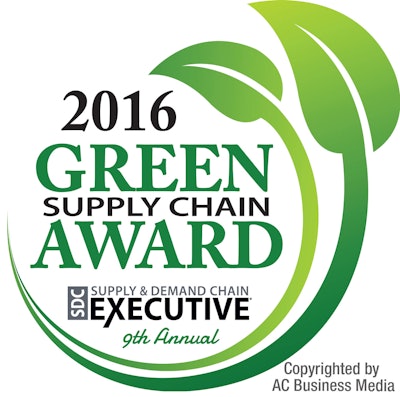
Supply & Demand Chain Executive has long taken the stance that being green and profitable are not mutually exclusive. In fact, many of the following companies are not only green-lighting successful sustainability initiatives, but also saving green in the process ...
3Gtms
The Most Efficient Way to Move Freight
3Gtms’ transportation management system (TMS) enables third-party logistics providers (3PLs) and logistics service providers (LSPs) to operate more sustainably through reducing fuel consumption and emissions during the transport of goods. The TMS incorporates optimization algorithms that help determine more efficient routes and ensure each route is maximized in terms of truck space. Clients report increased shipment consolidation, more efficient routes (and fewer miles traveled) and optimized truckloads. For instance, Bemis Manufacturing’s mix of freight changes drastically from day to day, so the company relies on 3Gtms’ TMS to help easily and quickly choose between all of its transportation options, and find the most efficient way to move freight.
ALOM
A Sustainable IT-Driven Strategy
ALOM worked with one of its medical device clients to design and implement a sustainable IT-driven strategy to expand its e-commerce-only order delivery protocol to include North American retail channel fulfillment to stores such as Target, CVS and Walgreens. ALOM engineered a proprietary order management process integrating retailer electronic data interchange (EDI) systems to receive orders by ALOM and feed them via application program interface (API) to the client for visibility. This solution improved the client’s sustainability by providing: paperless, real-time retail order management and tracking; reduced transportation time, cost and distance traveled per unit; a sustainable retail packaging design; and in-transit serial number tracking for automated delivery status notification. ALOM’s client saw a more than 40 percent reduction in per-unit transportation cost versus online fulfillment.
By the Numbers: ALOM’s client saw a more than 40 percent reduction in per-unit transportation cost versus online fulfillment.
Atlantix Global Systems
Greening End-of-Life or Surplus IT Equipment
Atlantix Global’s asset recovery services program maximizes the return on investment of a company’s end-of-life or surplus IT equipment, while also mitigating compliance risks when the equipment is refurbished, remarketed or recycled. The company believes that the most important aspect of asset recovery is the recycling process of end-of-life equipment. Its R2 standard certification—which focuses on the performance of electronics recyclers in environmental and public health, employee health and safety, security (data and facility), and the whole of the recycling process through final equipment disposition—confirms the company’s commitment to responsible recycling. Alantix customers see the results of green IT by reducing their footprint of electronic waste (e-waste), which is produced when electronic equipment is not properly disposed.
B-Stock Solutions
Liquidation Marketplace Diverts Hard-to-Sell Items from Landfills
B-Stock Solutions operates a large network of business-to-business (B2B) liquidation and wholesale online auction marketplaces. By ditching the practice of landfilling excess, obsolete and returned product and replacing it with a more sustainable B2B liquidation marketplace—for inventory of all conditions—B-Stock’s clients enabled the recycling, repurposing, reuse or resale of just under 70 million items through a total of 137,473 auctions to date. In the past 18 months alone, 45 million items were sold for reuse, resale or recycling. As an example, B-Stock worked with a large cellphone buyback company to build a B2B solution for its collected inventory, so it could auction off bulk quantities of merchandise directly to a qualified buyer base. The organization successfully sold 136,835 devices through 4,205 auctions.
By the Numbers: B-Stock’s clients enabled the recycling, repurposing, reuse or resale of just under 70 million items through a total of 137,473 auctions to date.
