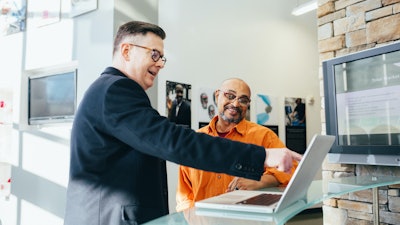
Countries around the world have been taking steps to control the spread of the Coronavirus disease (COVID-19). The world of work is no different – workers who were unable to go remote had no choice but to stay at home under income replacement arrangements.
The manufacturing industry as a whole has been severely impacted by the pandemic, with lockdowns persisting and assembly line workers forced to stay home to avoid further spread of the virus.
Now, conversations have evolved from business continuity and risk management, to getting employees and businesses back on track toward a more sustainable growth cycle. After all, things still have to be made, especially essential products, including medical devices and electrosurgical equipment, as well as personal protective equipment (PPE).
As part of a back-to-work program, business leaders have been focused on creating a safe workplace to protect their workforce.
Occupational safety and health (OSH) in the manufacturing industry is of paramount importance as the economy continues to recover, and technology is taking on a greater role to create and maintain workplace safety in manufacturing facilities that take into account risk assessment – physical as well as mental.
Technology’s role in protecting the workforce
A work environment is considered healthy if it promotes optimal levels of physical, mental and psychosocial well-being of all workers at all times. It also involves protecting workers from various foreseeable risks in their immediate environment.
During the pandemic, this means maintaining social distancing, consistent employee communication and robust data collection to power initiatives such as digital contact tracing. These are all new challenges that many manufacturing facilities are dealing with for the first time. What most managers will find is that ensuring all of these steps are taken on a consistent and reliable basis is impossible to do without the right technology in place.
Tech companies are quickly pivoting to come up with solutions that address the changing needs of frontline workers.
Challenging historically low employee engagement in manufacturing
On top of creating a safe place to work, technology can also help improve overall employee experience. According to a Gallup report on the state of the U.S. workplace, employees in the manufacturing industry have been the least engaged at work historically, with three-quarters of employees disengaged.
The industry has long lacked certain soft skills such as communication, trust and leadership – all of which have a sizeable impact on how employees feel about their place of work.
In a manufacturing facility, deskless workers can quickly become isolated and disengaged. The pandemic presents the perfect opportunity for this to change, and harnessing a device like the smartphone, in which 81% of Americans are in possession of, is making it a reality.
Mobile applications developed for employee communication and engagement, especially as it pertains to the deskless workforce, can act as a direct channel to the workforce where information, communication, and data is centralized.
To implement safety protocols to reduce the spread of the virus, daily health surveys can be integrated within these apps. Before starting their shift, workers are prompted to answer a set of COVID-19-related questions, which will decide whether or not they will be allowed to work that day.
Additionally, contact tracing apps can be incorporated into a workplace app to evaluate risk exposure. Wireless technology creates a digital trail of worker interaction, which can then be used to alert any employees of potential exposure to the virus.
Employee engagement is critical to any company’s success, especially during a pandemic. By connecting manufacturing employees and bringing them to the forefront of safety protocols, internal communication improves and trust is strengthened.
Safety must be factored into the equation
There has, understandably, been some push-back from privacy advocates, who fear tracking workers with artificial intelligence (AI) and wireless technologies is not always the best protocol and should not be used outside of the extreme pandemic case.
As always, data privacy regulations should be top of mind whenever implementing new strategies, even when it comes to safety. While innovations in technology make it possible for workplace communication platforms to achieve bank level data security features, cyber security really must be ingrained into company culture.
All employees, no matter their level, should have a basic understanding of what data they are allowed to access and share, and how do it in a safe and secure way.
A seamless and stress-free return to work
Making the process of returning to work with safety restrictions in place a hassle-free process for employees requires a robust process and continuous check-ins to ensure any new challenges or risks are swiftly planned for or eliminated.
Staggered shifts, social distancing and adequate sanitization are some of the proven safe workplace practices. However, to augment these, manufacturing companies should look to adopt a mobile intranet-like technology so that they can be better-connected to their workforce. Consistent communication during a pandemic has to be top priority, so that employees can adapt in tandem with the business as public health guidelines continue to evolve as the virus runs its course.