronics value chain, the shortage of semiconductors could stretch into the first quarter of 2023 and continue to hamper production of technology-dependent products like automobiles. Likewise, global manufacturers can expect severe supply constraints and cost inflation pressure for many component categories in 2023.
And, what happens when a product is scarce but indispensable? Prices skyrocket, lead times increase, more provision costs are incurred, and manufacturer margins may be squeezed.
The global supply chain remains very tight due to continued strong demand, and it is difficult for manufacturers to manage the mix and continued bottlenecks in specific product families. And, although most suppliers’ factories are running at almost full capacity, there are still certain manufacturers that are further constrained from the spread of COVID-19.
It is worth mentioning that demand from various industries for connected devices, including automotive, 5G and wireless, and IoT, is expected to continue to drive the increased consumption of semiconductors - especially the automotive market, which remains the most talked about business vertical. Most suppliers view this market as critical to attaining substantial revenue growth over the coming years.
Uncertainties in the supply chain industry are expected to persist until at least the end of 2022 - and in the case of the global chip shortage, into 2023 - as backlogs are cleared and demand is met.
Click here to hear more about procurement during today's disruptions:
How to mitigate supply chain risk
Mitigating risk has long been a driving force behind digital transformation efforts for global supply chains. But as factories closed and supply pipelines dried up in the aftermath of the pandemic outbreak, risk reduction has taken on even greater importance.
As capacity constraints drive extended lead times and price increases become the norm for the coming quarters, there are a few ways companies can mitigate supply chain risk and minimize component price increases:
- Alignment: Companies must ensure that design teams continue to stay aligned with their suppliers, technology roadmaps and capital investment plans.
- Supplier qualification: Qualifying multiple suppliers for common products is important, continually reviewing new suppliers as companies expand their product portfolios and capabilities. In addition, as part of the qualification process reviews, it is vital to monitor suppliers’ global footprints to mitigate concentration from any one country or region.
- Visibility: Provide as much visibility as possible to the supplier partners. This way companies can plan for their product capacity and any potential longer term capital investments.
- Increased lead times in planning systems and additional buffered inventories: Companies should update planning systems to reflect new lead times immediately, as pull-ins and support for unscheduled orders will be very difficult - especially with lead times moving out across most commodities.
In addition to these recommendations, it is important for companies to keep in mind that traditional supply chain practices that worked well in the past may no longer be relevant in today's environment. Regardless of what the future holds for component supply, businesses must have a solid supply chain strategy, complete with sourcing plans and strong supplier relationships, to protect their own operations.
Based on current market behavior, companies must explore alternative sources of supply or compounds. Strong partnerships with key suppliers will provide the opportunity to leverage their internal capabilities to offset the cost of change and validation process in analyzing alternative compounds for production, face market challenges and price fluctuations. Suppliers should have a good structure to execute the hedges.
Recommended supply chain actions (dual sourcing, use of safety stocks, safety lead times and extended planning horizons) are essential to mitigate risk of increased lead times and last-minute delivery delays. Having multiple supplier options instead of a single source will provide this resiliency and further mitigate commercial impacts.