BLG Logistics Inc.
Green Is a Commitment to Customers and Society
For BLG Logistics, green is not new. It is a commitment to its customers and society. The company takes responsibility for sustainability of local operations, and its effect on regional markets and the environments in which it operates all over the world, although specific actions and initiatives vary by office. BLG Logistics, a provider of logistics services for the automotive industry, not only supplies parts for just-in-sequence and just-in-time production, but is also a major distributor of finished vehicles. Overall, the company reduced fresh water requirements per car wash by 85 percent. It employs smart systems that provide energy only when needed, while focusing on smart technology to recover and restore energy.
By the Numbers: BLG Logistics reduced fresh water requirements per car wash by 85 percent.
CaseStack
Consolidation Protects Suppliers’ Resources
CaseStack's Retailer Consolidation Program protects suppliers’ resources by: providing proportional full truckload pricing instead of costly less-than-truckload (LTL) rates, boosting on-time performance, maximizing in-stock rates, limiting the potential for damages/shortages and lowering total logistics costs. Consolidation programs help conserve natural resources by reducing dock congestion, improving warehouse efficiencies and decreasing the number of trucks on the highway. The resulting supply chain consumes less energy and produces lower amounts of carbon emissions. Fewer trucks on the road results in fewer interactions with motorists and safer highways. CaseStack’s retailer partners experience: increased supplier price competition, increased inventory turns, lower order minimums, decreased safety stock levels, decreased inventory costs, increased efficiency, decreased vendor management time and costs, decreased dock congestion and decreased lead times.
Cass Information Systems Inc.
Digitizing and Reducing the Paper Chain
Cass Information Systems helps customers meet green supply chain goals by accelerating the amount of electronic interchange between Cass, customers and their freight carriers. Cass eliminates the use of paper by: averaging an annual EDI freight invoice percentage of over 75 percent; receiving electronic carrier invoices; accepting electronic shipment documentation from customers and carriers; imaging all documents and making them available online; digitizing customers’ transportation tariff and rate information; and posting customer routing instructions online for carriers. In fact, over 99 percent of Cass payments and remittance advice to carriers are electronic. Business intelligence also provides information for shipment optimization, such as consolidating shipments, reducing unnecessary expedited shipments, route optimization, or planning for optimum warehouse and distribution locations.
By the Numbers: Over 99 percent of Cass payments and remittance advice to carriers are electronic.
Celestica Inc.
A 94 Percent Carbon Footprint Reduction
Celestica receives, inspects, refurbishes, remanufactures, repairs, configures and redistributes products to maximize the value of customers’ returns. The company’s knowledge of product-level environmental legislation requirements and parts harvesting also help to maximize the value of products received as returns, thereby diverting good products from landfills. One of Celestica’s customers sought to reduce the cost of its operations by consolidating repair from more than eight sites to one, while providing in-region repair depots capable of triaging product. Celestica created three regional repair facilities, which were managed by a control tower that monitored event management and visibility for the entire network. Approximately 50 percent total savings were delivered to the customer by eliminating more than 30 transportation routes—equating to a 94 percent carbon footprint reduction.
By the Numbers: Celestica delivered approximately 50 percent in total saving to its customer by eliminating more than 30 transportation routes—equating to a 94 percent carbon footprint reduction.
DSC Logistics
Reducing Trucks on the Road and Miles Traveled
DSC Logistics’ Sustainability Committee oversees support for pilot projects and network-wide rollouts, sustainability education, and metrics and benchmarking efforts. The company tracks sustainability on six metrics—electricity, natural gas, water, propane, recycling and waste tonnage—across more than 40 locations. Consolidated shipping, its SmartWay certification and a strict no-idle policy are three of the primary components of DSC’s transportation-focused sustainability efforts. By consolidating multiple customers with a single destination onto a shared truck, the company can reduce trucks on the road and miles traveled. DSC's yearly goals include further waste stream reductions, implementation of lean initiatives focusing on reducing process steps and waste in the supply chain, and using strategic supply chain modeling to reduce logistics center footprints.
