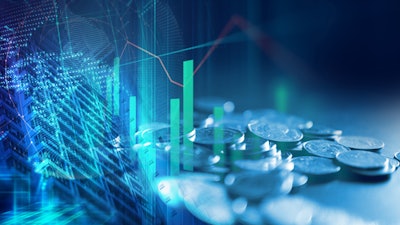
The Coronavirus disease (COVID-19) has had an outsized impact on industries that rely on physical operations, and supply chain and logistics service companies have not been spared.
One challenge that has been particularly thorny for this industry has been finding a middle ground between building a healthy balance sheet and ensuring equipment and assets are continually upgraded. While maintaining and upgrading truck fleets is a necessary and vital part of continued success in the transportation industry, many companies are understandably budget-conscious about embarking on such costly capital expenditures in a time when even having positive cashflow is an achievement. Further demonstrating the impact of COVID-19 on the industry, ACT Research forecasted that Class 8 sales will fall to 194,000 in 2020 compared to 281,000 in 2019. ACT also forecasted that sales will rise to 232,000 in 2021.
So, how can supply chain and logistics service companies strike a balance? Start by getting to the bottom of these three questions:
1. When should I upgrade?
It is tempting to upgrade only when there is a pressing need, such as if a truck breaks down or an OEM ends service support for a piece of equipment. But, this wait-and-see approach can backfire. For example, if you lose a truck from your fleet and spend weeks finding a new one, this decreased capacity is already costing money.
Don’t wait until the wheels are falling off to upgrade. Keep a pulse on potential cost-saving improvements while equipment still has useful life. Be vigilant of expiring warranties. While the initial cost may decrease cash on hand, upgrading may help preserve your balance sheet and save on maintenance issues in the long run. Transportation fleets with newer equipment experience increases in performance and a decrease in maintenance costs.
2. Which upgrades should come first?
Prioritizing and staying on top of upgrades is essential to remaining competitive in the market, but given a finite upgrade budget, where is money best spent?
The first step is to assess which assets are obsolete. By squeezing the life out of obsolete assets, you might feel like you are being cost-effective. However, newer equipment is so much more efficient and less costly to maintain, that deviating from normal asset replacement cycles can increase the total cost of operation (TCO). Stick to the replacement cycle, which may vary by fleet and is primarily based on factors such as usage, hours, mileage and duty cycle.
Telematics has also become an important aspect of the modern equipment fleet. Telematics supplies near real-time information on the operation of the machines, allowing supply chain companies to measure periods of use, fuel consumption and other service interval details. Supply chain companies should closely watch innovative technologies like automated equipment fleets and artificial intelligence (AI)-powered predictive maintenance, as they both continue to gain traction in the industry.
3. How can I maintain a healthy balance sheet?
Increasing profitability while remaining competitive in equipment upgrades can be difficult, but there are many steps supply chain companies can take, even amid COVID-19.
First, limiting equipment downtime is crucial to the success and profitability of transportation companies. Taking steps to ensure annual maintenance scheduling increases the number of in-service units available. Additionally, strategic parts planning and varied scheduled maintenance reduce the need for unforeseen and inevitable upgrades, improving machine availability.
Second, consider the merits of leasing. Leasing equipment, rather than the significant upfront cost to purchase the units outright, can free up additional cashflow to use in fleet expansion, maintenance and repair, additional drivers, fuel and customer service, which are all relevant to ensuring client satisfaction and expanding business in a tough market.
Keep an eye on best practices amid financial upheaval
While balancing upgrades with cash flow will always be a negotiation, and each company might reach a different conclusion, there are three aspects of equipment upgrade and operation should be considered:
Acquire equipment from original equipment manufacturers (OEMs) and invest in spare parts. With dealer locations throughout the United States, purchasing from the OEMs can limit equipment downtime which is vital to your bottom line. And, don’t just buy the equipment—make sure you have the parts as well, which speeds up the process of necessary maintenance.
Service maintenance requests from the original seller. While many supply chain and logistics companies may have existing relationships with localized technicians, it is vital to keep equipment operational. Servicing equipment from the original seller can save time and money.
Safety drives success. Never compromise on safety. It impacts everyone who uses the OEM’s products and services. Safe operation is the only option. To ensure safety, educate your operators. When purchasing from OEMs, take advantage of the instructors who have vast experience and knowledge of the products you’re purchasing or leasing. Allowing your operators to educate themselves on the assets they are handling will help them anticipate shortcomings.
The financial potholes from COVID-19 are far from over, but a bumpy road should not be a reason to panic and throw standard operating procedures out the window. Be proactive with your upgrades, don’t stray from best practices and you will find yourself better positioned when the economy returns to smoothly paved highway.