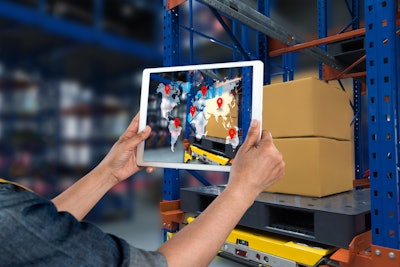
When it comes to planning, companies have mastered optimizing their strategies within their own four walls. We’re finding, however, that organizations struggle to take it beyond the four walls and bring a planning solution together that accounts for suppliers and vendors.
One way that companies can improve upon their existing planning methods and optimize the way their organization functions is to adopt a digital supply chain planning solution. Supply chain planning systems help organizations plan around a number of variables, arming them with the data and insights they need to ensure they can meet their desired business outcomes. Digitally connecting planning from the top floor to plant floor operations provides insights that benefit the entire operation, and allows companies to identify patterns, react quickly to demand, and eliminate or at least minimize and manage excess product overstocking.
One of the main benefits of implementing digital supply chain planning systems is that they make complex data more digestible. Instead of relying on spreadsheets, digital supply chain planning tools utilize analytics, AI, and machine learning to quickly process massive amounts of data and keep up with the demands of their customers. Using data to predict inventory levels is a vital step to understanding the supply and demand of manufacturers’ products. The ability to use contextualized information to provide meaning to the data is the fundamental idea in supply chain planning science. By factoring in geography, product type, customer type, and other meaningful aggregations, manufacturers can identify patterns and make better decisions. This data also helps them more effectively forecast consumer trends and respond more proactively to changes in supply and demand.
Click here to hear more about digital supply chains:
Similarly, digital supply chain planning tools provide real-time, comprehensive visibility into the supply chain. When a market or demand shift happens, manufacturers can confidently respond with agility and real-time insights from across the business to ensure inputs are met. For example, if a manufacturer were alerted to a backup at a port, such as those seen in Los Angeles last year, they could then reroute inventory to another location. If you don’t plan around reality and constraints, you’re not going to achieve the goals of the company without added costs and chaos included. Implementing a digital supply chain planning tool optimizes the supply chain, which in turn, improves lead times, accurate inventory levels and production efficiency, while also reducing costs.
When it comes to implementing a supply chain planning tool, there are a few factors to consider before finalizing a decision.
Make sure everyone’s on board
Collaboration between sales and marketing, operations, finance, and other areas that impact order fulfillment are crucial. Tools that enable better and more sustainable sales and operations planning and automated forecasting, like supply chain planning, are equally critical.
To get full approval, identify an individual early-on who is on board with the tool. He or she can serve as a champion and help you navigate organizational buy-in as you progress. Following that initial buy-in, ensure that every relevant stakeholder- those who will be using the software itself- is involved in the selection process.
Lastly, gain an understanding of each stakeholder’s needs and perspectives and incorporate those in your assessments. Take the time to get their responses and ensure that their needs will be met with a certain software. It’s important to get their opinion about the most important aspects of their job so that you don’t leave something out. Engaging stakeholders during- and especially at the beginning of- the process will help reduce risks and increase buy-in.
Do your homework
Ensure that the tool fits within your existing enterprise and IT landscape. A lack of integration between a planning solution and the relevant ERP systems as well as lack of helpful data sources like point of sale and market forecast data are notorious bottlenecks to efficiency. Be sure to ask potential vendors about their methods for integrating with your ERP systems and other data sources, and explore their ability to support forecasting and planning, as well as automating the execution of your plans.
Similarly, ask the vendor if they have specific industry experience in your manufacturing sector. If they’ve worked with similar companies, they’ll understand the various challenges and pressures faced by your organization, which will prove beneficial should any issues arise. They’ll also be able to take an approach that ensures you achieve the objectives you want from your software.
Without this vetting process, companies can potentially end up with a tool that can’t function in their current systems, creating more problems for manufacturers.
Align on timing
Just as supply chain planning software can help your business plan and prepare for the unexpected, you need to do both as part of the selection process itself. Take stock on busy seasons and whether your IT team has any other projects that might be deployed during the same period. The last thing you want to do is make the process more time-consuming or during a critical business period.
If timing is a priority, consider a tool that ranks high for intuitiveness and thus will come with a shorter learning curve. Responsive support and online documentation are other factors to consider when time is a key driver.
Finally, determine the cost of the status quo across the company. In addition to making sure your software selection activities dovetail with other business activities, you’ll want to have a solid sense of how soon your business will need your new planning solution in place. How much would a potential delay in implementing a new solution cost you? Taking timing into consideration and ensuring that your company can continue standard processes and is well equipped to make it through any delays will allow for a seamless transition.
To truly be successful in today’s economy, manufacturers need the right data. Having the right data means orders are closed on time and inventory levels and planning attributes are accurate. If those are wrong, then manufacturers won’t be making decisions based on reality, ultimately costing them time and money to get it right. Digital supply chain planning can offer manufacturers the processes they need to get the right data, helping them create better forecasts to align their supply requirements to achieve excellent customer outcomes. In a rapidly changing world, manufacturers can ill afford to pick a supply chain planning tool that will set them back. As such, it’s essential that manufacturers choose the tool that will be best for their organization.