By the Numbers: DSC Logistics tracks sustainability on six metrics—electricity, natural gas, water, propane, recycling and waste tonnage—across more than 40 locations.
DW Morgan Company
Reducing Trips through Synchronized Routing
Before DW Morgan Company optimized ground movement for a major original equipment manufacturer (OEM) client in Malaysia, the flow of goods was managed by 11 different partners, requiring 51 one-way trips per day and resulting in 704 empty truck kilometers. The company created and managed synchronized routing that now only requires 37 trips per day (a 27 percent improvement) and reduced empty kilometers by 36 percent, while creating new backhaul opportunities. In another case, a client used Inventory On Demand to have DW Morgan take ownership of goods at origin in Asia. Through its active management, DW Morgan reduced overall inventory by 30 percent, decreased transportation by 35 percent and eliminated the highest urgency, most carbon-intensive expedited shipments.
By the Numbers: DW Morgan reduced overall inventory by 30 percent, decreased transportation by 35 percent and eliminated the highest urgency, most carbon-intensive expedited shipments.
EcoVadis S.A.
Sustainability Ratings and Performance Improvement Tools
EcoVadis is a collaborative platform that provides sustainability ratings and performance improvement tools for global supply chains. The EcoVadis methodology, which covers 150 spend categories and 140 countries, is at the core of its corporate social responsibility (CSR) analysis system, which covers 21 criteria across four themes, including environment, fair labor practices, ethics/fair business practices and supply chain. Over 70 percent of participating companies improve their CSR performance score upon re-evaluation. Furthermore, the network’s scorecard-sharing capability is accelerating transparency. However, each of the company’s more than 30,000 customers—whether buyer or supplier—has their own sustainability story on how they are using EcoVadis.
By the Numbers: Over 70 percent of companies using the EcoVadis platform improve their corporate social responsibility performance score upon re-evaluation.
Elemica
Eliminating the Wasteful Idling of Trucks and More
Elemica provides cloud-based supply chain integration solutions that enable customers to collaborate with trading partners to procure, sell, and distribute their products more efficiently. By using the company’s integrated logistics and transportation products, customers lowered their carbon footprints and energy usage by optimizing shipments and loads. Additionally, Elemica’s Road Solution permits companies to book slots/appointments for arrivals or departures, ensuring the right team and equipment are at the dock when necessary, eliminating the wasteful idling of trucks. Meanwhile, the company’s Supplier Information Management solution helps manage suppliers’ credentials and track compliance, including sustainability requirements. Since 2004, Elemica has delivered approximately 200 million messages, equating to savings of 2,000 cubic meters of landfill space, 22,000,000 liters of water used in paper production, 21,500 trees and 245,000 kilograms of CO2 emissions.
By the Numbers: Since 2004, Elemica has delivered approximately 200 million messages, equating to savings of 2,000 cubic meters of landfill space, 22,000,000 liters of water used in paper production, 21,500 trees and 245,000 kilograms of CO2 emissions.
FoodLogiQ
Supplier Sustainability Rating System
When Whole Foods Market set out to launch a sustainability rating system—Responsibly Grown—for its suppliers, the company turned to FoodLogiQ to build it. Within the program, prospective suppliers seek approval by entering data about their products, supply chain and certifications into the Whole Foods supplier portal using FoodLogiQ’s software. Once the vendors are approved, the system surveys them on Whole Food’s standards around growing practices, pesticide use and waste management, among other things, and then qualifies them for the Responsibly Grown listing. Whole Foods stores, in turn, print labels with the designation and place them on signage by the products. Whole Foods launched Responsibly Grown by rating hundreds of products with key suppliers, representing more than 50 percent of produce nationwide.
By the Numbers: Whole Foods launched Responsibly Grown by rating hundreds of products with key suppliers, representing more than 50 percent of produce nationwide.
