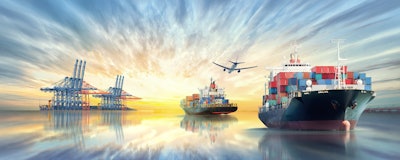
We’d all like to believe there is a quick fix to shield us from the type of supply chain disruption we’ve seen with the Coronavirus disease (COVID-19) pandemic. Unfortunately, there isn’t.
No single technology is going to immunize supply chains from disruption. But, there are recognized risk management approaches to take and collaborative capabilities that make the reengineering of a supply base more effective.
First, let’s consider why global supply chains deliver value, even if they may need to be adjusted for risks. Expecting large enterprises to abandon global supply chains and vertically integrate the process isn’t going to happen. There is way too much strategic value in global production capacity that has evolved over the last 20 years.
Initially, the draw for outsourcing production to emerging economies in Asia was huge, due to lower wage levels compared with North America. However, this early on comparative advantage has evolved into a competitive factor as Chinese contract manufacturers in sectors such as electronics have built up the domain expertise and advanced infrastructure, necessary to efficiently produce and ship modern, high-tech components and products.
Today, it’s not just the relatively lower wages that make Chinese manufacturers attractive, but their capabilities in areas like precision machining, tool and die, electronics manufacturing and electronics quality control. Other countries in Asia are similarly building these advantages. While single-sourcing critical components from Asia can be too big a risk in some cases, leveraging advanced manufacturing capacity from overseas is going to continue as global companies look to produce complex products in an economical way.
Diversification needs
The last few months, however, has reminded large, global original equipment manufacturers (OEMs) of the risks and costs of highly distributed supply chains. There have been significant disruptions before—such as the earthquake and tsunami that devastated parts of Japan in 2011. But, nothing has been on the scale and speed of COVID-19 disruption.
In a poll by the Institute of Supply Management (ISM), nearly 75% of companies reported some degree of supply chain disruption due to COVID-19-related restrictions, and more than 80% believe their organization will see COVID-19-related impacts. Analyst firms such as Gartner are advising that companies assess diversification of the supplier ecosystem and review or create a sound risk management program.
For certain, we’ve had a major wakeup call for the risks involved with extended global supply chains. OEMs will be taking a closer look at their supply chains for risk, paying special attention to single-sourced components or materials critical to their most profitable or strategic products. In some cases, it may be wise to build up buffer inventories for some critical components or establish secondary sources of supply, perhaps “onshore” or nearer to the U.S. market. It’s unrealistic, however, to think large OEMs will indiscriminately abandon advanced manufacturing capacity overseas.
There is a sensible path to supply chain resiliency. It will center on supply chain risk assessments, including a closer look at risks in the deeper tiers of each chain. This is more about methods and rigorous programs than it is about technology. But, once it becomes time to expand a supply base and start working with third-party engineering and manufacturing teams, collaboration capabilities play a vital role in increasing the speed and fidelity of the details involved in establishing new sources of supply.
Currently, much of the collaboration in the engineering and manufacturing world still consists of file-based systems that tether people to specialized software systems and costly, high-end workstations. This has given engineers some powerful tools to create, but collaboration is slow and serial in nature. The better way is using a cloud-based, software-as-a-service product development platform that allows engineers to simultaneous collaborate, design in real time and automatically keep an immutable, digital record of changes. Think Google Docs instead of the old “word processing” era when you kept files locally on a PC.
Speed and fidelity
When OEMs and suppliers can collaborate simultaneously without worrying about who has what file checked out, or whether the latest revision is being worked on, the iterative process involved in finding new suppliers speed up, with less errors and rework than in the past. Such collaborative capabilities, available on normal computing devices, is going to help companies adjust their supply chains in this era of heightened risks and more employees shifting to remote working arrangements.
The effort required in supply chain risk assessment and risk mitigation programs is substantial. It’s not a simple fix, but needs to be done. When it’s time to move forward with new suppliers, cloud-based collaboration will take much of the time and friction out of the process by allowing for rapid, concurrent engineering with a digital twin of revision processes and related product data. In short, we need systems that lend speed and fidelity to the many details that go into establishing alternative sources of supply.
We are going through some extraordinary times that require a combination of rigorous risk assessment and fresh approaches to collaboration. Some companies will look to near-shoring as a means of becoming more agile, but global supply chains will live on, adjusted and expanded for risk. Those companies that are able to move quickly to mitigate risks and secure quality alternative sources of supply are going to be at an advantage and thrive during future economic upheavals.