HighJump
Attacking Inefficiency through Myriad Greenworthy Products
The HighJump warehouse management system (WMS) enables customers to reduce their paper needs, as well as better control product flows and optimize product movements, which saves energy. HighJump Retail Advantage helps omnichannel customers make better decisions about getting a product to the customer—whether by shipping, delivery or in-store pickup—by quickly determining the most efficient method of fulfilling a customer’s order, which saves fuel costs and energy resources. Meanwhile, HighJump Transportation Management implements route planning, mode selection and carrier choice to enable companies to reduce their carbon footprints. HighJump Container Advantage, in contrast, optimizes containerization by selecting the proper carton size for the best item arrangement, cutting the material used in packing.
ModusLink Global Solutions
Sustainability Comes in Different Packages
A major electronics firm challenged ModusLink to identify ways to reduce its greenhouse gas (GHG) emissions and redesign its product packaging using sustainable materials. With ModusLink’s team of engineers analyzing the amount of GHG emissions resulting from various packaging types, then redesigning the packaging, the customer was able to realize savings of more than $350,000 in packaging materials by eliminating 74,000 cubic feet or 88,000 pounds of packaging. In another case, a global consumer electronics firm worked with ModusLink to reduce packaging material costs and increase the logistics efficiency of the packaging. Ultimately, ModusLink helped the client cut paper, fiber and plastic use by 50 percent; reduce shipping costs by 45 percent; and increase pallet density by 157 percent, on average.
By the Numbers: ModusLink’s customer was able to realize savings of more than $350,000 in packaging materials, while eliminating 74,000 cubic feet or 88,000 pounds of packaging.
NeoGrid
Big Supporter of Sustainable IT Processes
NeoGrid provides solutions which, by their nature, contribute to the sustainability of the supply chain by curtailing paper waste through the use of EDI. Furthermore, NeoGrid solutions are operated in the cloud, which saves energy because the thousands of companies that interact with one another through these solutions are able to use the same solution at the same time without the need to have a server on each site. Through the use of virtual servers, NeoGrid is able to reduce energy consumption in its data center by 80 percent. Additionally, in 2013, NeoGrid is proud to have saved 350 tons of paper—the equivalent of about 4,000 trees. These kinds of savings are significant because they also reduce carbon dioxide (CO2) emissions and landfill pollution.
By the Numbers: Through the use of virtual servers, NeoGrid is able to reduce energy consumption in its data center by 80 percent.
Performance Team
Transloading Translates into a Carbon Reduction of 30 Percent
In the past five years, Performance Team transloaded over 250,000 containers using a 3:2 compression standard that translated into approximately 167,000 outbound trailers and a carbon reduction footprint of 30 percent. As of the first quarter of 2016, the company’s fleet was 100 percent updated with EPA SmartWay-approved tires to improve fuel efficiency and performance, while continuing to use SmartWay-certified hybrid trailer skirts on trailers and under trays. This equipment has an estimated fuel efficiency improvement of 4 to 5 percent in California and 6 to 7 percent outside of California. Moreover, Performance Team is installing solar panels for selected facilities in its network, as well as switching from metal-halide lights to energy-saving T-5 florescent fixtures in all of its facilities.
By the Numbers: Performance Team transloaded over 250,000 containers using a 3:2 compression standard that translated into a carbon reduction footprint of 30 percent.
Port Everglades, a Department of Broward County
LEED Certification for Green Improvements
Port Everglades employs clean technologies, such as clean-diesel engines and generators, embraces progressive regulations, hosts community/customer awareness programs, and actively fosters green partnerships. The port also continues to implement green infrastructure, including remote sensors for energy management and stormwater runoff controls. Port Everglades received its first Leadership in Energy and Environmental Design (LEED) certification for green improvements to a terminal, which included the implementation of: recycled concrete and asphalt in construction; low-flow toilets and fixtures; energy-efficient interior lighting; parking lot lights powered by wind turbines and solar panels; natural lighting; energy-efficient air conditioning filters and CO2 monitors; remote control lighting and air systems tied to occupancy sensors; regional materials manufactured within 500 miles of the port; and low volatile-organic-compound products.
ProShip Inc.
Reduce Shipping Volumes by up to 50 Percent
ProShip’s CVP-500 fit-to-size packing system automates all steps of package fulfillment for single- and multi-item orders with variable dimensions. As soon as an order is picked, the CVP-500 builds, fills, folds and labels each parcel in one process. Compared to standard cardboard boxes, the CVP-500 can save up to 20 percent on corrugated and eliminates unnecessary void fill by creating a perfect fit around items being shipped. Furthermore, fit-to-size packaging can reduce shipping volumes by up to 50 percent. When Lasaulec, a seller of maintenance, repair and operating supplies, decided to centralize all its logistics activities out of one automated warehouse, it realized it had to handle 300,000 items in a variety of sizes. Lasaulec implemented the CVP-500 and now expects to save €150,000 to €250,000 per year on void fill material.
By the Numbers: Lasaulec implemented ProShip’s CVP-500 and now expects to save €150,000 to €250,000 per year on void fill material.
Other Green Award Winners:
4flow AG | www.4flow.com |
A. Duie Pyle | www.aduiepyle.com |
AFN Logistics | www.LoadAFN.com |
AFS Technologies | www.afsi.com |
American Global Logistics | www.americangloballogistics.com |
APL Logistics | www.apllogistics.com |
ArrowStream | www.arrowstream.com |
Avendra LLC | www.avendra.com |
Cargo Chief | www.cargochief.com |
CBX Software | www.cbxsoftware.com |
Chainalytics | www.chainalytics.com |
Cisco Systems | www.cisco.com/c/en_sg/index.html |
Cloud Logistics | www.gocloudlogistics.com |
Comerica Inc. | www.comerica.com |
Crown Equipment Corporation | www.crown.com |
DMW&H | www.dmwandh.com |
Echo Global Logistics | www.echo.com |
enVista | www.envistacorp.com |
HAVI | www.havi.com |
Inmar | www.inmar.com |
International Asset Systems (IAS) | www.interasset.com |
John Galt Solutions | www.johngalt.com |
Kenco Logisctics | www.kencogroup.com |
LF Beauty (Thailand) Limited | www.lifung.com |
LOG-NET Inc. | www.LOG-NET.com |
MatchBack System Inc. | www.matchbacksystems.com |
Method Home | www.methodhome.com |
Murphy Warehouse Company | www.murphywarehouse.com |
Paragon Software Systems | www.paragontruckrouting.com |
Penske Logsitics LLC | www.PenskeLogistics.com |
Reverse Recycling Inc. | www.reverserecycling.com |
Rubicon Global | www.rubiconglobal.com |
Ryder | www.ryder.com |
Saddle Creek Logistics Services | www.sclogistics.com |
Schenker Inc. | www.dbschenker.com |
Security Technologies Inc. | www.sectechinc.com |
Smith Corona | www.smithcorona.com |
Source One Management Services | www.sourceoneinc.com |
Spinnaker | www.spinnakerMGMT.com |
Steelwedge | www.steelwedge.om |
Stryker's Sustainability Solutions | www.sustainability.stryker.com/ |
Supply Chain Optimizers, LLC | www.supplychainoptimizers.com |
SYSPRO | www.syspro.com |
Thomson Terminals Limited | www.thomsongroup.com |
ToolsGroup | www.ToolsGroup.com |
Tyco Retail Solutions | www.tycoretailsolutions.com |
UNEX Manufacturing | www.unex.com |
VAI | www.vai.net |
Westfalia Technologies Inc. | www.westfaliausa.com |
Yale Materials Handling Corporation | www.yale.com/north-america/en-us |